Physical Vapor Deposition (PVD) is a versatile vacuum-based coating technology used to deposit thin films and coatings on various substrates. It is widely employed across industries for its ability to enhance material properties such as hardness, wear resistance, oxidation resistance, and friction reduction. PVD is used in applications ranging from decorative coatings in consumer goods to functional coatings in automotive, semiconductor, and industrial manufacturing. The process involves vaporizing a solid material and depositing it onto a substrate, often with the addition of reactive gases to achieve specific properties. PVD coatings are valued for their durability, precision, and ability to meet demanding performance requirements.
Key Points Explained:
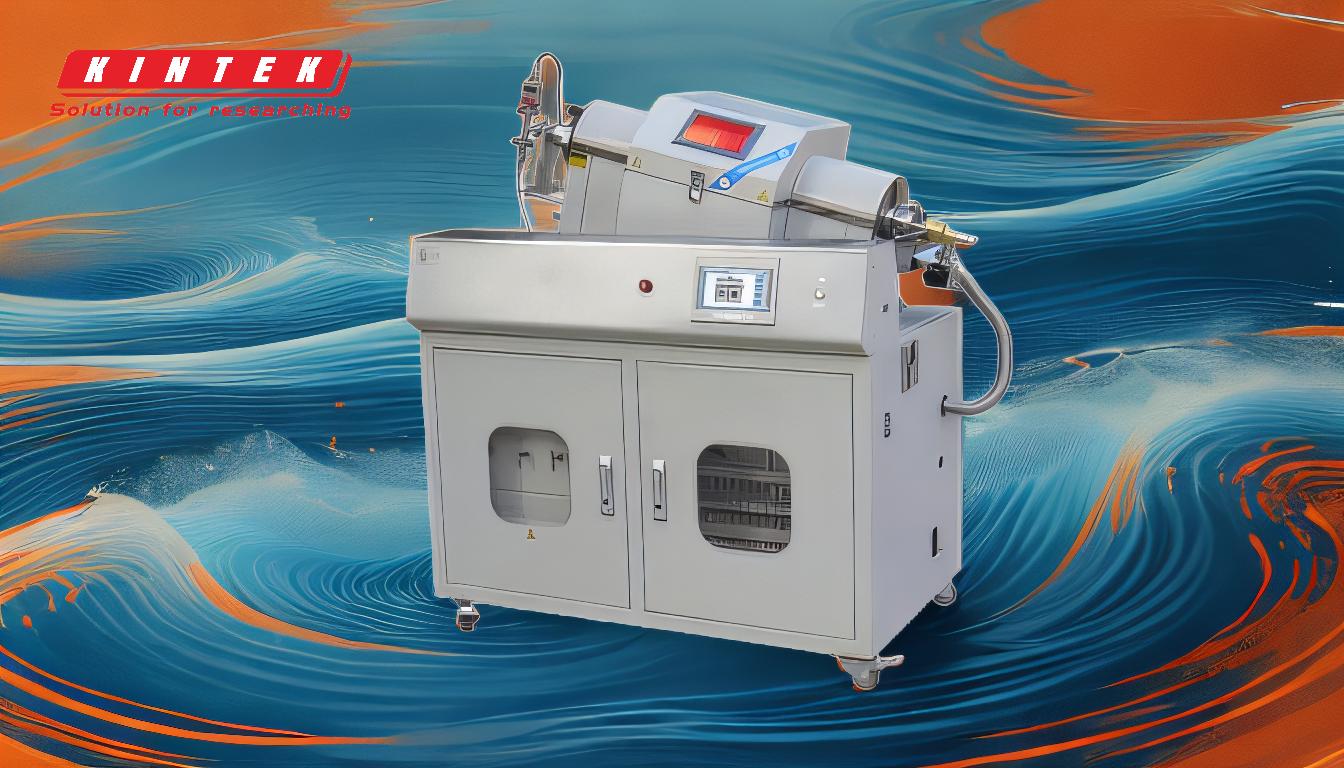
-
Overview of PVD Technology:
- PVD is a family of vacuum deposition methods that transform material from a solid phase to a vapor and then back to a solid film on a substrate.
- Common PVD techniques include sputtering and evaporation, which are conducted under vacuum conditions to ensure high-quality coatings.
- The process involves bombarding a solid precursor material with energy (e.g., electron beams) to release atoms, which then deposit onto the substrate.
-
Functional Benefits of PVD Coatings:
- Reduced Friction: PVD coatings are used to minimize friction in moving parts, enhancing efficiency and longevity.
- Improved Hardness: Coatings increase the surface hardness of substrates, making them more resistant to wear and deformation.
- Oxidation Resistance: PVD coatings protect materials from oxidation and corrosion, especially in high-temperature or harsh environments.
- Tribological Properties: PVD is used to create coatings that improve wear resistance, making it ideal for cutting tools, forming tools, and industrial machinery.
-
Applications in Consumer Goods:
- PVD is used to add aesthetic and functional value to products like jewelry, watches, and promotional items.
- It provides durable, high-quality finishes with vibrant colors, enhancing the appeal and longevity of consumer goods.
-
Role in Semiconductor Manufacturing:
- PVD, particularly sputtering, is critical in producing microchips and thin-film photovoltaic cells.
- Metals like platinum, tungsten, and copper are deposited in multilayered structures for microchips.
- For photovoltaic cells, materials such as copper, indium, gallium, and tellurium are coated onto glass or plastic substrates to improve efficiency.
-
Automotive Industry Applications:
- PVD coatings improve the durability and performance of engine components.
- They are also used for decorative purposes, giving auto and motorcycle interiors and trim a high-end, durable finish.
-
Decorative and Industrial Coatings:
- PVD is widely used for decorative coatings on products like door and window hardware, kitchen and bathroom fixtures, and marine supplies.
- It is also applied in industrial settings to enhance the performance of tools and components, such as cutting and forming tools.
-
Innovative and Emerging Applications:
- PVD is being explored in new markets for innovative applications, such as coating glass surfaces for thermo-optical properties.
- The technology is continuously evolving to meet the demands of advanced materials and industries.
In summary, PVD is a critical technology for enhancing the performance, durability, and aesthetics of materials across a wide range of industries. Its ability to create precise, high-quality coatings makes it indispensable in modern manufacturing and design.
Summary Table:
Application | Key Benefits |
---|---|
Consumer Goods | Aesthetic finishes, vibrant colors, and enhanced durability for jewelry, watches, and promotional items. |
Semiconductor Manufacturing | Deposits metals like platinum, tungsten, and copper for microchips and photovoltaic cells. |
Automotive Industry | Improves engine component durability and provides high-end decorative finishes. |
Industrial Coatings | Enhances wear resistance for cutting tools, forming tools, and machinery. |
Emerging Applications | Explores thermo-optical properties for glass coatings and advanced materials. |
Learn how PVD coatings can transform your products—contact our experts today!