Chemical sputtering is a specialized form of sputtering that involves chemical reactions between the bombarding ions and the target material, leading to the formation of volatile compounds that are then ejected from the surface. Unlike physical sputtering, which relies solely on the transfer of kinetic energy to eject atoms, chemical sputtering involves a chemical interaction that modifies the target material, making it easier to remove. This process is particularly relevant in applications involving reactive gases and materials that can form volatile compounds, such as in semiconductor manufacturing or the deposition of certain thin films.
Key Points Explained:
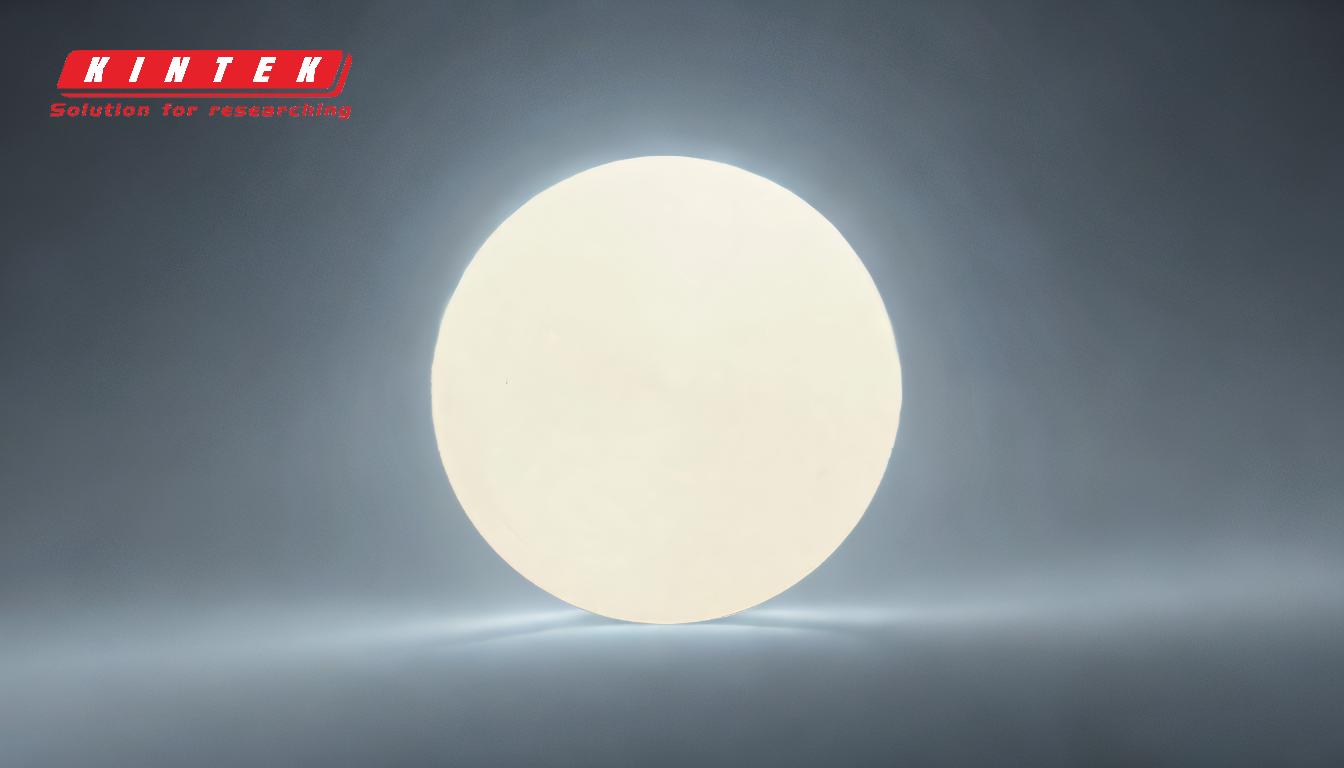
-
Definition of Chemical Sputtering:
- Chemical sputtering is a process where chemical reactions between the bombarding ions and the target material result in the formation of volatile compounds. These compounds are then ejected from the surface, leading to material removal.
- Unlike physical sputtering, which is purely mechanical, chemical sputtering involves chemical interactions that alter the target material's properties.
-
Mechanism of Chemical Sputtering:
- In chemical sputtering, reactive ions (such as oxygen, nitrogen, or fluorine) are used to bombard the target material.
- These ions react with the target atoms to form volatile compounds (e.g., metal oxides, nitrides, or fluorides).
- The volatile compounds have lower binding energy to the target surface, making them easier to eject compared to the original material.
-
Role of Reactive Gases:
- Reactive gases (e.g., O₂, N₂, CF₄) play a critical role in chemical sputtering by providing the ions that react with the target material.
- The choice of gas depends on the target material and the desired chemical reaction. For example, oxygen is often used to sputter metals that form stable oxides.
-
Applications of Chemical Sputtering:
- Semiconductor Manufacturing: Chemical sputtering is used to etch or deposit thin films with precise chemical compositions, such as silicon dioxide (SiO₂) or silicon nitride (Si₃N₄).
- Optical Coatings: It is employed to create anti-reflective or reflective coatings by depositing materials like titanium dioxide (TiO₂) or aluminum oxide (Al₂O₃).
- Wear-Resistant Coatings: Chemical sputtering is used to deposit hard coatings like titanium nitride (TiN) or diamond-like carbon (DLC) for industrial tools.
-
Advantages of Chemical Sputtering:
- Enhanced Material Removal: Chemical reactions can increase the sputtering yield compared to physical sputtering alone.
- Precision and Control: The process allows for precise control over the chemical composition and properties of the deposited films.
- Versatility: It can be used with a wide range of materials, including metals, semiconductors, and insulators.
-
Comparison with Physical Sputtering:
- Energy Transfer: Physical sputtering relies on kinetic energy transfer, while chemical sputtering involves both kinetic energy and chemical energy.
- Volatility of Products: In chemical sputtering, the ejected material is often in the form of volatile compounds, whereas physical sputtering ejects neutral atoms or molecules.
- Process Conditions: Chemical sputtering typically requires reactive gases and specific gas pressures, while physical sputtering uses inert gases like argon.
-
Challenges and Limitations:
- Reaction Control: The chemical reactions must be carefully controlled to avoid unwanted byproducts or over-etching.
- Gas Purity: Impurities in the reactive gases can affect the quality of the deposited films.
- Equipment Complexity: Chemical sputtering systems may require additional components, such as gas flow controllers and reactive gas sources.
-
Examples of Chemical Sputtering Reactions:
-
Silicon Sputtering with Oxygen:
- Reaction: Si + O₂ → SiO₂ (volatile silicon dioxide)
- Application: Used in the deposition of silicon dioxide films for semiconductor devices.
-
Titanium Sputtering with Nitrogen:
- Reaction: Ti + N₂ → TiN (titanium nitride)
- Application: Used for wear-resistant coatings on cutting tools.
-
Silicon Sputtering with Oxygen:
-
Future Trends in Chemical Sputtering:
- Advanced Materials: Research is ongoing to develop new materials and coatings with unique properties, such as superconductors or biocompatible films.
- Green Technologies: Efforts are being made to use environmentally friendly gases and reduce the environmental impact of chemical sputtering processes.
- Automation and AI: Integration of automation and AI for real-time monitoring and control of chemical sputtering processes to improve efficiency and reproducibility.
By understanding the principles and applications of chemical sputtering, equipment and consumable purchasers can make informed decisions about the materials and processes best suited for their specific needs.
Summary Table:
Aspect | Chemical Sputtering |
---|---|
Definition | A process involving chemical reactions between ions and target material to form volatile compounds. |
Mechanism | Reactive ions (e.g., O₂, N₂, CF₄) bombard the target, forming volatile compounds for material removal. |
Applications | Semiconductor manufacturing, optical coatings, wear-resistant coatings. |
Advantages | Enhanced material removal, precise control, versatility with various materials. |
Challenges | Requires careful reaction control, high gas purity, and complex equipment. |
Comparison to Physical Sputtering | Involves chemical energy and volatile compounds, unlike physical sputtering's kinetic energy transfer. |
Discover how chemical sputtering can optimize your material deposition processes—contact our experts today!