Hydrogen annealing is a specialized heat treatment process conducted in a controlled hydrogen atmosphere to achieve specific material properties, such as stress relief, surface cleaning, and prevention of oxidation. This process is particularly beneficial for materials like steel, hard alloys, ceramic materials, and rare refractory metals. Hydrogen annealing is often referred to as "bright annealing" due to its ability to produce a bright, clean surface finish by reducing oxides on the material. However, precautions are necessary to avoid decarburization of steel parts. The process is typically carried out at elevated temperatures, often between 200-300°C, and can be more efficient due to hydrogen's higher heat transfer coefficient compared to other gases. While hydrogen annealing is effective, it is also more expensive, making nitrogen-hydrogen blends a cost-effective alternative in some cases.
Key Points Explained:
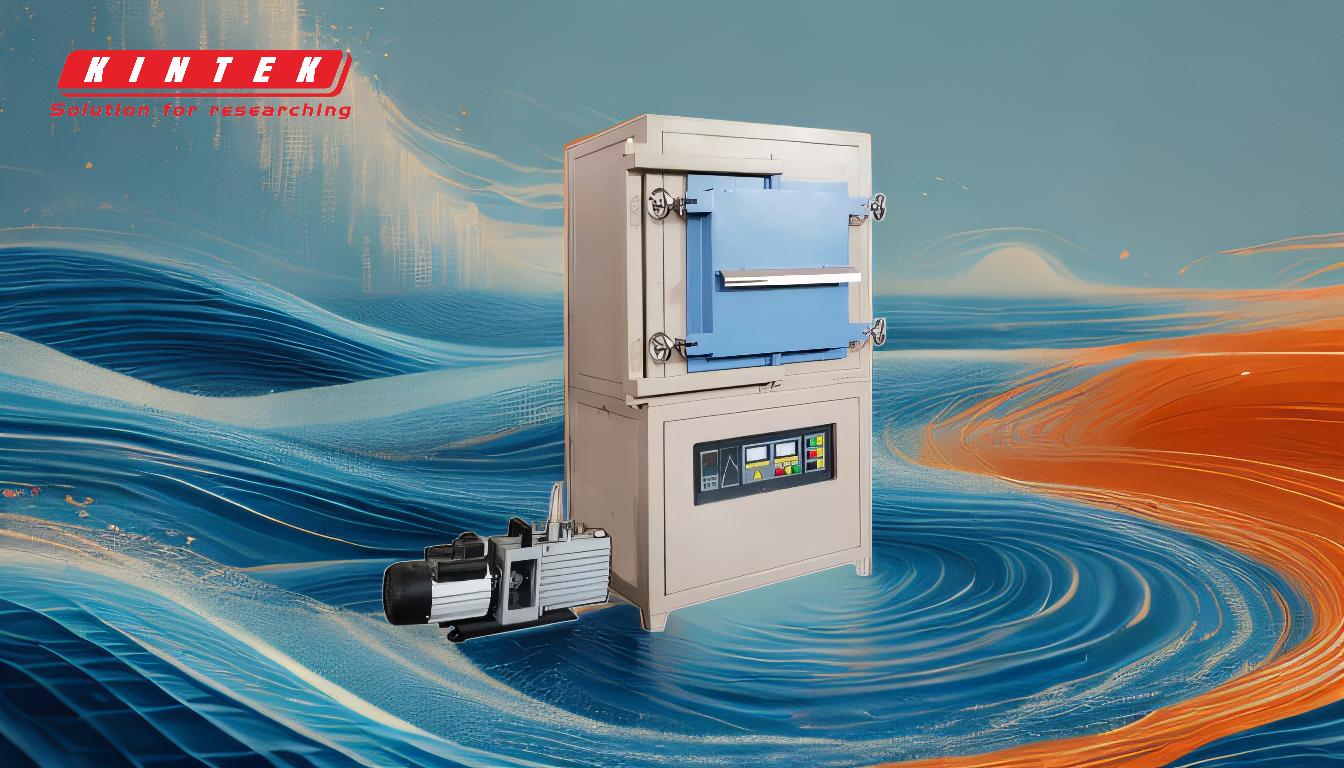
-
Definition and Purpose of Hydrogen Annealing:
- Hydrogen annealing is a heat treatment process performed in a 100% hydrogen atmosphere to relieve internal stresses, clean surfaces, and prevent oxidation.
- It is particularly useful for materials like steel, hard alloys, ceramic materials, and rare refractory metals.
- The process is often called "bright annealing" because it results in a bright, clean surface finish by reducing oxides on the material.
-
Process Conditions:
- The annealing process is typically conducted at elevated temperatures, usually between 200-300°C.
- The material is kept in a hydrogen annealing oven for several hours to ensure effective treatment.
- Hydrogen's high heat transfer coefficient makes the process more efficient compared to using air or a traditional hydrogen-nitrogen gas mixture.
-
Benefits of Hydrogen Annealing:
- Surface Cleaning: Hydrogen acts as a highly reducing gas, which helps in removing oxides from the material surface, leading to a bright finish.
- Stress Relief: The process helps in relieving internal stresses induced during fabrication processes like casting, welding, or coating.
- Oxidation Prevention: The hydrogen atmosphere prevents oxidation and discoloration of the material.
-
Challenges and Precautions:
- Decarburization: Hydrogen can decarburize steel parts, which may weaken the material. Precautions are necessary to mitigate this effect.
- Cost: Hydrogen annealing is more expensive due to the cost of maintaining a pure hydrogen atmosphere. Nitrogen-hydrogen blends are often used as a cost-effective alternative.
-
Applications:
- Hydrogen annealing is used in various industries for reducing, sintering, annealing, and surface treatment of materials.
- It is particularly beneficial for heat treating cast and welded components, as well as for materials that require a high-quality surface finish.
-
Equipment:
- A hydrogen annealing furnace is specifically designed for this process, using hydrogen or a mixture of hydrogen and nitrogen gas (with a hydrogen content greater than 5%) as a protective atmosphere.
- The furnace ensures a controlled environment for the annealing process, maintaining the necessary temperature and atmosphere conditions.
-
Post-Processing:
- Hydrogen annealing is often used immediately after processes like welding, coating, or galvanizing to remove enclosed hydrogen atoms responsible for hydrogen embrittlement.
- The process helps in improving the material's mechanical properties and overall durability.
By understanding these key points, one can appreciate the importance and complexity of hydrogen annealing in material processing, especially when a high-quality surface finish and stress relief are critical.
Summary Table:
Aspect | Details |
---|---|
Purpose | Relieve internal stresses, clean surfaces, prevent oxidation, and improve surface finish. |
Temperature Range | 200-300°C |
Key Benefits | Surface cleaning, stress relief, oxidation prevention, bright finish. |
Challenges | Risk of decarburization, higher cost compared to nitrogen-hydrogen blends. |
Applications | Steel, hard alloys, ceramics, rare refractory metals, cast/welded components. |
Equipment | Hydrogen annealing furnace with controlled hydrogen or nitrogen-hydrogen atmosphere. |
Optimize your material processing with hydrogen annealing—contact our experts today to learn more!