A retort furnace is a specialized type of furnace designed for heat treatment processes, particularly those requiring controlled atmospheres. It features a cylindrical metal retort where materials are suspended, allowing for precise temperature and atmosphere control. This furnace is widely used in industries such as ceramics, metallurgy, electronics, and chemical processing for applications like carburizing, nitriding, sintering, and annealing. Its design ensures quicker heating, improved operating conditions, and reduced fuel consumption, making it a valuable tool in high-temperature material processing.
Key Points Explained:
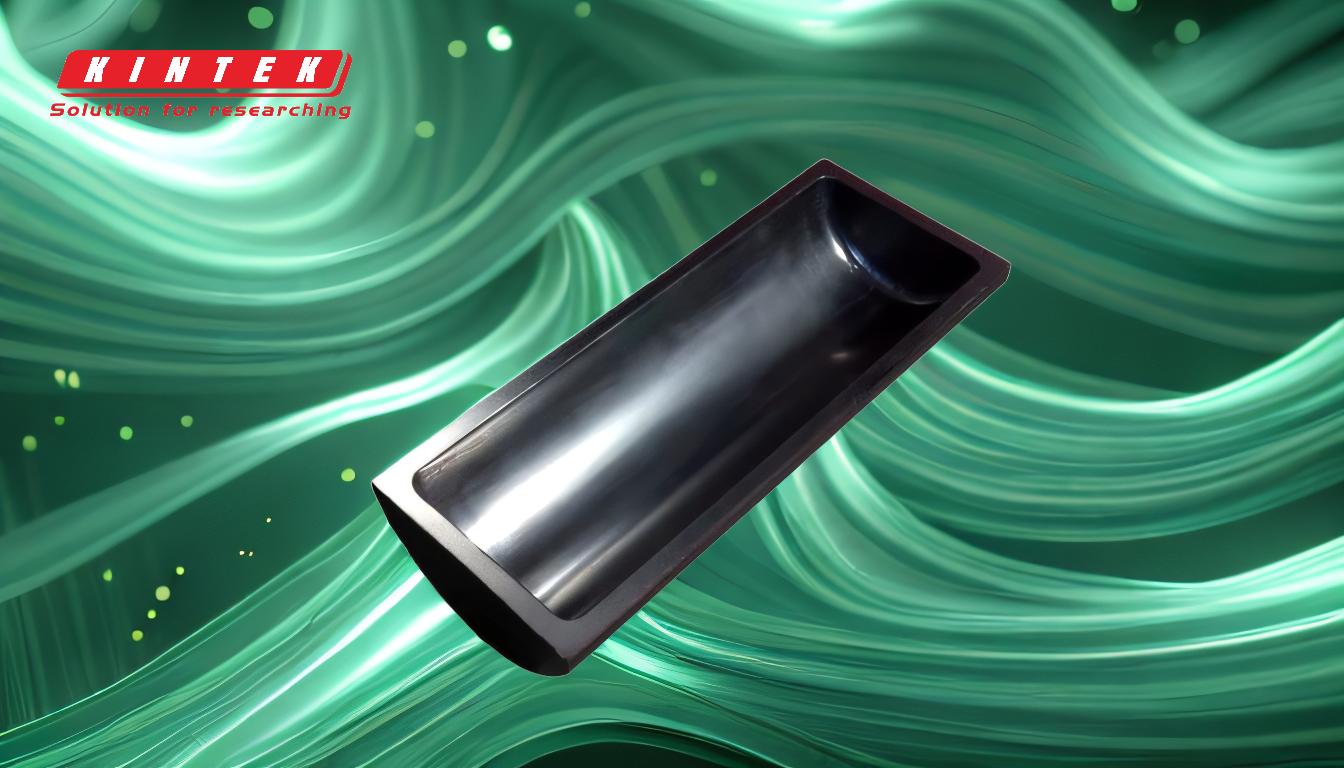
-
Definition and Structure of a Retort Furnace
- A retort furnace is a vertical furnace equipped with a cylindrical metal retort. The retort serves as a sealed chamber where materials are placed for heat treatment.
- The retort allows for the introduction of special gas atmospheres, which are essential for processes like carburizing (adding carbon to metal surfaces) and nitriding (adding nitrogen to metal surfaces).
-
Applications of Retort Furnaces
- Retort furnaces are used in a wide range of industries, including ceramics, metallurgy, electronics, glass, and chemical processing.
- Specific applications include:
- Powder roasting and ceramic sintering.
- High-temperature experiments and material treatment.
- Annealing, sintering, and flue gas treatment.
- They are also utilized in research institutions and universities for advanced material studies.
-
Advantages of Retort Furnaces
- Quicker Heating Times: The design ensures efficient heat transfer, reducing processing time.
- Improved Operating Conditions: The sealed retort minimizes exposure to external contaminants, ensuring cleaner processing environments.
- Reduced Fuel Consumption: The efficient design lowers energy usage, making it cost-effective.
-
Components and Functionality
- Retort: The central chamber where materials are placed and treated under controlled atmospheres.
- Heating Elements: Typically made of graphite, ceramics, or metals, these elements provide the necessary heat.
- Temperature Control System: Ensures precise temperature regulation for consistent results.
- Atmosphere Control: Allows for the introduction of gases like nitrogen or carbon-rich atmospheres for specialized treatments.
-
Comparison with Other Furnace Types
- Unlike a muffle furnace, which is used for processes like alkali fusion and organic material decomposition, a retort furnace is specifically designed for atmosphere-controlled heat treatment.
- Compared to a vacuum furnace, which operates under a vacuum environment, a retort furnace uses gas atmospheres for specific material treatments.
-
Industrial Significance
- Retort furnaces are critical in industries requiring precise heat treatment under controlled conditions.
- They are particularly valuable in the production of advanced materials, where consistent quality and performance are essential.
By understanding the design, functionality, and applications of a retort furnace, industries can leverage its capabilities to achieve superior material processing results.
Summary Table:
Aspect | Details |
---|---|
Definition | A vertical furnace with a cylindrical metal retort for controlled heat treatment. |
Applications | Carburizing, nitriding, sintering, annealing, and advanced material studies. |
Industries | Ceramics, metallurgy, electronics, glass, and chemical processing. |
Advantages | Quicker heating, improved operating conditions, and reduced fuel consumption. |
Key Components | Retort, heating elements, temperature control system, and atmosphere control. |
Discover how a retort furnace can optimize your heat treatment processes—contact us today!