An electric arc furnace (EAF) is a high-temperature melting furnace primarily used in the steel industry to melt scrap metal and produce carbon steel, alloy steel, and cast-iron products. It operates by generating an electric arc between graphite electrodes and the metal charge, reaching temperatures up to 3275°F (1800°C). The process is energy-efficient, self-contained, and relies on electrical energy rather than secondary heat sources. EAFs are widely used for recycling ferrous scrap, making them a sustainable alternative to traditional blast furnaces. The melting process involves stages like charging, meltdown, and refining, with added materials like burnt lime and spar to aid slag formation.
Key Points Explained:
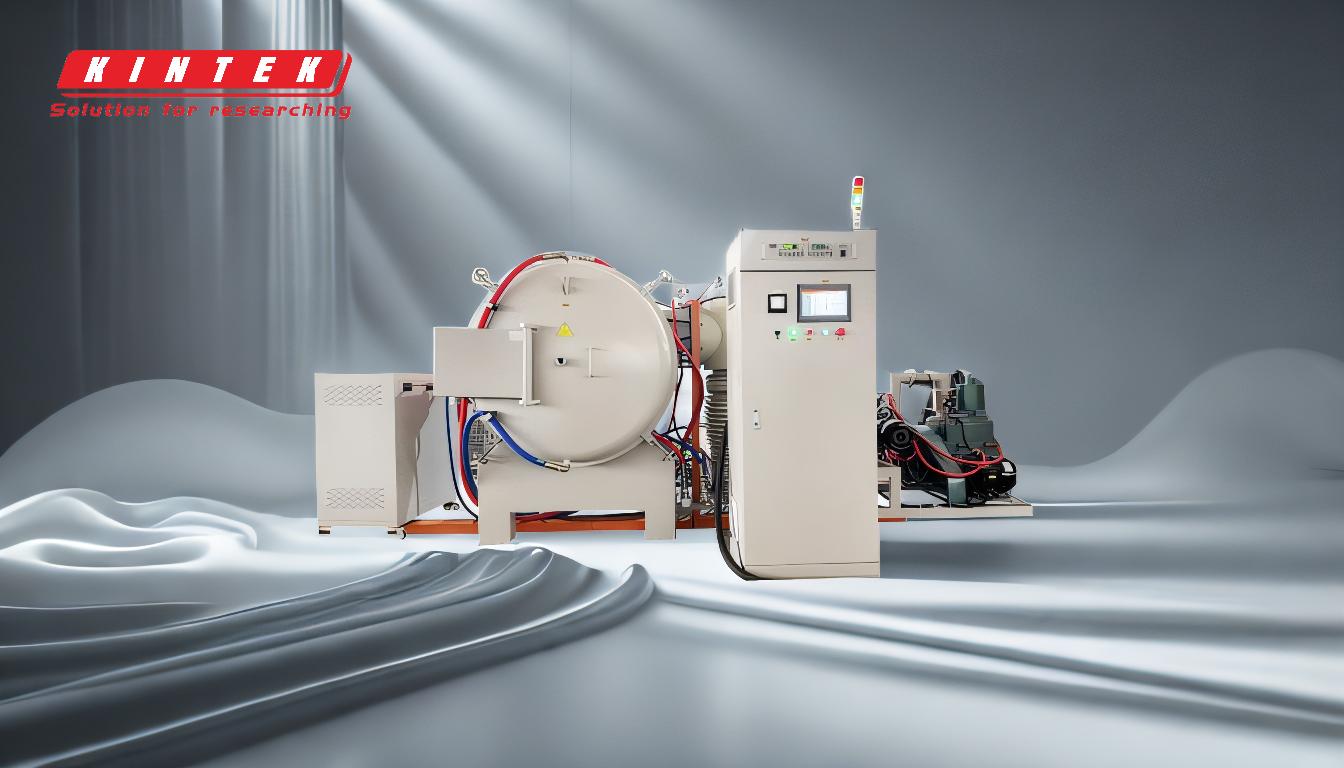
-
Primary Use of Electric Arc Furnaces:
- Electric arc furnaces are primarily used to melt scrap metal, including ferrous scrap, to produce carbon steel, alloy steel, and cast-iron products.
- Unlike traditional blast furnaces, EAFs do not require molten metal as a base material, making them ideal for recycling and reusing scrap metal.
-
Working Principle:
- EAFs generate heat through an electric arc formed between graphite electrodes and the metal charge.
- The arc creates a plasma discharge, producing intense heat (up to 3275°F or 1800°C) that melts the metal.
- The process is self-contained, relying solely on electrical energy without the need for external heat sources.
-
Materials Melted in EAFs:
- Scrap Steel: The primary raw material for EAFs, including heavy and light scrap, which is preheated and charged into the furnace.
- Alloying Elements: Materials like carbon, silicon, and manganese are oxidized during the melting process to refine the steel.
- Additives: Burnt lime and spar are added to facilitate slag formation, which helps remove impurities.
-
Process Stages:
- Charging: Scrap metal is loaded into the furnace using a large basket. The roof swings open to allow charging.
- Meltdown: Electrodes are lowered onto the scrap, and an electric arc is formed. The voltage is increased to accelerate melting.
- Refining: Oxygen may be added to oxidize impurities, and slag is formed to separate impurities from the molten metal.
-
Energy Consumption:
- EAFs are energy-efficient, requiring approximately 350 kWh to 370 kWh of electrical energy to melt one ton of scrap.
- The use of electrical energy makes EAFs more environmentally friendly compared to traditional methods that rely on fossil fuels.
-
Applications in Industry:
- EAFs are widely used in the steel industry for producing large slabs, beams, and other structural components.
- They are also used in foundries for melting shredded scrap and producing high-quality steel products.
-
Advantages of EAFs:
- Sustainability: EAFs promote recycling by using scrap metal as the primary raw material.
- Flexibility: They can produce a wide range of steel grades and alloys.
- Cost-Effectiveness: Lower operating costs compared to traditional blast furnaces due to reduced energy and raw material requirements.
-
Temperature Control:
- EAFs are equipped with advanced devices for accurate temperature control, ensuring safe and efficient operation.
- The ability to maintain high temperatures (up to 3275°F) allows for rapid melting and refining of metals.
-
Environmental Impact:
- EAFs contribute to reducing carbon emissions by recycling scrap metal and using electrical energy instead of fossil fuels.
- The process generates less waste and minimizes the need for mining raw materials.
-
Future Trends:
- The adoption of EAFs is expected to grow as industries prioritize sustainability and energy efficiency.
- Innovations in electrode technology and energy recovery systems are further enhancing the efficiency of EAFs.
In summary, electric arc furnaces are versatile, energy-efficient, and environmentally friendly tools for melting scrap metal and producing high-quality steel products. Their ability to recycle materials and operate at high temperatures makes them a cornerstone of modern steelmaking.
Summary Table:
Key Aspect | Details |
---|---|
Primary Use | Melting scrap metal to produce carbon steel, alloy steel, and cast iron. |
Working Principle | Generates heat via electric arc between graphite electrodes and metal charge. |
Temperature Range | Up to 3275°F (1800°C). |
Energy Consumption | 350–370 kWh per ton of scrap. |
Main Materials | Scrap steel, alloying elements, burnt lime, and spar. |
Process Stages | Charging, meltdown, refining. |
Advantages | Sustainability, flexibility, cost-effectiveness, precise temperature control. |
Environmental Impact | Reduces carbon emissions and minimizes mining needs. |
Learn how electric arc furnaces can transform your steelmaking process—contact our experts today!