A sinter furnace, also known as a sintering furnace, is a specialized piece of equipment used in the sintering process, which involves compacting loose materials into a solid mass by applying heat and pressure below the material's melting point. This process reduces porosity and improves density, making it essential in industries like manufacturing, dentistry, and ceramics. Sintering furnaces come in various types, such as vacuum, hydrogen, and hot press furnaces, each designed for specific applications. They consist of key components like heating elements, vacuum systems, temperature control mechanisms, and cooling systems, ensuring precise and efficient sintering. The versatility and cost-effectiveness of sintering make it a widely adopted process for producing high-quality components.
Key Points Explained:
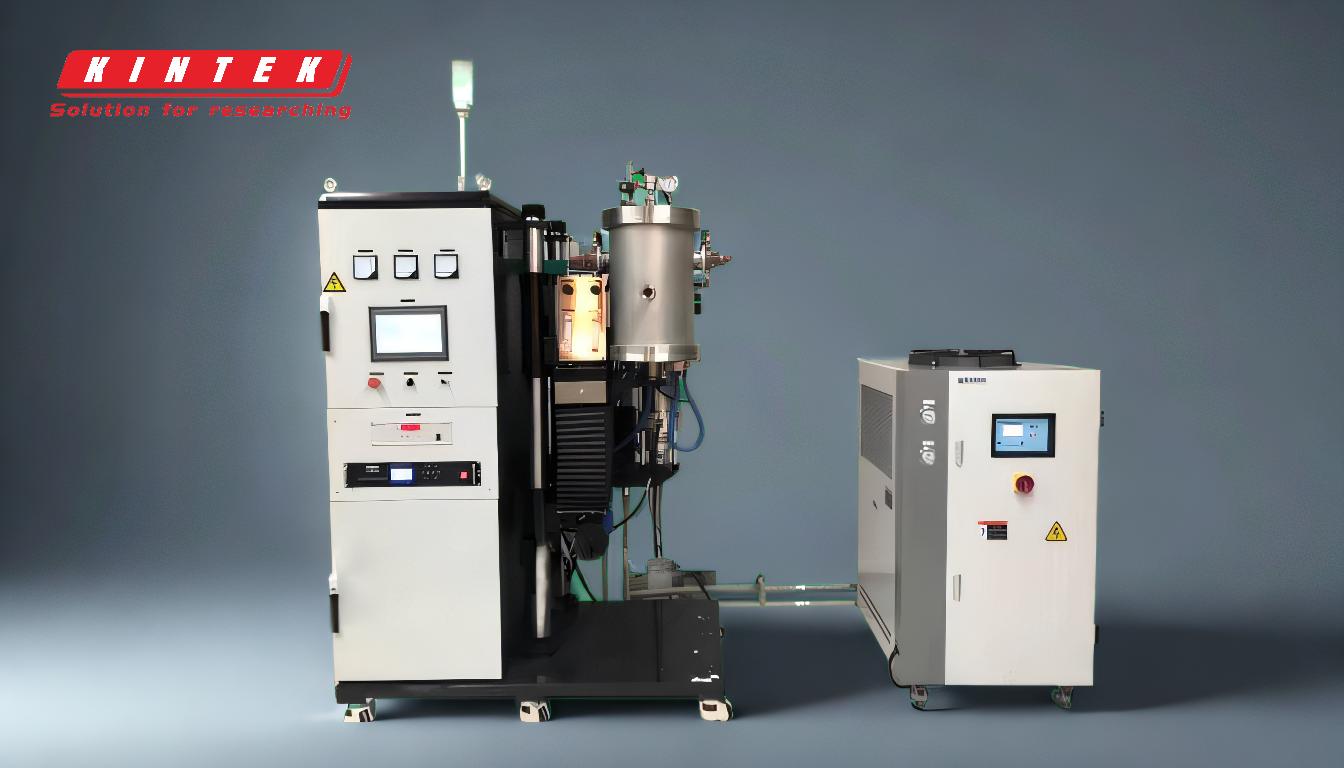
-
What is a Sinter Furnace?
- A sintering furnace is a device used to sinter materials, which involves compacting loose particles into a solid mass by applying heat and pressure below the material's melting point. This process reduces porosity and enhances the material's density and strength.
-
Key Components of a Sinter Furnace
- Vacuum Chamber: Designed to withstand high temperatures and vacuum conditions, it ensures a controlled environment for sintering.
- Heating Elements: Provide the high temperatures required for sintering.
- Vacuum Pumps: Create and maintain the vacuum environment.
- Temperature Control Systems: Manage the heating and cooling rates to ensure precise sintering.
- Charging System: Used for loading and unloading materials.
- Cooling System: Cools the furnace shell and vacuum pump to maintain operational efficiency.
-
Types of Sinter Furnaces
- Vacuum Sintering Furnace: Uses a vacuum environment to prevent oxidation and contamination during sintering.
- Hydrogen Sintering Furnace: Utilizes hydrogen as a reducing atmosphere to achieve high-density sintering.
- Hot Press Sintering Furnace: Combines high temperature and pressure in a vacuum environment to sinter materials, often used for ceramics.
-
Applications of Sinter Furnaces
- Dental Industry: Used to sinter zirconia for dental restorations like crowns and bridges, achieving the required hardness and density.
- Manufacturing: Produces components such as gears, bearings, and electrical contacts with improved mechanical properties.
- Ceramics: Sinters ceramic powders into solid materials with high strength and density.
-
The Sintering Process
- Loading: Materials are loaded into the furnace.
- Evacuation: The furnace is evacuated to create a vacuum or controlled atmosphere.
- Heating: Materials are heated to the sintering temperature.
- Pressure Application: In hot press sintering, pressure is applied to compact the material.
- Cooling: The sintered material is cooled to room temperature.
-
Advantages of Sintering
- Cost-Effective: Reduces material waste and energy consumption.
- Versatile: Applicable to a wide range of materials and industries.
- Improved Properties: Enhances the density, strength, and durability of materials.
By understanding the components, types, and applications of sintering furnaces, purchasers can make informed decisions based on their specific needs and requirements.
Summary Table:
Aspect | Details |
---|---|
Definition | A device that compacts loose materials into solid masses using heat and pressure. |
Key Components | Vacuum chamber, heating elements, vacuum pumps, temperature control, cooling systems. |
Types | Vacuum, hydrogen, and hot press sintering furnaces. |
Applications | Dental restorations, manufacturing components, ceramic sintering. |
Advantages | Cost-effective, versatile, improves material density and strength. |
Looking for the right sinter furnace for your needs? Contact us today to learn more!