Deposition time refers to the duration required to deposit a specific thickness or amount of material onto a substrate during a deposition process, such as sputtering or plasma deposition. It is influenced by factors like deposition rate, target-substrate distance, power, temperature, and the physical properties of the target material. Optimizing deposition time involves balancing these factors to achieve uniformity, efficiency, and cost-effectiveness. Understanding deposition time is crucial for process control, ensuring desired material properties, and minimizing resource consumption.
Key Points Explained:
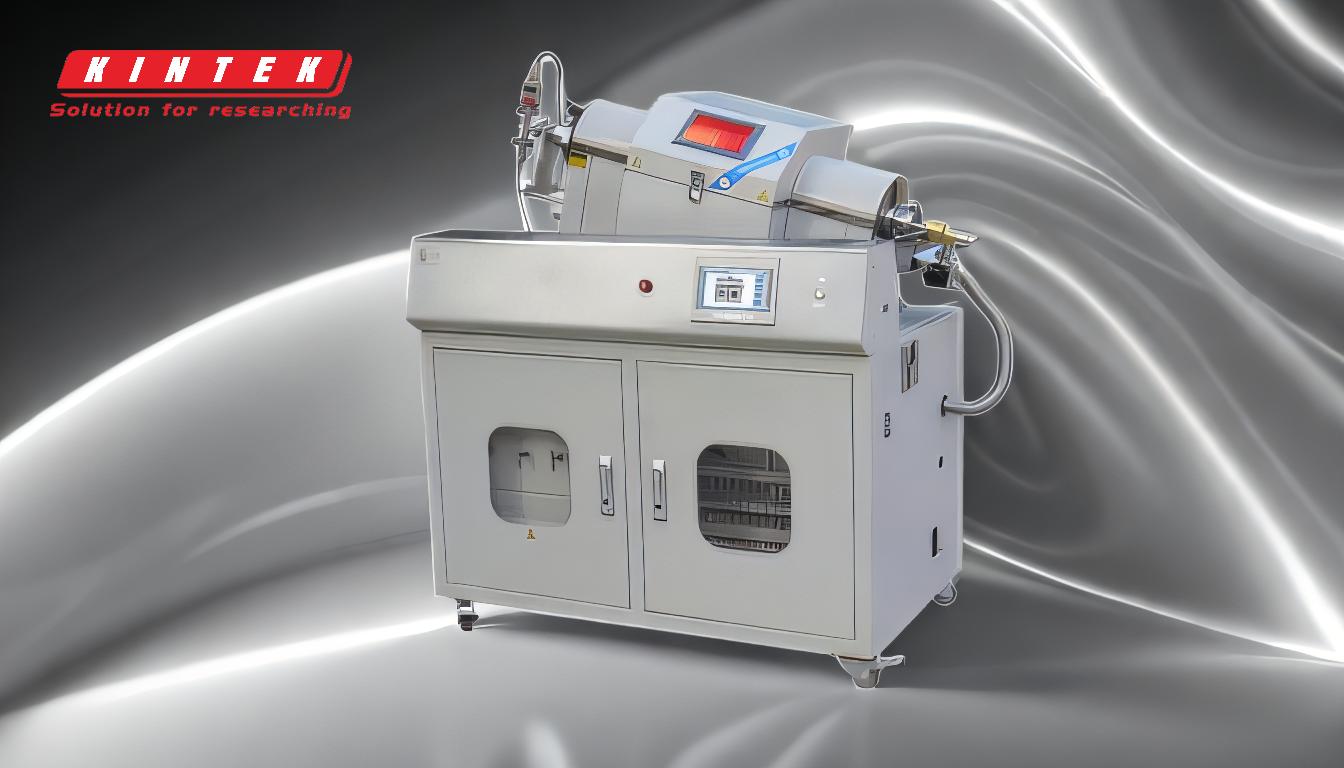
-
Definition of Deposition Time:
- Deposition time is the period required to deposit a specific thickness or amount of material onto a substrate.
- It is a critical parameter in processes like sputtering and plasma deposition, where material is transferred from a target to a substrate.
-
Factors Influencing Deposition Time:
-
Deposition Rate: The speed at which material is deposited, influenced by factors like target-substrate distance, power, and temperature.
- A higher deposition rate reduces deposition time, while a lower rate increases it.
- Target-Substrate Distance: Closer distances generally increase deposition rates, reducing deposition time.
- Power and Temperature: Higher power and temperature can enhance deposition rates, thereby decreasing deposition time.
- Physical Properties of Target Material: Materials with higher sputtering yields or easier ionization may deposit faster, reducing deposition time.
-
Deposition Rate: The speed at which material is deposited, influenced by factors like target-substrate distance, power, and temperature.
-
Impact of Deposition Time on Process Quality:
- Thickness Uniformity: Longer deposition times may lead to non-uniform thickness if factors like target-substrate distance or erosion zone size are not optimized.
- Material Composition: Proper deposition time ensures the desired elemental composition and minimizes contamination risks.
- Process Efficiency: Optimizing deposition time can reduce energy consumption and costs associated with assistant gases and reactor occupation.
-
Optimizing Deposition Time:
- Reactor Parameters: Adjusting parameters like power, temperature, and target-substrate distance can optimize deposition time.
- Cleaning and Maintenance: Regular cleaning of the reactor and monitoring of chamber conditions ensure consistent deposition rates and quality.
- Monitoring and Control: Real-time monitoring of plasma characteristics (temperature, composition, density) and elemental composition helps maintain optimal deposition conditions.
-
Practical Considerations for Equipment and Consumable Purchasers:
- Equipment Selection: Choose deposition systems with adjustable parameters to control deposition time effectively.
- Cost Efficiency: Consider systems that minimize energy and gas consumption while maintaining high deposition rates.
- Process Flexibility: Opt for equipment that allows easy adjustments to accommodate different materials and deposition requirements.
By understanding and optimizing deposition time, manufacturers can achieve better process control, improve material quality, and reduce operational costs. This makes it a critical consideration for both process engineers and equipment purchasers.
Summary Table:
Key Factors | Impact on Deposition Time |
---|---|
Deposition Rate | Higher rate reduces time; lower rate increases time. |
Target-Substrate Distance | Closer distance increases rate, reducing time. |
Power and Temperature | Higher power/temperature enhances rate, decreasing time. |
Physical Properties of Target | Materials with higher sputtering yields or easier ionization deposit faster, reducing time. |
Optimization Strategies | Benefits |
Adjust Reactor Parameters | Achieves uniformity and efficiency. |
Regular Cleaning/Maintenance | Ensures consistent deposition rates and quality. |
Real-Time Monitoring | Maintains optimal deposition conditions. |
Optimize your deposition process today—contact our experts for tailored solutions!