Vacuum coating is a thin-film deposition technology used to apply thin layers of materials (metallic, ceramic, or other compounds) onto substrates like glass, metal, or plastics. This process occurs in a vacuum environment, where the coating material is vaporized or ionized and then deposited onto the target surface. Vacuum coating enhances properties such as durability, wear resistance, corrosion protection, optical performance, and energy efficiency. Common methods include Physical Vapor Deposition (PVD) and Chemical Vapor Deposition (CVD). Applications range from decorative and functional coatings in industries like automotive, aerospace, and electronics to specialized uses in solar cells, optical films, and medical devices.
Key Points Explained:
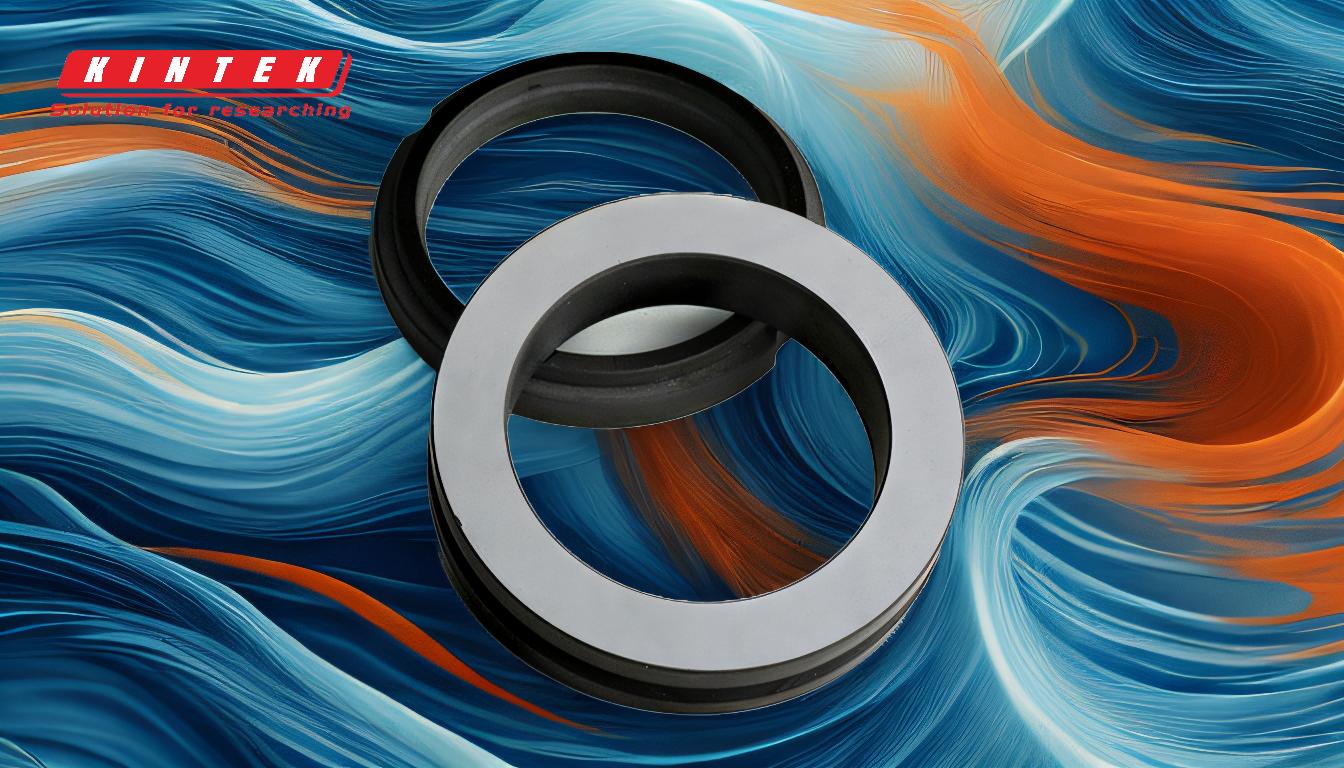
-
Definition and Process of Vacuum Coating:
- Vacuum coating involves depositing thin layers of materials onto substrates in a vacuum environment.
- The process typically uses Physical Vapor Deposition (PVD) or Chemical Vapor Deposition (CVD).
- In PVD, materials are vaporized or ionized using thermal energy or plasma, while CVD involves chemical reactions to form the coating.
- The vacuum environment ensures minimal contamination and allows for precise control over the coating's thickness and properties.
-
Key Technologies in Vacuum Coating:
-
Physical Vapor Deposition (PVD):
- Involves vaporizing the coating material in a vacuum chamber and depositing it onto the substrate.
- Commonly used for metallic and ceramic coatings.
- Produces thin, durable, and wear-resistant layers.
-
Chemical Vapor Deposition (CVD):
- Uses chemical reactions to deposit coatings from gaseous precursors.
- Ideal for creating high-purity, uniform coatings with complex compositions.
- Often used in semiconductor and optical applications.
-
Physical Vapor Deposition (PVD):
-
Applications of Vacuum Coating:
-
Decorative and Functional Coatings:
- Used on glass, metal, and plastics for aesthetic and protective purposes.
- Examples include low-emissivity glass for energy efficiency and decorative coatings on automotive parts.
-
Industrial and Manufacturing:
- Applied to engine components for wear resistance and durability.
- Used in aerospace and medical industries for specialized coatings.
-
Electronics and Optics:
- Essential for manufacturing microchips, LEDs, solar cells, and optical films.
- Enhances conductivity, light harvesting, and device performance.
-
Energy and Sustainability:
- Used in thin-film solar cells to improve efficiency and durability.
- Applied to flexible packaging materials for permeation barriers.
-
Decorative and Functional Coatings:
-
Advantages of Vacuum Coating:
-
Precision and Control:
- Allows for nanoscale thickness control, ensuring uniform and consistent coatings.
-
Enhanced Material Properties:
- Improves hardness, wear resistance, corrosion protection, and optical performance.
-
Versatility:
- Suitable for a wide range of materials and substrates, including metals, ceramics, and polymers.
-
Clean and Contamination-Free:
- The vacuum environment minimizes impurities, resulting in high-quality coatings.
-
Precision and Control:
-
Industries Utilizing Vacuum Coating:
-
Automotive:
- Used for decorative finishes and protective coatings on carbon fiber composites and engine components.
-
Aerospace:
- Applied to critical components for wear resistance and corrosion protection.
-
Medical:
- Used in devices requiring biocompatible and durable coatings.
-
Electronics:
- Essential for semiconductor devices, flexible displays, and sensors.
-
Energy:
- Key in solar cell manufacturing and energy-efficient glass production.
-
Automotive:
-
Future Trends and Innovations:
- Development of advanced materials for coatings, such as nanocomposites and hybrid organic-inorganic layers.
- Increased use in renewable energy applications, including next-generation solar cells and energy storage devices.
- Integration with additive manufacturing (3D printing) for complex geometries and customized coatings.
- Expansion into emerging industries like wearable technology and flexible electronics.
In summary, vacuum coating is a versatile and highly effective technology with applications across numerous industries. Its ability to enhance material properties, combined with precision and adaptability, makes it a critical process in modern manufacturing and innovation.
Summary Table:
Aspect | Details |
---|---|
Process | Deposition of thin layers in a vacuum using PVD or CVD methods. |
Key Technologies | - Physical Vapor Deposition (PVD) |
- Chemical Vapor Deposition (CVD) | |
Applications | Automotive, aerospace, electronics, medical devices, solar cells, optics. |
Advantages | Precision control, enhanced durability, corrosion protection, versatility. |
Industries | Automotive, aerospace, medical, electronics, energy. |
Future Trends | Nanocomposites, renewable energy, 3D printing, wearable technology. |
Learn how vacuum coating can transform your products—contact our experts today!