An induction furnace for heat treatment is a specialized device that uses electromagnetic induction to heat metals for processes like melting, forging, or heat treatment. It operates by generating eddy currents within the metal, which produce heat due to electrical resistance. This method ensures uniform heating, precise temperature control, and minimal contamination, making it ideal for applications in foundries and metalworking industries. Induction furnaces are highly efficient, environmentally friendly, and capable of continuous operation. They consist of key components like a power unit, chiller, and vacuum unit, and are designed with advanced features such as automatic frequency scanning, comprehensive protection systems, and energy-saving capabilities.
Key Points Explained:
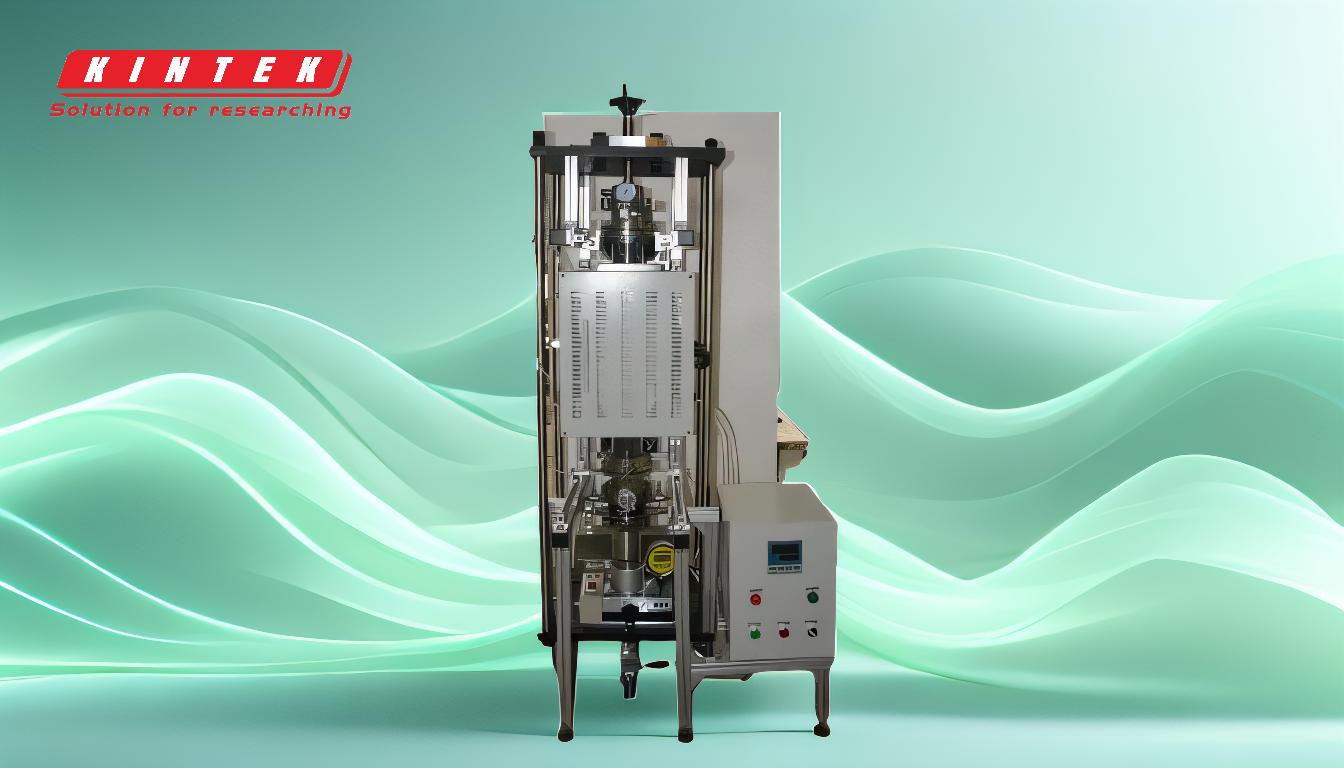
-
Principle of Operation:
- Induction furnaces use electromagnetic induction to generate heat. An alternating current passes through a coil, creating a magnetic field that induces eddy currents in the metal. These currents produce heat due to the metal's electrical resistance, ensuring uniform heating and melting.
-
Key Components:
- Inductor (Coil): Generates the alternating magnetic field.
- Furnace Body: Holds the material to be heated or melted.
- Power Supply: Provides the necessary electrical energy.
- Capacitor: Helps in tuning the system for optimal performance.
- Control System: Manages temperature, power, and other operational parameters.
-
Temperature Capabilities:
- Induction furnaces can reach extremely high temperatures, typically up to 1800ºC. This makes them suitable for melting a wide range of metals, including iron, steel, copper, aluminum, and precious metals.
-
Advantages of Induction Heating:
- Uniform Heating: Ensures consistent temperature distribution throughout the material.
- Precise Control: Allows for accurate temperature regulation, essential for heat treatment processes.
- Minimal Contamination: Unlike gas furnaces, induction furnaces reduce the risk of contamination, resulting in purer alloys.
-
Operational Features:
- Automatic Frequency Scanning: Ensures smooth and stable operation by automatically adjusting the frequency.
- Comprehensive Protection Systems: Includes safeguards against over-voltage, over-current, overheating, and water shortage.
- Energy Efficiency: Designed to be power-saving and environmentally friendly, reducing operational costs.
-
Applications:
- Foundries: Used for melting metals and producing castings.
- Heat Treatment: Employed for processes like annealing, hardening, and tempering.
- Vacuum Melting: Ideal for producing high-purity alloys with minimal oxidation and gas impurities.
-
Design and Maintenance:
- Modular Design: Allows for easy replacement of furnace bodies to accommodate different materials and weights.
- User-Friendly Operation: Features like display functions for current, voltage, and time simplify monitoring and adjustments.
- Low Maintenance: Well-coordinated components and integrated circuits make maintenance straightforward and cost-effective.
-
Environmental and Economic Benefits:
- Low Carbon Footprint: Induction furnaces are more environmentally friendly compared to traditional furnaces.
- Cost-Effective: Uniform smelting and energy efficiency reduce overall production costs.
- Continuous Operation: Capable of 24-hour continuous smelting, enhancing productivity.
In summary, an induction furnace for heat treatment is a versatile and efficient tool in metalworking, offering precise temperature control, uniform heating, and minimal contamination. Its advanced features and robust design make it a preferred choice for various industrial applications.
Summary Table:
Feature | Description |
---|---|
Principle of Operation | Uses electromagnetic induction to generate heat via eddy currents in metals. |
Key Components | Inductor (coil), furnace body, power supply, capacitor, and control system. |
Temperature Range | Up to 1800ºC, suitable for melting iron, steel, copper, aluminum, and more. |
Advantages | Uniform heating, precise control, minimal contamination, and energy efficiency. |
Applications | Foundries, heat treatment (annealing, hardening), and vacuum melting. |
Environmental Benefits | Low carbon footprint, cost-effective, and capable of continuous operation. |
Upgrade your metalworking processes with an induction furnace—contact us today to learn more!