Controlled atmosphere in heat treatment refers to the use of specific gas environments within a furnace to achieve precise material properties and prevent undesirable chemical reactions during heating and cooling processes. This technique is essential for improving the quality, durability, and performance of metal parts. By controlling the atmosphere, processes like oxidation, decarburization, and surface hardening can be managed effectively. The use of an atmosphere box furnace is a common method to achieve this, as it provides a tightly sealed environment with precise temperature and gas composition control. This approach offers numerous advantages, including enhanced material properties, energy efficiency, and improved productivity.
Key Points Explained:
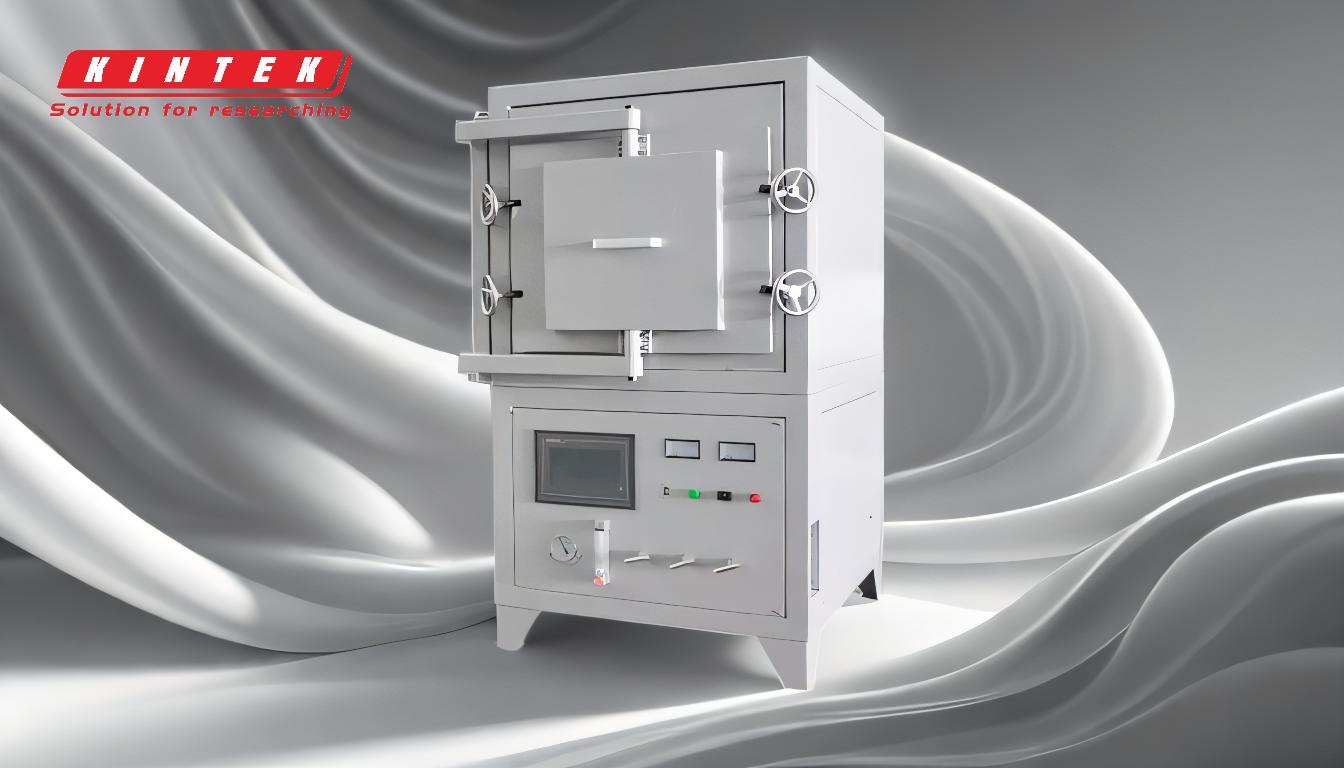
-
Prevention of Oxidation and Decarburization:
- A controlled atmosphere prevents the workpiece from reacting with oxygen, carbon dioxide, or water vapor in the air, which can lead to oxidation (rust) or decarburization (loss of carbon from the surface). This is critical for maintaining the integrity and mechanical properties of the material.
- For example, in steel heat treatment, controlling the levels of O2, CO, and water vapor ensures the workpiece remains free from oxidation or decarburization, preserving its hardness and strength.
-
Surface Property Enhancement:
- Controlled atmospheres enable precise control of surface characteristics, such as carbon content. This is particularly important for processes like carburizing (adding carbon to the surface) or nitriding (adding nitrogen), which improve wear resistance and fatigue strength.
- The atmosphere acts as a carrier for key elements that chemically react with the surface, enhancing its properties without compromising the core material.
-
Special Heat Treatment Processes:
- Controlled atmospheres facilitate advanced heat treatment techniques, such as decarburization, carbon reinforcement removal, and surface hardening. These processes are essential for achieving specific material properties required in industries like automotive, aerospace, and tool manufacturing.
-
Improved Efficiency and Productivity:
- Using a controlled atmosphere reduces the need for post-treatment cleaning and machining, saving time and resources. It also improves labor productivity by automating and streamlining the heat treatment process.
- An atmosphere box furnace offers better furnace control, higher throughput, and reduced labor demands compared to traditional methods like box or salt bath furnaces.
-
Energy Savings and Cost Efficiency:
- Controlled atmosphere furnaces are designed to be energy-efficient, with features like thermal homogeneity, accurate temperature controls, and safety devices. These features reduce operating costs while maintaining high performance.
- The ability to process parts of all shapes and sizes further enhances their versatility and cost-effectiveness.
-
Consistency and Quality Assurance:
- A controlled atmosphere ensures consistent heating and cooling rates, which are critical for achieving uniform material properties. This consistency is essential for producing parts that meet strict quality standards.
- For example, in a laboratory setting, a controlled atmosphere lab furnace provides precise temperature control and a tightly sealed environment, ensuring successful outcomes for material processing experiments.
-
Versatility and Applications:
- Controlled atmosphere heat treatment is applicable to a wide range of materials and industries, including steel, aluminum, and titanium. It is used in processes like annealing, hardening, tempering, and brazing.
- The ability to create protective or reactive atmospheres makes it suitable for specialized applications, such as creating oxide-free surfaces or achieving specific material microstructures.
In summary, controlled atmosphere heat treatment is a sophisticated technique that leverages precise gas environments to enhance material properties, prevent defects, and improve process efficiency. The use of an atmosphere box furnace is a key enabler of this process, offering advanced control and versatility for a wide range of industrial applications.
Summary Table:
Key Benefits | Description |
---|---|
Prevents Oxidation & Decarburization | Protects materials from rust and carbon loss, ensuring strength and durability. |
Enhances Surface Properties | Improves wear resistance and fatigue strength through carburizing or nitriding. |
Facilitates Special Processes | Enables advanced techniques like surface hardening and carbon reinforcement. |
Boosts Efficiency & Productivity | Reduces post-treatment cleaning and machining, saving time and resources. |
Saves Energy & Costs | Energy-efficient design with precise temperature and gas controls. |
Ensures Consistency & Quality | Provides uniform heating and cooling for consistent material properties. |
Versatile Applications | Suitable for steel, aluminum, titanium, and processes like annealing or brazing. |
Discover how controlled atmosphere heat treatment can optimize your processes—contact us today for expert advice!