Sintering is a critical process in material science and manufacturing, where powdered materials are compacted and heated to form a solid mass without reaching the material's melting point. This process is widely used across various industries to produce components like gears, bearings, and electrical contacts. A sintering furnace is the specialized equipment used to carry out this process. It operates by applying heat and, in some cases, pressure to facilitate atomic diffusion, which bonds the powder particles together. Different types of sintering furnaces, such as hot press sintering furnaces, vacuum sintering furnaces, and atmosphere sintering furnaces, are designed to meet specific industrial needs. These furnaces are equipped with components like vacuum chambers, heating elements, and temperature control systems to ensure precise and efficient sintering.
Key Points Explained:
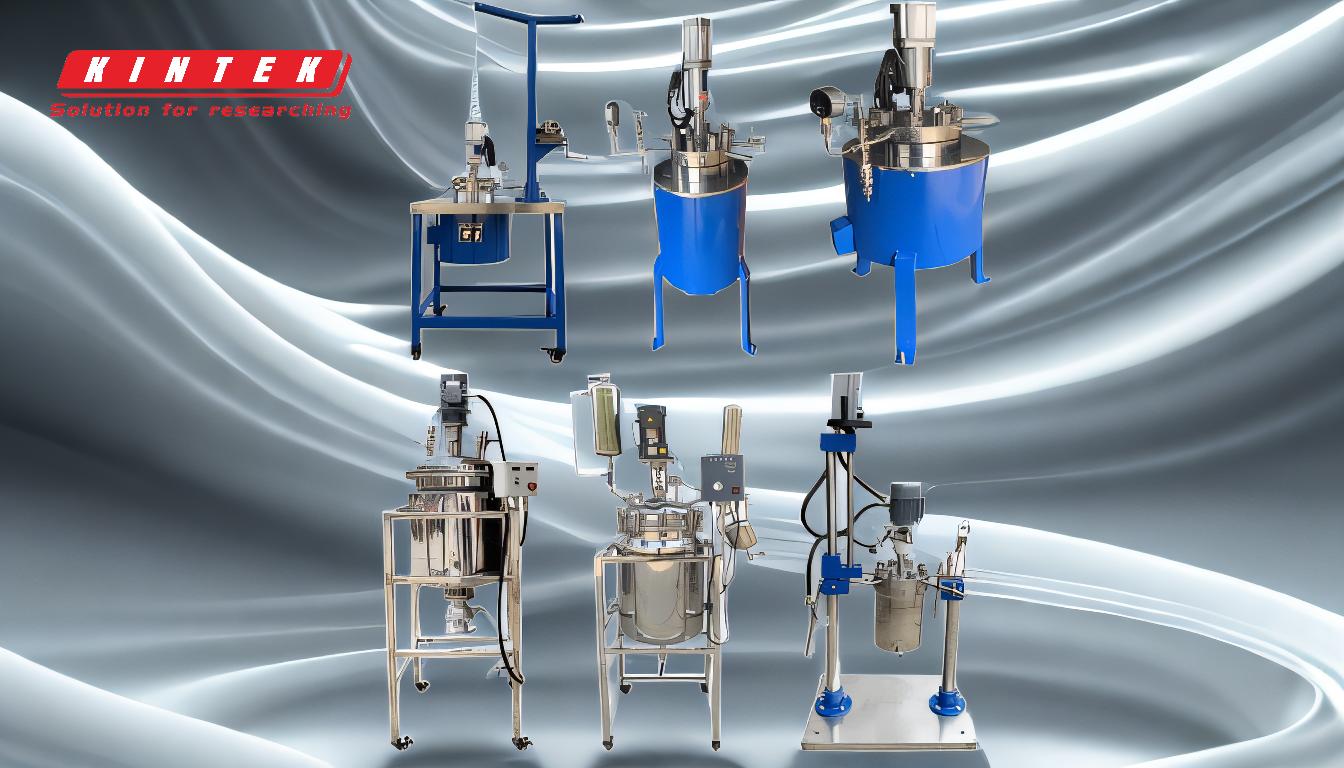
-
What is Sintering?
- Sintering is a process that densifies powdered materials by heating them below their melting point, causing atomic diffusion that fuses the particles into a solid mass.
- This method is cost-effective and versatile, making it suitable for producing complex parts in industries like automotive, aerospace, and electronics.
-
Types of Sintering Furnaces:
-
Hot Press Sintering Furnace:
- Combines high temperature and high pressure in a vacuum environment to sinter ceramic powders.
- Components include a furnace body, heater, pressure system, and vacuum system.
- The process involves loading powder, evacuating the furnace, heating, applying pressure, and cooling.
-
Vacuum Sintering Furnace:
- Operates in a vacuum to prevent oxidation and contamination, improving product quality.
- Key components include a vacuum chamber, heating elements, vacuum pumps, and temperature control systems.
- Steps involve charging the material, vacuuming, heating, insulation, and cooling.
-
Atmosphere Sintering Furnace:
- Controls the furnace atmosphere (e.g., nitrogen, argon) to optimize sintering conditions.
- Includes heating devices, pressure mechanisms, sintering chambers, and gas control systems.
- The process results in material migration, grain boundary movement, and pore elimination, producing dense ceramic bodies.
-
Hot Press Sintering Furnace:
-
Applications of Sintering:
- Used to manufacture components like gears, couplings, bearings, pulleys, rotors, sprockets, electrical contacts, cams, and armatures.
- Suitable for a wide range of materials, including metals, ceramics, and composites.
-
Advantages of Sintering:
- Produces complex shapes with high precision and minimal material waste.
- Enhances material properties such as strength, density, and wear resistance.
- Operates at temperatures below the melting point, reducing energy consumption.
-
Key Components of a Sintering Furnace:
- Vacuum Chamber: Designed to withstand high temperatures and vacuum conditions.
- Heating Elements: Provide the necessary high temperatures for sintering.
- Vacuum Pumps: Create and maintain the vacuum environment.
- Temperature Control Systems: Ensure precise heating and cooling rates.
- Charging System: Facilitates loading and unloading of materials.
- Water Cooling System: Cools the furnace shell and vacuum pump to maintain operational efficiency.
-
How Sintering Works:
- Stage 1: Powdered material is compressed into a weak, oversize component using a mold or binder.
- Stage 2: The component is heated to below the melting point, causing particles to fuse and the binder to burn away, resulting in a full-strength part.
By understanding the fundamentals of sintering and the role of a sintering furnace, manufacturers can optimize their processes to produce high-quality components efficiently and cost-effectively.
Summary Table:
Aspect | Details |
---|---|
What is Sintering? | Densifies powdered materials by heating below melting point, fusing particles into a solid mass. |
Types of Sintering Furnaces | - Hot Press Sintering Furnace |
- Vacuum Sintering Furnace
- Atmosphere Sintering Furnace | | Applications | Gears, bearings, electrical contacts, and more. Suitable for metals, ceramics, and composites. | | Advantages | Produces complex shapes, enhances material properties, and reduces energy consumption. | | Key Components | Vacuum chamber, heating elements, vacuum pumps, temperature control systems, charging system, water cooling system. | | How Sintering Works | 1. Compress powder into a weak component.
- Heat below melting point to fuse particles and burn away binder. |
Ready to optimize your material production process? Contact us today to learn more about sintering furnaces!