A cold press machine, specifically in the context of cold isostatic pressing (CIP), is a device used to apply uniform pressure to powdered materials at room temperature or slightly elevated temperatures (typically below 93°C). This process uses a liquid medium, such as water, oil, or a glycol mixture, to transmit pressure evenly across the material. The primary purpose of cold isostatic pressing is to form "raw" parts that have enough structural integrity to be handled and further processed. These parts are then typically sintered to achieve their final strength and density. Unlike hot isostatic pressing (HIP), which operates at high temperatures and is used for densifying castings and metal products, CIP is conducted at lower temperatures, making it suitable for forming green parts from powders.
Key Points Explained:
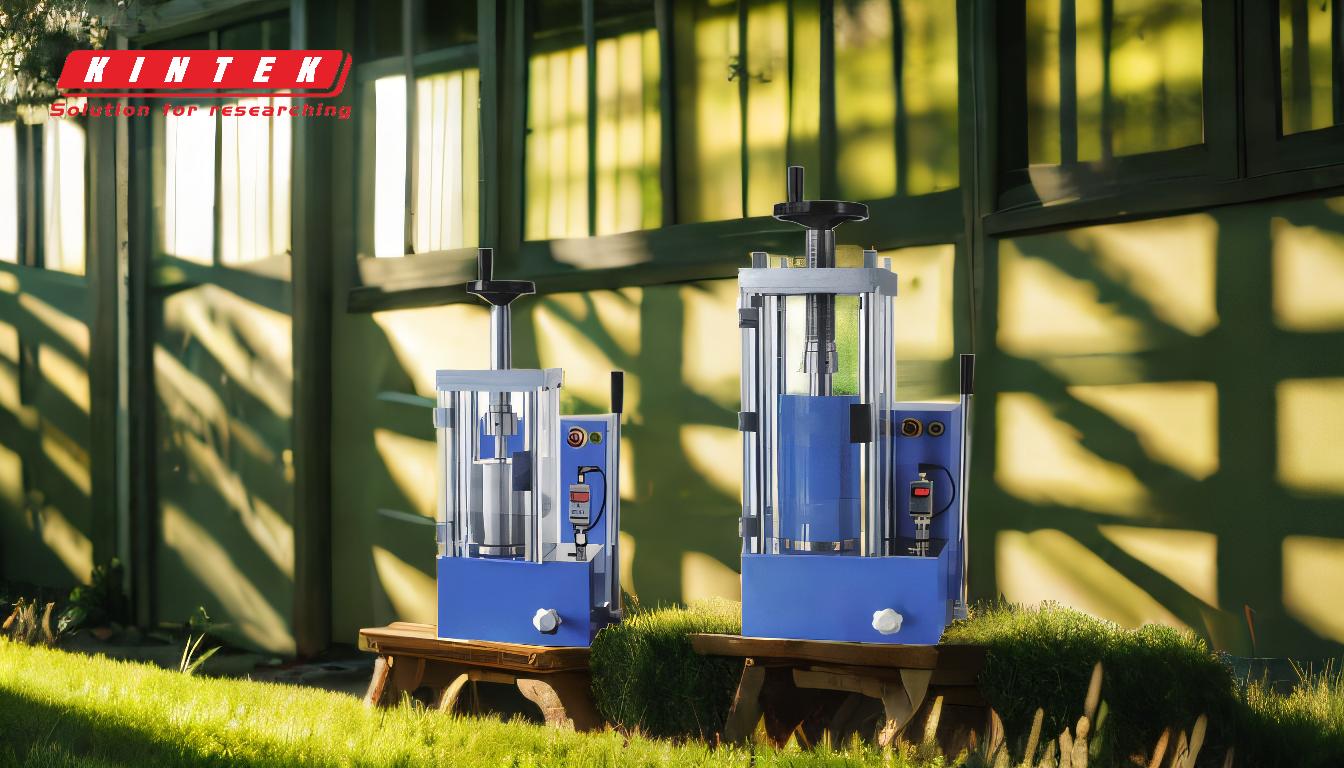
-
Definition and Purpose of Cold Press Machine:
- A cold press machine is used in cold isostatic pressing (CIP) to apply uniform pressure to powdered materials.
- The purpose is to form raw parts that can be handled and processed further, typically through sintering.
-
Temperature Range:
- CIP operates at room temperature or slightly higher temperatures, usually below 93°C.
- This is in contrast to hot isostatic pressing (HIP), which requires much higher temperatures for densification.
-
Liquid Medium:
- The pressure in CIP is applied using a liquid medium such as water, oil, or a glycol mixture.
- This liquid medium ensures that the pressure is distributed evenly across the material, leading to uniform compaction.
-
Forming Raw Parts:
- The primary outcome of CIP is the creation of raw or "green" parts.
- These parts have sufficient strength for handling but require further processing, such as sintering, to achieve their final mechanical properties.
-
Comparison with Hot Isostatic Pressing (HIP):
- CIP is conducted at lower temperatures and is used for forming parts from powders.
- HIP, on the other hand, is used at high temperatures for densifying castings and metal products, often to eliminate porosity and improve mechanical properties.
-
Applications:
- CIP is widely used in industries where uniform compaction of powdered materials is required, such as in the production of ceramics, metals, and composites.
- It is particularly useful for materials that are sensitive to high temperatures or for parts that require complex shapes and uniform density.
-
Advantages of Cold Isostatic Pressing:
- Uniform pressure application leads to consistent density and mechanical properties in the final product.
- Suitable for a wide range of materials, including those that are sensitive to high temperatures.
- Capable of producing complex shapes with high precision.
-
Limitations:
- The raw parts produced by CIP require additional processing (e.g., sintering) to achieve final strength.
- The process may be slower compared to other pressing methods due to the need for uniform pressure application.
By understanding these key points, a purchaser of equipment or consumables can better evaluate whether a cold press machine is suitable for their specific needs, particularly in applications requiring uniform compaction of powdered materials at lower temperatures.
Summary Table:
Aspect | Details |
---|---|
Purpose | Forms raw parts from powdered materials for further processing. |
Temperature Range | Room temperature or slightly elevated (typically below 93°C). |
Liquid Medium | Water, oil, or glycol mixture for uniform pressure distribution. |
Applications | Ceramics, metals, composites; ideal for temperature-sensitive materials. |
Advantages | Uniform density, suitable for complex shapes, works with sensitive materials. |
Limitations | Requires sintering for final strength; slower process. |
Learn how a cold press machine can optimize your material compaction—contact our experts today!