A sputtering machine is a sophisticated piece of equipment used to deposit thin films of materials onto substrates through a process called sputtering. This process involves creating a plasma of energetic ions, typically argon, which bombard a target material (cathode) to eject atoms. These ejected atoms then deposit onto a substrate (anode), forming a thin film. Sputtering is widely used in industries such as semiconductors, optics, and electronics for applications ranging from thin-film transistors to anti-reflective coatings and biomedical implants. The process is highly versatile, allowing for the deposition of various materials, including metals, oxides, and nitrides, with precise control over film thickness and composition.
Key Points Explained:
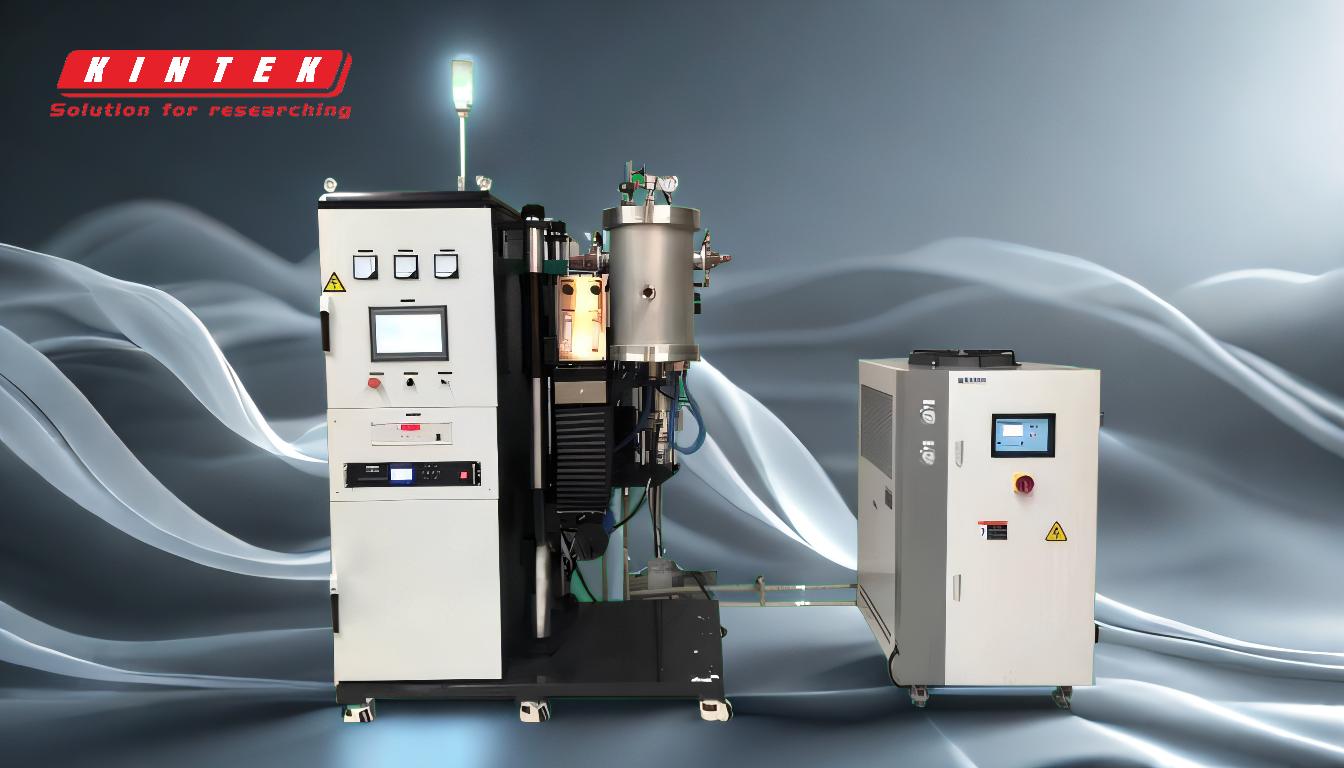
-
Basic Mechanism of Sputtering:
- Sputtering occurs in a vacuum chamber where an inert gas, typically argon, is ionized to form a plasma.
- A negative charge is applied to the target material (cathode), attracting positively charged argon ions.
- These ions bombard the target at high velocity, ejecting atomic-sized particles from the target surface.
- The ejected particles travel through the vacuum and deposit onto a substrate, forming a thin film.
-
Components of a Sputtering Machine:
- Target: The material to be sputtered, usually in the form of a flat or cylindrical solid piece. The target must be large enough to avoid unintended sputtering of other components.
- Substrate: The surface onto which the thin film is deposited, often a wafer or glass.
- Vacuum Chamber: Maintains a high vacuum to ensure the purity of the deposited film and to facilitate the ionization of the inert gas.
- Power Supply: Applies the necessary voltage to create the plasma and accelerate ions toward the target.
-
Types of Sputtering:
- Reactive Sputtering: Involves sputtering a metal target in the presence of a reactive gas (e.g., oxygen or nitrogen) to deposit compounds like oxides or nitrides. This method is often used to achieve higher deposition rates compared to other techniques like RF magnetron deposition.
- Magnetron Sputtering: Uses magnetic fields to confine the plasma near the target, increasing the efficiency of the sputtering process and allowing for higher deposition rates.
-
Applications of Sputtering:
- Semiconductor Industry: Sputtering is extensively used to deposit thin films of various materials in integrated circuit processing, including contact metals for thin-film transistors and low-emissivity coatings.
- Optics: Used to deposit anti-reflective coatings on glass for optical applications.
- Electronics: Gold sputtering is used to coat circuit panels and electronic components due to gold's excellent conductivity.
- Biomedical: Sputtering is used to coat biomedical implants with radiopaque films, making them visible in X-rays, and to prepare tissue samples for electron microscope scanning.
-
Advantages of Sputtering:
- Versatility: Can deposit a wide range of materials, including metals, alloys, and compounds.
- Precision: Allows for precise control over film thickness and composition.
- Uniformity: Produces highly uniform films, even on complex geometries.
- High Melting Point Materials: Particularly useful for depositing materials with high melting points that are difficult to deposit using other methods like chemical vapor deposition (CVD).
-
Challenges and Considerations:
- Target Erosion: Over time, the target material erodes, forming grooves or "race tracks," which can affect the uniformity of the deposited film.
- Vacuum Requirements: Sputtering requires a high vacuum, which can be more demanding than other deposition methods.
- Cost: The equipment and maintenance costs can be high, especially for large-scale industrial applications.
-
Recent Developments:
- Transparent and Metal Electrodes: Sputtering is increasingly used to create transparent and metal electrodes for thin-film solar cells and TFT-LCD components.
- Advanced Materials: Research is ongoing to develop new target materials and sputtering techniques to improve film properties and deposition rates.
In summary, a sputtering machine is a critical tool in modern manufacturing and research, enabling the precise deposition of thin films for a wide range of applications. Its versatility, precision, and ability to handle high melting point materials make it indispensable in industries ranging from semiconductors to biomedical engineering.
Summary Table:
Aspect | Details |
---|---|
Process | Uses plasma to eject atoms from a target, depositing them onto a substrate. |
Key Components | Target, substrate, vacuum chamber, power supply. |
Types | Reactive sputtering, magnetron sputtering. |
Applications | Semiconductors, optics, electronics, biomedical implants. |
Advantages | Versatile, precise, uniform, handles high melting point materials. |
Challenges | Target erosion, high vacuum requirements, cost. |
Interested in sputtering machines for your applications? Contact our experts today to learn more!