Conventional sintering is a widely used manufacturing process that transforms powdered materials into dense, solid bodies by applying heat and pressure at temperatures below the material's melting point. This process is essential in industries such as powder metallurgy, ceramics, and plastics, where it is used to create strong, durable, and complex-shaped components. Sintering involves blending fine powders, compacting them into a desired shape, and then heating the compacted part in a controlled environment to bond the particles together. The result is a structurally sound material with improved mechanical properties, making it suitable for various applications.
Key Points Explained:
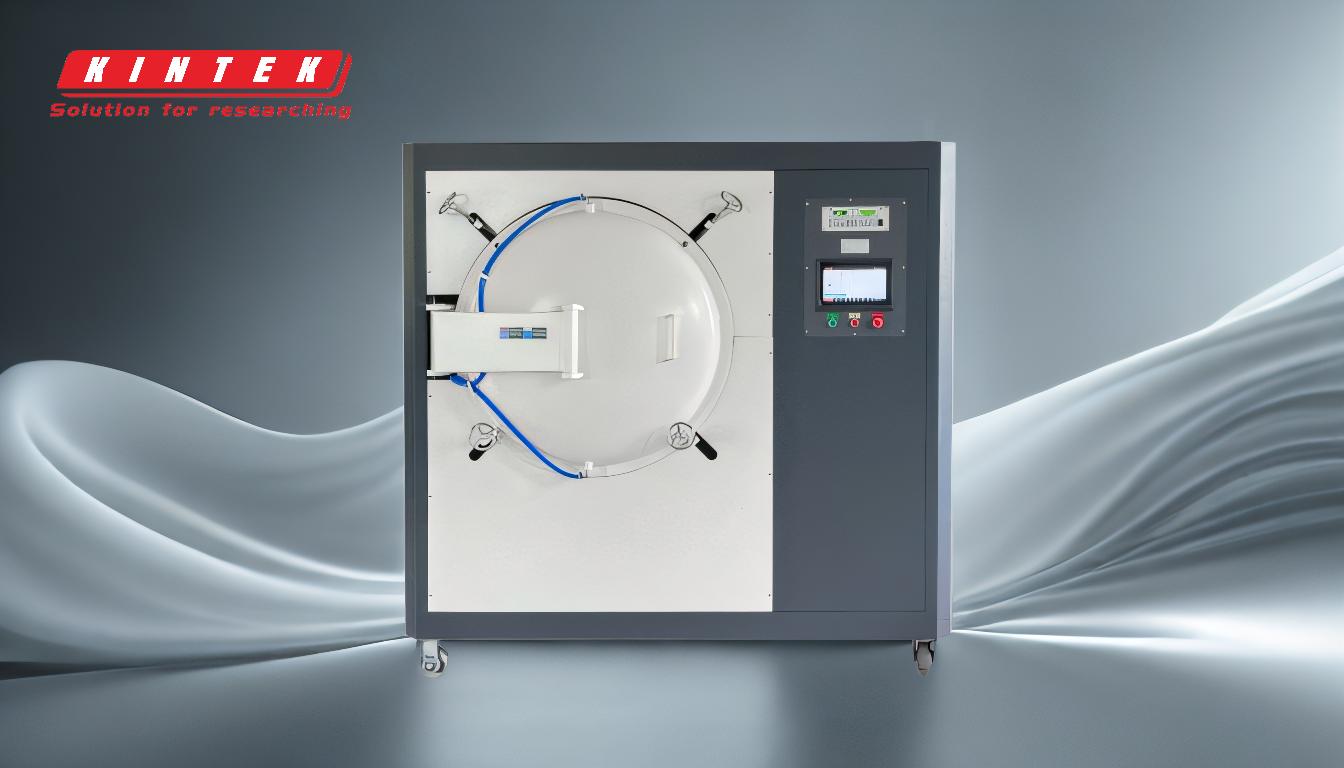
-
Definition of Conventional Sintering:
- Sintering is a process that transforms powdered materials into dense, solid bodies by applying heat and pressure below the material's melting point.
- It is used to bond adjacent powder particle surfaces, creating a cohesive mass without melting the material.
-
Steps Involved in the Sintering Process:
- Blending: Fine powdered metals or other materials are mixed to achieve a uniform composition.
- Compaction: The blended powder is pressed into a desired shape using mechanical or hydraulic presses.
- Sintering: The compacted part is heated in a controlled atmosphere furnace to bond the particles together, forming a solid mass.
-
Materials Suitable for Sintering:
- Metals (e.g., iron, copper, tungsten, molybdenum)
- Ceramics
- Plastics
- Composite materials
-
Key Characteristics of Sintering:
- Temperature Control: Sintering occurs at temperatures below the material's melting point to prevent liquefaction.
- Atom Diffusion: Atoms diffuse across particle boundaries, fusing them together to form a solid piece.
- Enhanced Properties: The process improves the material's strength, hardness, and durability.
-
Applications of Sintering:
- Powder Metallurgy: Used to produce metal components with complex shapes, such as gears, bearings, and automotive parts.
- Ceramics: Sintering is essential in manufacturing ceramic tiles, insulators, and refractory materials.
- Plastics: Used to create durable plastic components with high precision.
-
Advantages of Sintering:
- Cost-Effective: Reduces material waste and allows for the production of near-net-shape components.
- Material Versatility: Suitable for a wide range of materials, including those with high melting points.
- Improved Properties: Enhances mechanical strength, wear resistance, and thermal stability.
-
Challenges and Limitations:
- Porosity: Sintered parts may have residual porosity, which can affect their mechanical properties.
- Dimensional Accuracy: Achieving precise dimensions can be challenging due to shrinkage during sintering.
- Material Limitations: Not all materials are suitable for sintering, especially those with low melting points or poor thermal stability.
-
Comparison with Other Manufacturing Processes:
- Casting: Sintering avoids the need for melting, making it suitable for materials with high melting points.
- Machining: Sintering produces near-net-shape components, reducing the need for extensive machining.
- Additive Manufacturing: Sintering is often used in conjunction with 3D printing to create dense, functional parts.
By understanding these key points, equipment and consumable purchasers can make informed decisions about the suitability of sintering for their specific applications, ensuring optimal performance and cost-effectiveness.
Summary Table:
Aspect | Details |
---|---|
Definition | Transforms powdered materials into dense solids using heat and pressure. |
Key Steps | Blending, compaction, and sintering in a controlled environment. |
Materials | Metals, ceramics, plastics, and composites. |
Applications | Powder metallurgy, ceramics, plastics, and automotive components. |
Advantages | Cost-effective, versatile, and improves mechanical properties. |
Challenges | Porosity, dimensional accuracy, and material limitations. |
Discover how sintering can optimize your manufacturing process—contact our experts today!