DC magnetron sputtering is a widely used physical vapor deposition (PVD) technique for creating thin films on substrates. It operates in a vacuum chamber where a target material is bombarded by ionized gas molecules, typically argon, causing atoms to be ejected and deposited onto a substrate. This method leverages a magnetic field orthogonal to the electric field, enhancing plasma confinement and increasing deposition rates. It is highly versatile, allowing for the deposition of various materials, including metals and insulators, and is commonly used in optical and electrical applications. While it offers advantages like high deposition rates and good uniformity, challenges such as non-uniform target erosion exist.
Key Points Explained:
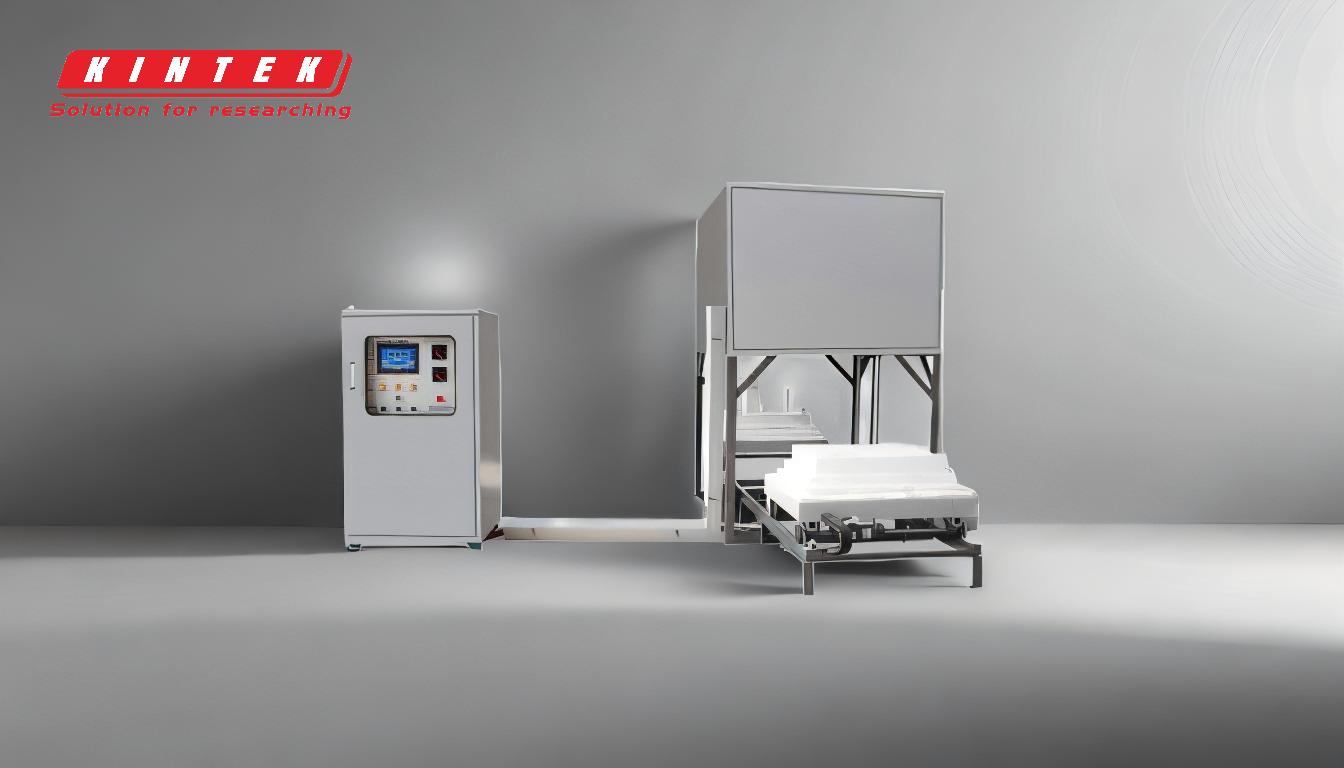
-
Basic Principle of DC Magnetron Sputtering:
- DC magnetron sputtering is a PVD technique where a target material is bombarded by ionized gas molecules (typically argon) in a vacuum chamber.
- The process involves the ejection of target atoms due to ion collisions, which then deposit onto a substrate to form a thin film.
-
Role of Magnetic and Electric Fields:
- A magnetic field is established orthogonal to the electric field on the target surface. This configuration confines electrons near the target, increasing plasma density and enhancing the sputtering process.
- The magnetic field helps improve deposition rates and plasma dissociation rates compared to traditional dipole sputtering.
-
Process Steps:
- The vacuum chamber is evacuated to create a low-pressure environment.
- Inert gas (usually argon) is introduced into the chamber.
- A high negative voltage is applied between the cathode (target) and anode, ionizing the argon gas and creating a plasma.
- Positive argon ions from the plasma collide with the negatively charged target, ejecting target atoms.
- Ejected atoms travel through the vacuum and deposit onto the substrate, forming a thin film.
-
Advantages of DC Magnetron Sputtering:
- High Deposition Rates: Achieves faster thin-film deposition compared to other methods.
- Good Uniformity: Ensures consistent film thickness across the substrate.
- Versatility: Can deposit a wide range of materials, including metals, insulators, and compounds.
- Low Pressure Operation: Reduces contamination and improves film quality.
-
Challenges and Limitations:
- Non-Uniform Target Erosion: The magnetic field can cause uneven erosion of the target, reducing its usable life.
- Substrate Damage Risk: High-energy ions may damage sensitive substrates if not properly controlled.
-
Applications:
- Widely used in optical coatings (e.g., anti-reflective coatings) and electrical applications (e.g., semiconductor devices).
- Suitable for depositing metallic and insulating thin films for various industrial and research purposes.
-
Comparison with Other Sputtering Methods:
- Ion Beam Sputtering: Offers precise control but is slower and more expensive.
- Diode Sputtering: Simpler but less efficient and slower than magnetron sputtering.
- DC magnetron sputtering strikes a balance between efficiency, cost, and versatility.
By leveraging magnetic fields and controlled plasma environments, DC magnetron sputtering remains a cornerstone of thin-film deposition technology, offering a reliable and efficient solution for a wide range of applications.
Summary Table:
Aspect | Details |
---|---|
Basic Principle | A PVD technique using ionized gas to eject target atoms onto a substrate. |
Key Components | Vacuum chamber, magnetic field, electric field, target material, argon gas. |
Advantages | High deposition rates, good uniformity, versatility, low-pressure operation. |
Challenges | Non-uniform target erosion, risk of substrate damage. |
Applications | Optical coatings, semiconductor devices, and industrial thin-film deposition. |
Comparison with Others | More efficient and versatile than diode sputtering, faster than ion beam. |
Discover how DC magnetron sputtering can enhance your thin-film processes—contact our experts today!