Biomass conversion efficiency refers to the effectiveness with which organic materials (biomass) are transformed into usable energy or valuable products. It is a critical metric in evaluating the performance of biomass conversion technologies, as it determines how much of the input biomass is successfully converted into the desired output, such as biofuels, heat, or electricity. Higher efficiency means more energy or product is derived from the same amount of biomass, reducing waste and improving sustainability. Understanding this concept is essential for optimizing processes, selecting appropriate technologies, and making informed decisions in renewable energy and biofuel production.
Key Points Explained:
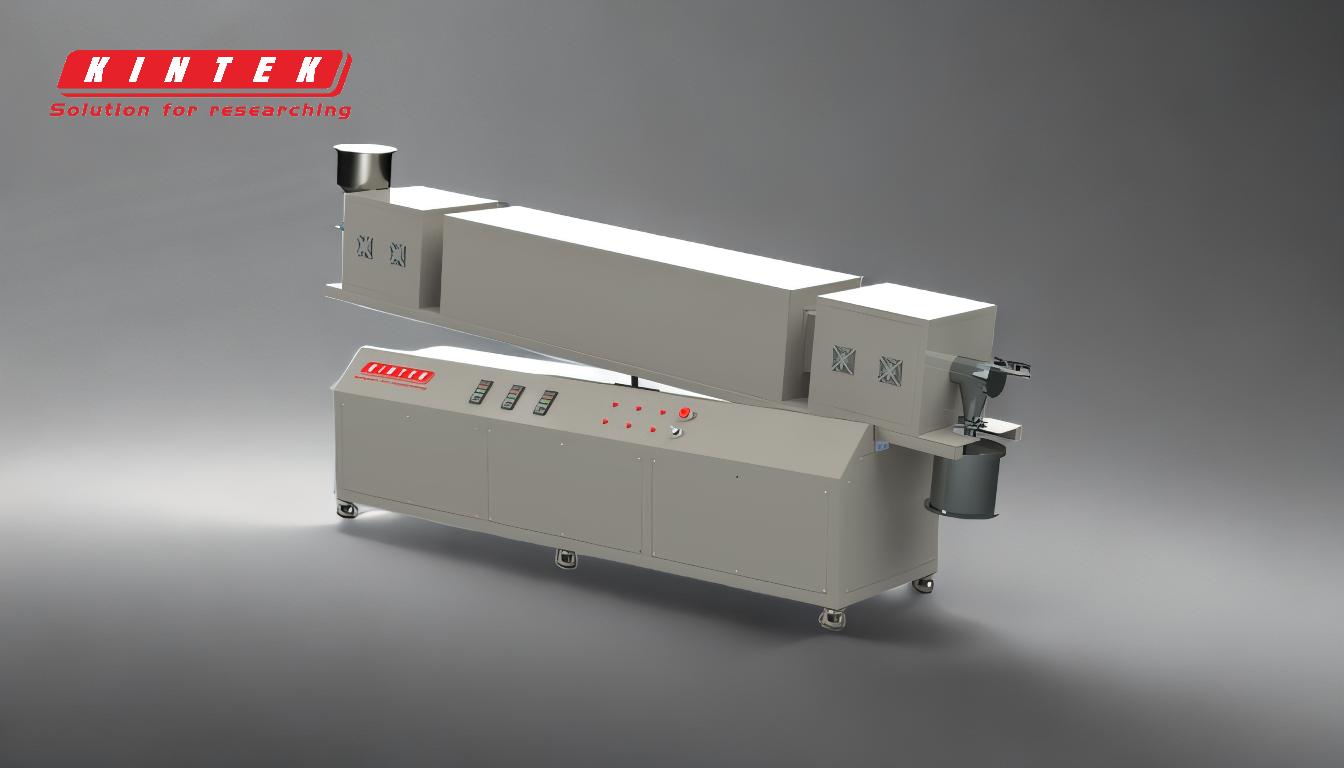
-
Definition of Biomass Conversion Efficiency:
- Biomass conversion efficiency measures the ratio of useful output (e.g., energy, biofuels) to the input biomass.
- It quantifies how effectively a conversion process transforms raw biomass into a usable form.
- Efficiency is typically expressed as a percentage, calculated as (Useful Output Energy / Input Biomass Energy) × 100.
-
Factors Influencing Biomass Conversion Efficiency:
- Type of Biomass: Different biomass feedstocks (e.g., wood, agricultural waste, algae) have varying energy densities and chemical compositions, affecting conversion efficiency.
- Conversion Technology: The method used (e.g., combustion, gasification, pyrolysis, anaerobic digestion) significantly impacts efficiency. For example, gasification may achieve higher efficiency than direct combustion.
- Process Conditions: Variables like temperature, pressure, and reaction time play a crucial role in determining efficiency.
- Moisture Content: High moisture levels in biomass can reduce efficiency by requiring additional energy for drying.
- Impurities and Contaminants: Presence of non-combustible materials or contaminants can lower the quality of the output.
-
Types of Biomass Conversion Processes:
-
Thermochemical Conversion:
- Includes processes like combustion, gasification, and pyrolysis.
- Converts biomass into heat, syngas, or bio-oil.
- Typically achieves higher energy recovery rates compared to biochemical methods.
-
Biochemical Conversion:
- Involves processes like anaerobic digestion and fermentation.
- Produces biogas, ethanol, or other biofuels.
- Efficiency depends on the activity of microorganisms and feedstock suitability.
-
Chemical Conversion:
- Uses chemical reactions to transform biomass into fuels or chemicals.
- Examples include transesterification for biodiesel production.
-
Mechanical Conversion:
- Involves physical processes like pelletizing or briquetting to improve biomass handling and combustion efficiency.
-
Thermochemical Conversion:
-
Importance of Biomass Conversion Efficiency:
- Economic Viability: Higher efficiency reduces the cost per unit of energy or product, making biomass conversion more competitive with fossil fuels.
- Environmental Impact: Efficient processes minimize waste and greenhouse gas emissions, contributing to sustainability goals.
- Resource Optimization: Maximizing efficiency ensures that limited biomass resources are used effectively, reducing pressure on land and ecosystems.
- Energy Security: Improved efficiency enhances the reliability of biomass as a renewable energy source, reducing dependence on non-renewable fuels.
-
Challenges in Achieving High Efficiency:
- Feedstock Variability: Inconsistent quality and composition of biomass can hinder consistent efficiency.
- Technological Limitations: Some conversion technologies are still in developmental stages and may not yet achieve optimal efficiency.
- Energy Losses: Heat loss, incomplete reactions, and byproduct formation can reduce overall efficiency.
- Scale-Up Issues: Achieving high efficiency at small scales may not translate to large-scale industrial operations.
-
Strategies to Improve Biomass Conversion Efficiency:
- Feedstock Preprocessing: Drying, grinding, or pelletizing biomass can enhance its suitability for conversion processes.
- Advanced Technologies: Investing in cutting-edge technologies like catalytic pyrolysis or integrated biorefineries can boost efficiency.
- Process Optimization: Fine-tuning process parameters (e.g., temperature, residence time) can maximize output.
- Co-Processing: Combining biomass with other materials (e.g., coal) or using hybrid systems can improve overall efficiency.
- Waste Utilization: Capturing and utilizing byproducts (e.g., heat, ash) can enhance the overall efficiency of the system.
-
Applications of Biomass Conversion Efficiency:
- Biofuel Production: Efficiency is critical in producing ethanol, biodiesel, and biogas for transportation and industrial use.
- Power Generation: Biomass power plants rely on efficient conversion to generate electricity from organic waste.
- Heat Production: Biomass boilers and stoves use efficient combustion to provide heating for residential and commercial spaces.
- Chemical Manufacturing: Efficient conversion processes enable the production of bio-based chemicals and materials.
-
Future Trends in Biomass Conversion Efficiency:
- Integration with Renewable Energy Systems: Combining biomass conversion with solar, wind, or hydropower can create hybrid systems with higher overall efficiency.
- Development of Novel Catalysts: Advances in catalyst technology can improve reaction rates and yields in thermochemical and chemical conversion processes.
- AI and Machine Learning: These technologies can optimize process parameters in real-time, enhancing efficiency.
- Circular Economy Approaches: Emphasizing waste-to-energy and closed-loop systems can maximize resource utilization and efficiency.
By understanding and improving biomass conversion efficiency, stakeholders can unlock the full potential of biomass as a sustainable and renewable resource, contributing to a greener and more energy-secure future.
Summary Table:
Aspect | Details |
---|---|
Definition | Ratio of useful output energy to input biomass energy, expressed as a percentage. |
Key Factors | Biomass type, conversion technology, process conditions, moisture content, impurities. |
Conversion Processes | Thermochemical (combustion, gasification), biochemical (anaerobic digestion), chemical, mechanical. |
Importance | Economic viability, environmental impact, resource optimization, energy security. |
Challenges | Feedstock variability, technological limitations, energy losses, scale-up issues. |
Improvement Strategies | Feedstock preprocessing, advanced technologies, process optimization, co-processing, waste utilization. |
Applications | Biofuel production, power generation, heat production, chemical manufacturing. |
Future Trends | Integration with renewables, novel catalysts, AI optimization, circular economy approaches. |
Ready to optimize your biomass conversion processes? Contact our experts today to get started!