A retort in heat treatment refers to a specialized furnace or vessel designed for controlled heating processes, often used in industrial applications such as metal treatment, food sterilization, and chemical reactions. In the context of heat treatment, retort furnaces are vertical systems that allow precise movement of the load between different temperature zones, such as a hot chamber for heating and a fast cooling chamber for quenching. These furnaces are airtight, ensuring controlled atmospheres for processes like annealing, tempering, or case hardening. Retorts are also used in other industries, such as food processing (e.g., canning retorts for sterilization) and chemistry (e.g., distillation retorts), highlighting their versatility in handling high-temperature processes under controlled conditions.
Key Points Explained:
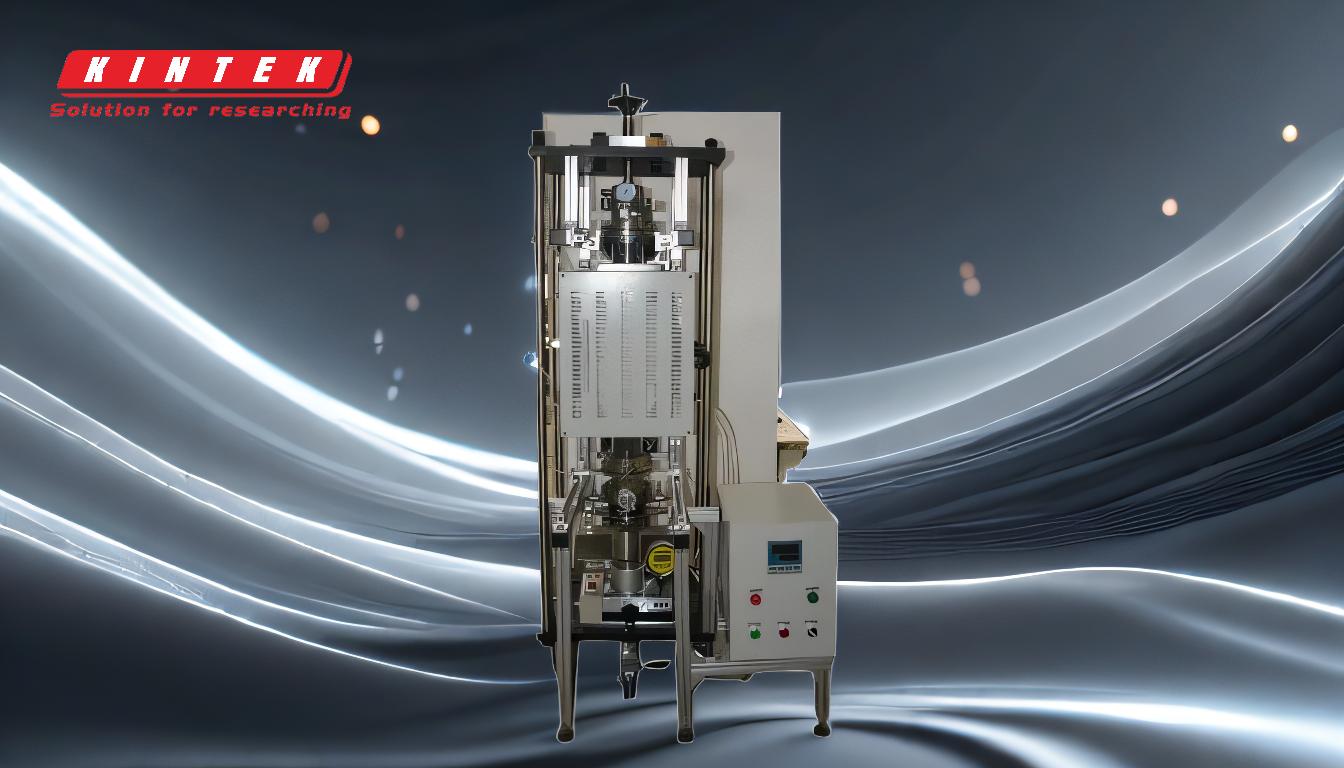
-
Definition of a Retort in Heat Treatment:
- A retort in heat treatment is an airtight vessel or furnace designed for controlled heating and cooling processes. It is commonly used in industrial applications to treat materials like metals, ensuring precise temperature control and uniform heat distribution.
-
Structure and Function of Retort Heat Treatment Furnaces:
- Retort furnaces are vertical systems with multiple chambers, typically including:
- A hot chamber for heating the load to the desired temperature.
- A fast cooling chamber for rapid quenching or cooling after heat treatment.
- The load is moved vertically between these chambers, allowing for efficient and controlled processing.
- Retort furnaces are vertical systems with multiple chambers, typically including:
-
Applications of Retort Heat Treatment:
- Retort furnaces are widely used in:
- Metal Treatment: Processes like annealing, tempering, and case hardening require precise temperature control, which retort furnaces provide.
- Food Industry: Canning retorts are used for sterilization under high temperatures (116–130 °C), ensuring food safety and preservation.
- Chemical Industry: Retorts are used for distillation, pyrolysis, and other high-temperature chemical reactions.
- Retort furnaces are widely used in:
-
Advantages of Retort Heat Treatment:
- Controlled Atmosphere: The airtight design allows for the use of inert gases or vacuum conditions, preventing oxidation or contamination.
- Uniform Heating: Vertical movement ensures even heat distribution, critical for consistent material properties.
- Efficiency: The ability to rapidly move between heating and cooling chambers reduces processing time and energy consumption.
-
Comparison with Other Retort Applications:
- While retort heat treatment furnaces are primarily used for material processing, retorts in other industries serve different purposes:
- Food Industry: Canning retorts focus on sterilization and preservation.
- Chemical Industry: Laboratory retorts are used for distillation or dry distillation of substances.
- Industrial Processes: Retorts are used in shale oil extraction, charcoal production, and mercury recovery.
- While retort heat treatment furnaces are primarily used for material processing, retorts in other industries serve different purposes:
-
Key Considerations for Purchasing a Retort Heat Treatment Furnace:
- When selecting a retort furnace, consider:
- Temperature Range: Ensure the furnace can achieve the required temperatures for your specific application.
- Atmosphere Control: Look for features like gas purging or vacuum capabilities.
- Load Capacity: Choose a furnace size that accommodates your typical load dimensions and weight.
- Cooling Rate: Evaluate the cooling chamber's efficiency for processes requiring rapid quenching.
- Energy Efficiency: Opt for designs that minimize energy consumption and operational costs.
- When selecting a retort furnace, consider:
In summary, a retort in heat treatment is a versatile and essential tool for industries requiring precise and controlled high-temperature processes. Its design and functionality make it suitable for a wide range of applications, from metal treatment to food sterilization, ensuring consistent and reliable results.
Summary Table:
Key Aspect | Details |
---|---|
Definition | Airtight vessel for controlled heating and cooling processes. |
Structure | Vertical system with hot and fast cooling chambers. |
Applications | Metal treatment, food sterilization, chemical reactions. |
Advantages | Controlled atmosphere, uniform heating, energy efficiency. |
Key Considerations | Temperature range, atmosphere control, load capacity, cooling rate, energy efficiency. |
Ready to enhance your heat treatment processes? Contact us today for expert advice on retort furnaces!