An induction furnace is a highly efficient and widely used device for melting metals, relying on electromagnetic induction to generate heat. It is primarily composed of three key components: a power supply, an induction coil, and a crucible made of refractory materials. The power supply provides the necessary electrical energy, while the induction coil generates a magnetic field that induces eddy currents in the metal charge within the crucible, causing it to heat up and melt. The crucible, made of durable refractory materials, holds the metal charge and withstands the extreme temperatures required for melting. Additionally, some induction furnaces may include auxiliary components such as water-cooled cables, compensation capacitors, and reducers to enhance performance and efficiency.
Key Points Explained:
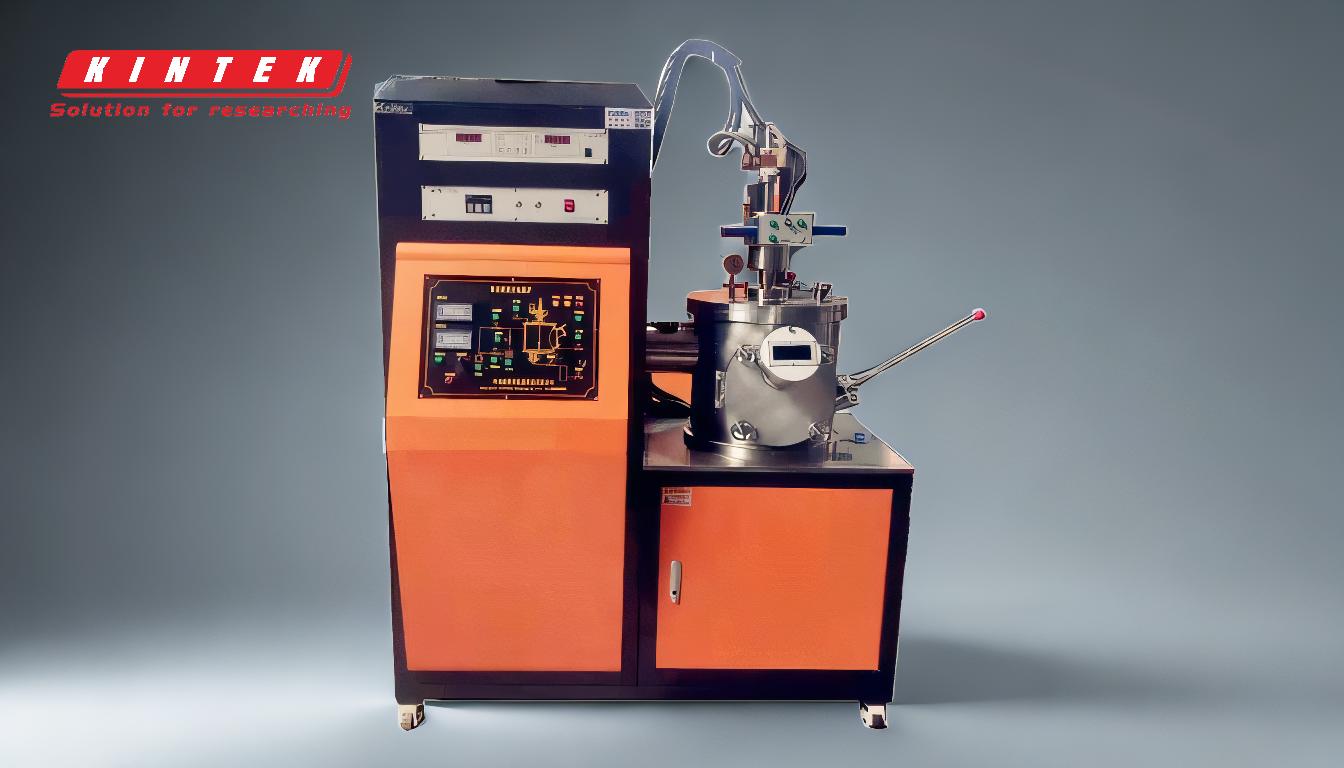
-
Power Supply:
- The power supply is the heart of the induction furnace, providing the electrical energy required to generate the magnetic field. It typically operates at high frequencies, such as 2500 Hz, to ensure efficient heating.
- The power supply must be robust and reliable, as it directly impacts the furnace's performance and energy efficiency. It often includes components like inverters and transformers to regulate and convert the electrical current.
-
Induction Coil:
- The induction coil, also known as the induction ring, is a critical component that generates the alternating magnetic field necessary for induction heating. It is usually made of copper or another highly conductive material to minimize energy loss.
- The coil is designed to create a strong magnetic field that penetrates the metal charge, inducing eddy currents that generate heat through resistance. The design and placement of the coil are crucial for ensuring uniform heating and efficient melting.
-
Crucible:
- The crucible is the container that holds the metal charge during the melting process. It is constructed from refractory materials, such as ceramics or graphite, which can withstand the extreme temperatures and chemical reactions involved in metal melting.
- The crucible's material and design are tailored to the specific type of metal being melted, ensuring durability and preventing contamination of the molten metal. It acts as the secondary winding of a transformer, completing the electrical circuit necessary for induction heating.
-
Metal Charge:
- The metal charge, placed inside the crucible, serves as the secondary winding of the induction furnace's transformer. When exposed to the magnetic field generated by the induction coil, the metal charge experiences eddy currents, which heat it to the melting point.
- The composition and size of the metal charge can affect the efficiency of the melting process, as well as the quality of the final product. Proper loading and distribution of the charge are essential for achieving consistent results.
-
Auxiliary Components:
- Water-Cooled Cables: These cables are used to connect the power supply to the induction coil, ensuring efficient energy transfer while preventing overheating. The water cooling system helps maintain the cables' temperature within safe limits.
- Compensation Capacitors: These components are used to improve the power factor of the induction furnace, enhancing its energy efficiency and reducing operational costs.
- Reducer: In some induction furnaces, a reducer is used to control the flow of molten metal, ensuring precise pouring and minimizing waste.
In summary, an induction furnace is a sophisticated system composed of several key components that work together to achieve efficient and precise metal melting. The power supply, induction coil, and crucible are the core elements, while auxiliary components like water-cooled cables and compensation capacitors enhance performance and reliability. Understanding these components is essential for selecting and operating an induction furnace effectively.
Summary Table:
Component | Role | Key Features |
---|---|---|
Power Supply | Provides electrical energy for generating the magnetic field | High-frequency operation (e.g., 2500 Hz), includes inverters and transformers |
Induction Coil | Generates alternating magnetic field for induction heating | Made of copper or conductive materials, ensures uniform heating |
Crucible | Holds the metal charge and withstands extreme temperatures | Made of refractory materials (e.g., ceramics, graphite), prevents contamination |
Metal Charge | Acts as the secondary winding, heats up due to eddy currents | Size and composition affect melting efficiency and product quality |
Auxiliary Components | Enhance performance and efficiency | Includes water-cooled cables, compensation capacitors, and reducers |
Ready to optimize your metal melting process? Contact us today to learn more about induction furnaces!