Hydraulic systems operate across a wide range of pressures, and what is considered "high pressure" can vary depending on the application and industry standards. Generally, high-pressure hydraulics refers to systems that operate at pressures significantly above standard levels, often exceeding 2,000 psi (pounds per square inch). These systems are designed to handle heavy loads, provide precise control, and deliver high power output. High-pressure hydraulics are commonly used in industries such as construction, manufacturing, and aerospace, where robust performance is required. However, the definition of high pressure can differ based on the context, with some industries considering pressures above 5,000 psi or even 10,000 psi as high. The design, components, and safety measures of high-pressure hydraulic systems must be carefully engineered to ensure reliability and safety.
Key Points Explained:
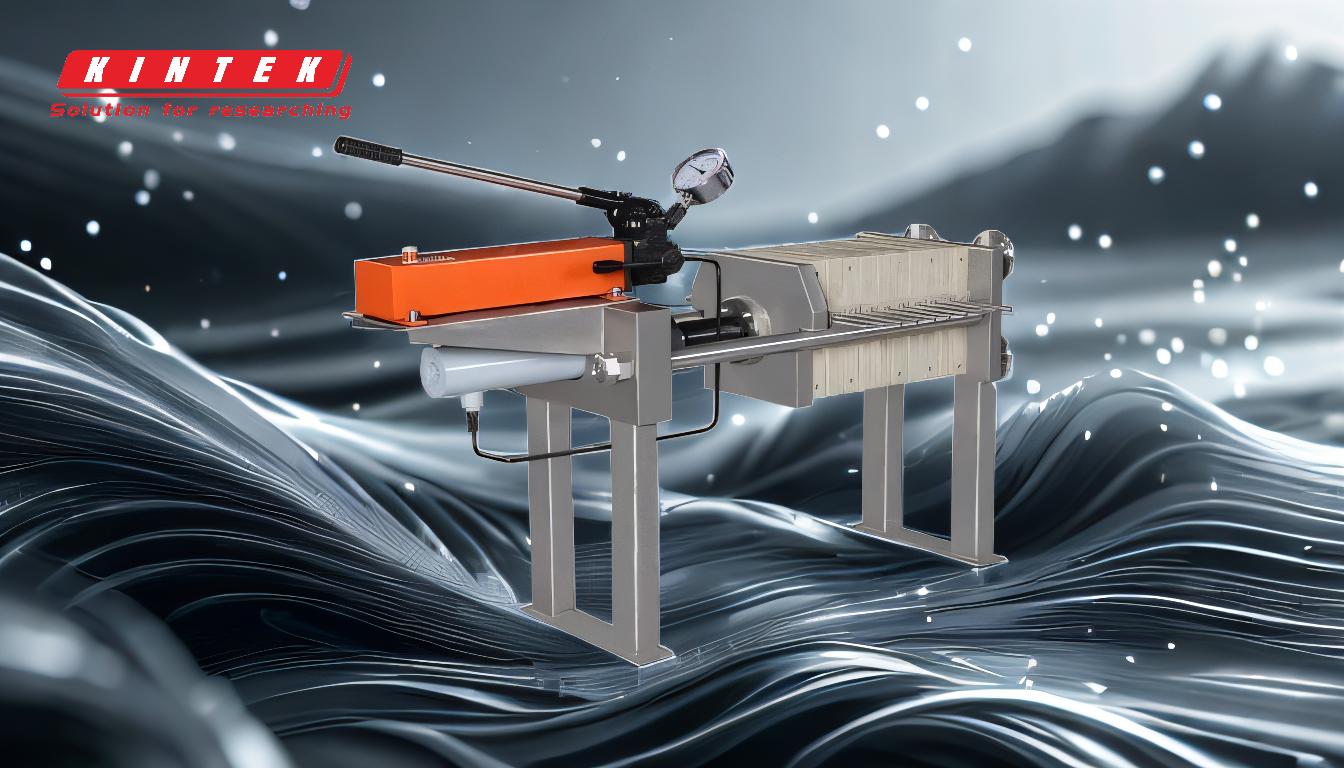
-
Definition of High Pressure in Hydraulics:
- High pressure in hydraulics typically refers to systems operating above 2,000 psi. However, this threshold can vary depending on the industry and specific application. For example:
- In mobile hydraulics (e.g., construction equipment), pressures above 3,000 psi are often considered high.
- In industrial hydraulics, pressures exceeding 5,000 psi may be classified as high.
- In specialized applications like aerospace or high-performance machinery, pressures above 10,000 psi are sometimes required.
- High pressure in hydraulics typically refers to systems operating above 2,000 psi. However, this threshold can vary depending on the industry and specific application. For example:
-
Applications of High-Pressure Hydraulics:
- High-pressure hydraulic systems are used in demanding applications where high force and precision are essential. Examples include:
- Construction Equipment: Excavators, bulldozers, and cranes rely on high-pressure hydraulics to lift heavy loads and perform precise movements.
- Manufacturing: Hydraulic presses and injection molding machines use high-pressure systems to shape materials with accuracy.
- Aerospace: Aircraft landing gear and control systems often operate at high pressures to ensure reliability and safety.
- Oil and Gas: Hydraulic fracturing (fracking) equipment operates at extremely high pressures to extract resources from deep underground.
- High-pressure hydraulic systems are used in demanding applications where high force and precision are essential. Examples include:
-
Components Designed for High Pressure:
- High-pressure hydraulic systems require specialized components to withstand the stresses and deliver consistent performance. Key components include:
- Pumps: High-pressure hydraulic pumps are designed to generate and maintain elevated pressures without failure.
- Cylinders and Actuators: These must be robust to handle the forces generated by high-pressure fluids.
- Hoses and Fittings: High-pressure hoses and fittings are reinforced to prevent leaks or bursts under extreme conditions.
- Valves: Precision valves are used to control the flow and pressure of hydraulic fluid in high-pressure systems.
- High-pressure hydraulic systems require specialized components to withstand the stresses and deliver consistent performance. Key components include:
-
Safety Considerations:
- Operating at high pressures introduces significant safety risks, such as fluid leaks, component failure, or catastrophic bursts. To mitigate these risks:
- Material Selection: Components must be made from high-strength materials capable of withstanding high pressures.
- Pressure Relief Valves: These are essential to prevent over-pressurization and protect the system from damage.
- Regular Maintenance: High-pressure systems require frequent inspection and maintenance to ensure all components are in good condition.
- Training: Operators and maintenance personnel must be trained to handle high-pressure systems safely.
- Operating at high pressures introduces significant safety risks, such as fluid leaks, component failure, or catastrophic bursts. To mitigate these risks:
-
Industry Standards and Regulations:
- High-pressure hydraulic systems are subject to industry standards and regulations to ensure safety and performance. Examples include:
- ISO Standards: The International Organization for Standardization provides guidelines for hydraulic system design and operation.
- SAE Standards: The Society of Automotive Engineers sets standards for hydraulic components used in mobile and industrial applications.
- OSHA Regulations: In the United States, the Occupational Safety and Health Administration outlines safety requirements for hydraulic systems in the workplace.
- High-pressure hydraulic systems are subject to industry standards and regulations to ensure safety and performance. Examples include:
-
Advantages of High-Pressure Hydraulics:
- High-pressure systems offer several benefits, including:
- Higher Power Density: They can deliver more force in a smaller package, making them ideal for space-constrained applications.
- Improved Efficiency: High-pressure systems often operate more efficiently, reducing energy consumption.
- Precision Control: They enable precise control of movements, which is critical in applications like robotics and manufacturing.
- High-pressure systems offer several benefits, including:
-
Challenges of High-Pressure Hydraulics:
- Despite their advantages, high-pressure systems come with challenges:
- Cost: High-pressure components are more expensive due to the need for advanced materials and engineering.
- Complexity: These systems are more complex to design, install, and maintain.
- Safety Risks: The potential for accidents due to high pressures requires rigorous safety protocols.
- Despite their advantages, high-pressure systems come with challenges:
By understanding these key points, equipment and consumable purchasers can make informed decisions when selecting high-pressure hydraulic systems and components. Whether for heavy-duty construction equipment or precision industrial machinery, high-pressure hydraulics play a critical role in modern engineering and technology.
Summary Table:
Aspect | Details |
---|---|
Definition | Typically above 2,000 psi, but varies by industry (e.g., 3,000–10,000+ psi). |
Applications | Construction, manufacturing, aerospace, oil and gas. |
Key Components | Pumps, cylinders, hoses, fittings, valves. |
Safety Measures | High-strength materials, pressure relief valves, regular maintenance. |
Advantages | Higher power density, improved efficiency, precision control. |
Challenges | Higher cost, increased complexity, safety risks. |
Need expert advice on high-pressure hydraulic systems? Contact us today for tailored solutions!