An inert oven is a specialized heating device designed to operate in an environment devoid of reactive gases, such as oxygen, to prevent oxidation or other chemical reactions during the heating process. It is commonly used in industries like metallurgy, materials science, and electronics, where maintaining a non-reactive atmosphere is critical. The oven is typically filled with inert gases like nitrogen or argon to create a controlled environment. This ensures that sensitive materials, such as metals, ceramics, or polymers, can be heated without degradation or contamination. Inert ovens are essential for processes like sintering, annealing, and curing, where precise temperature control and a contaminant-free environment are required.
Key Points Explained:
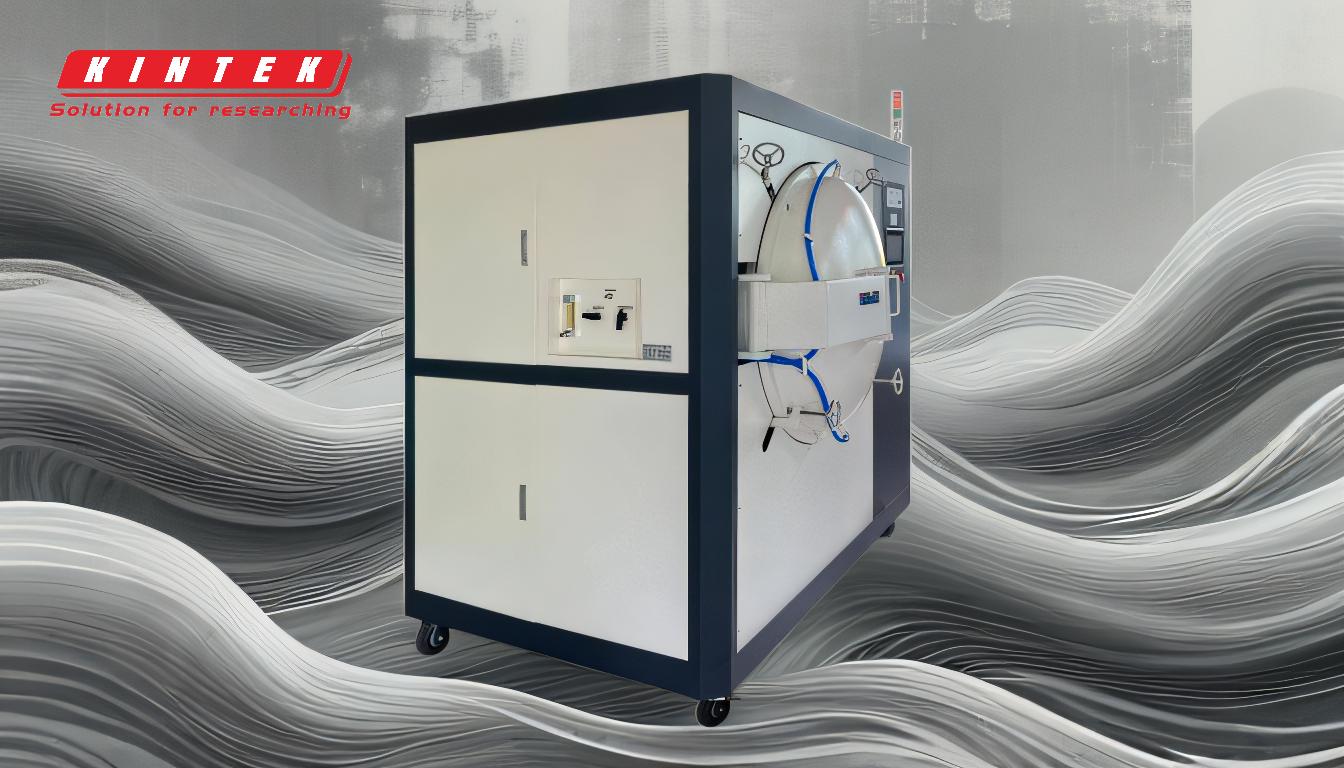
-
Definition and Purpose of an Inert Oven:
- An inert oven is a heating device that operates in a controlled, non-reactive atmosphere.
- Its primary purpose is to prevent oxidation, contamination, or unwanted chemical reactions during heating processes.
- It is widely used in industries that require precise thermal processing of sensitive materials.
-
Inert Atmosphere:
- The oven is filled with inert gases like nitrogen or argon, which displace oxygen and other reactive gases.
- This controlled environment ensures that materials being heated do not react with the surrounding atmosphere.
- The choice of gas depends on the specific application and the material being processed.
-
Applications of Inert Ovens:
- Metallurgy: Used for annealing, sintering, and heat treatment of metals to enhance their properties without oxidation.
- Materials Science: Essential for processing ceramics, composites, and advanced materials that require a contaminant-free environment.
- Electronics: Used in the production of semiconductors and other electronic components where even minor contamination can affect performance.
-
Key Features of Inert Ovens:
- Temperature Control: Precise temperature regulation is critical for achieving consistent results.
- Gas Purging System: Ensures the complete removal of reactive gases before and during the heating process.
- Safety Mechanisms: Includes features like pressure relief valves and gas monitoring systems to maintain a safe operating environment.
-
Advantages of Using an Inert Oven:
- Prevents oxidation and degradation of materials.
- Enables the processing of sensitive materials that cannot withstand reactive atmospheres.
- Improves the quality and consistency of the final product.
-
Considerations for Purchasing an Inert Oven:
- Size and Capacity: Choose an oven that meets the volume and size requirements of your materials.
- Temperature Range: Ensure the oven can achieve the temperatures needed for your specific processes.
- Gas Compatibility: Verify that the oven is compatible with the inert gases you plan to use.
- Safety Features: Look for ovens with robust safety mechanisms to protect both the materials and operators.
By understanding these key points, you can make an informed decision when selecting an inert oven for your specific needs. Whether you're working in research, manufacturing, or development, an inert oven is a valuable tool for ensuring the integrity and quality of your materials.
Summary Table:
Aspect | Details |
---|---|
Definition | A heating device operating in a controlled, non-reactive atmosphere. |
Purpose | Prevents oxidation, contamination, and unwanted chemical reactions. |
Inert Gases Used | Nitrogen, argon, or other non-reactive gases. |
Applications | Metallurgy, materials science, electronics. |
Key Features | Precise temperature control, gas purging system, safety mechanisms. |
Advantages | Prevents material degradation, ensures high-quality results. |
Purchase Considerations | Size, temperature range, gas compatibility, safety features. |
Ready to enhance your material processing? Contact us today to find the perfect inert oven for your needs!