Furnace brazing, particularly in a vacuum brazing furnace, offers several significant advantages, making it a preferred method for joining materials in industries like aerospace, particle physics, and metallurgical research. The process involves heating entire assemblies to a temperature where the braze alloy melts and flows into the joint, creating strong, reliable bonds upon cooling. Key benefits include uniform temperature distribution, precise control, low contamination, and the ability to handle large batches efficiently. Additionally, vacuum brazing eliminates part distortion, allows for joining unweldable materials, and ensures metallurgical repeatability, making it ideal for high-precision applications.
Key Points Explained:
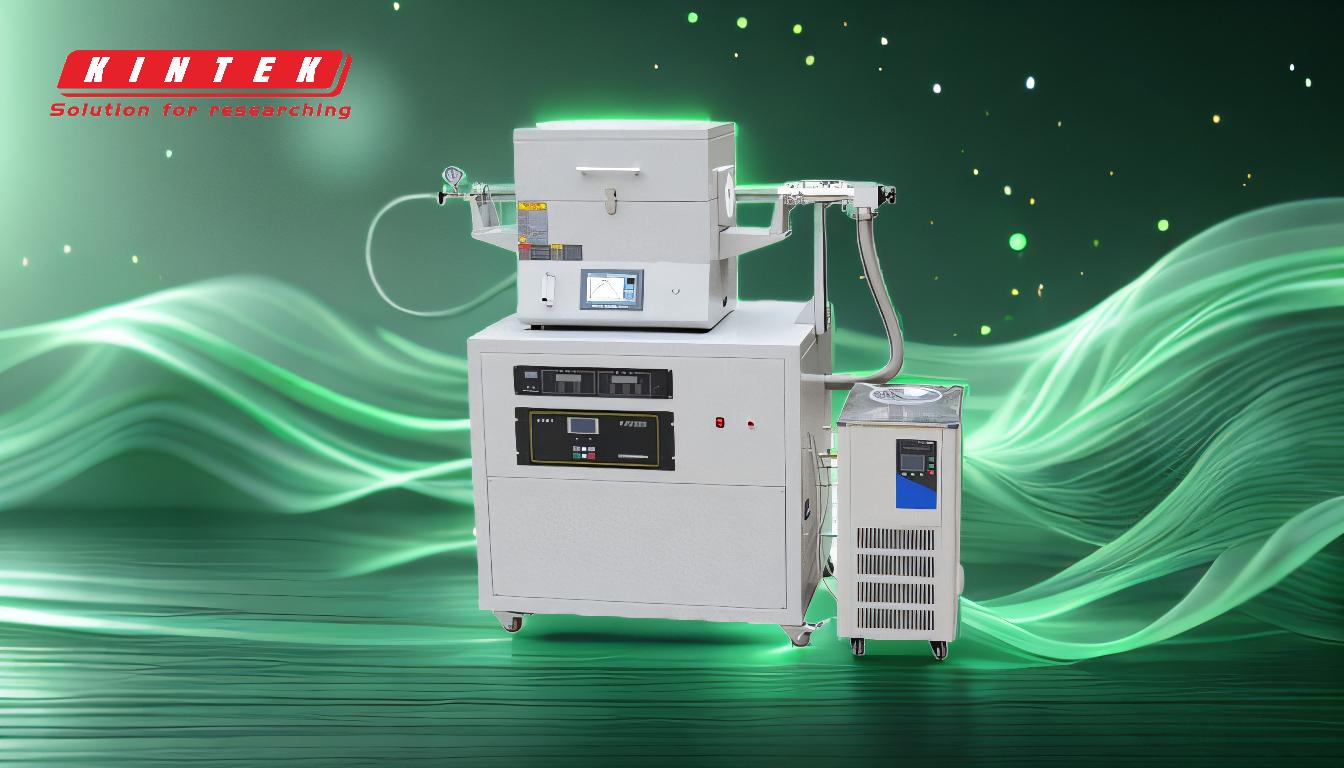
-
Uniform Temperature Distribution:
- Vacuum brazing furnaces provide uniform temperatures within the range of 1100–1500°C (2000–2800°F), ensuring consistent heating across the entire assembly. This uniformity is critical for achieving reliable and repeatable brazing results, especially when dealing with large or complex components.
-
Precise Temperature Control:
- The ability to control temperature within a small area ensures that the braze alloy melts and flows precisely where needed. This precision is enhanced by sophisticated cycle programming and barcode-linked systems, which recognize workpieces and apply the correct heating cycles automatically.
-
Low Contamination:
- The vacuum environment minimizes contamination from carbon, oxygen, and other gases, which can compromise the integrity of the braze joint. The process also removes oxide layers from the workpiece surfaces, ensuring clean, strong bonds.
-
Efficient Batch Processing:
- Furnace brazing is typically a batch process, where entire assemblies are loaded into the furnace at once. This method is time and energy-intensive but is justified for materials that are highly reactive to oxygen, as it prevents oxide formation that could hinder the brazing process.
-
Elimination of Part Distortion:
- Unlike other metal joining processes, vacuum brazing minimizes thermal distortion. The controlled heating and cooling cycles ensure that parts maintain their shape and dimensional accuracy, which is crucial for high-precision applications.
-
Joining Unweldable Materials:
- Vacuum brazing allows for the joining of materials that are difficult or impossible to weld. This capability expands the range of materials that can be used in manufacturing, enabling more innovative and complex designs.
-
Environmental and Operational Efficiency:
- Vacuum brazing furnaces are designed with features like water-cooled double skins to keep external temperatures low and pre-programmed controls to minimize human resource waste. These features contribute to a more environmentally friendly and operationally efficient process.
-
Metallurgical Repeatability:
- The ability to computer-control the brazing process ensures that each batch meets the same high standards, providing consistent quality and performance across multiple production runs.
In summary, the advantages of furnace brazing, particularly in a vacuum environment, make it an indispensable process for industries requiring high precision, reliability, and efficiency. The combination of uniform heating, precise control, low contamination, and the ability to handle complex materials ensures that vacuum brazing remains a top choice for advanced manufacturing applications.
Summary Table:
Advantage | Description |
---|---|
Uniform Temperature Distribution | Ensures consistent heating across assemblies, ideal for large or complex parts. |
Precise Temperature Control | Allows precise melting and flow of braze alloy for accurate joint formation. |
Low Contamination | Minimizes contamination from gases, ensuring clean and strong bonds. |
Efficient Batch Processing | Handles large batches efficiently, reducing oxide formation. |
Elimination of Part Distortion | Maintains shape and dimensional accuracy during heating and cooling. |
Joining Unweldable Materials | Enables bonding of materials that are difficult or impossible to weld. |
Environmental and Operational Efficiency | Features like water-cooled skins and pre-programmed controls enhance efficiency. |
Metallurgical Repeatability | Ensures consistent quality and performance across production runs. |
Unlock the full potential of vacuum brazing for your projects—contact our experts today!