Direct current (DC) magnetron sputtering is a highly efficient physical vapor deposition (PVD) technique used to deposit thin films of materials onto substrates. It involves the use of a magnetron, which applies a negative voltage to a target material, attracting positively charged ions from a plasma. These ions bombard the target, causing atoms to be ejected and deposited onto a substrate, forming a thin film. The process is enhanced by magnetic fields that trap electrons, increasing ionization and deposition rates. DC magnetron sputtering is widely used in industries for coating materials like metals, ceramics, and alloys due to its ability to produce uniform, dense, and high-quality films at relatively low temperatures.
Key Points Explained:
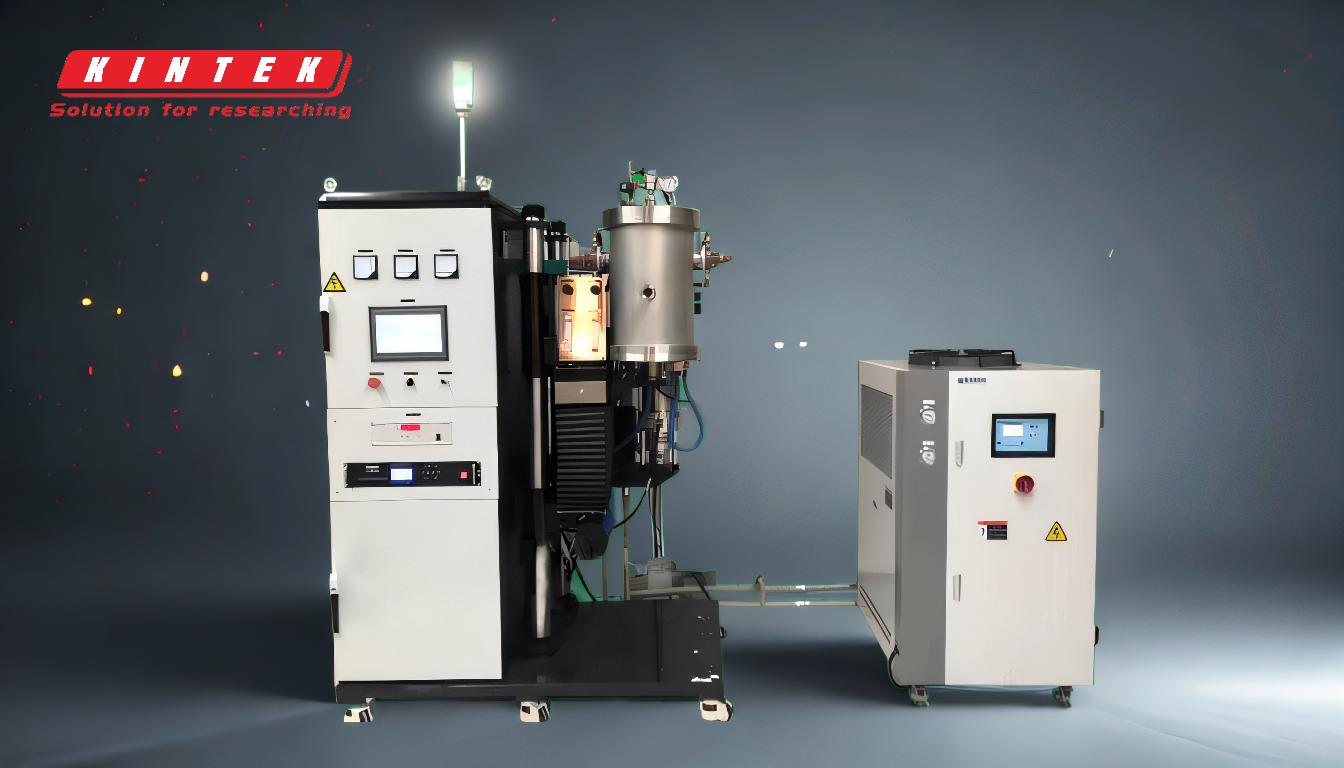
-
Basic Principle of DC Magnetron Sputtering:
- DC magnetron sputtering is a PVD process where a target material is bombarded by ionized gas molecules (usually argon) in a vacuum chamber.
- A negative voltage (typically −300 V or more) is applied to the target, attracting positively charged ions from the plasma.
- When these ions collide with the target, they transfer energy, causing atoms to be ejected (sputtered) from the target surface.
- These ejected atoms travel through the vacuum and deposit onto a substrate, forming a thin film.
-
Role of Magnetic Fields:
- A magnetic field is applied perpendicular to the electric field near the cathode (target).
- This magnetic field traps electrons, forcing them into cycloidal orbits, which increases their path length and the likelihood of collisions with gas atoms.
- The increased ionization enhances the plasma density, leading to higher sputtering rates and more efficient deposition.
-
Components of a DC Magnetron Sputtering System:
- Target (Cathode): The material to be sputtered, held at a negative voltage.
- Anode (Grounded): The substrate holder where the thin film is deposited.
- Vacuum Chamber: Maintains a low-pressure environment for plasma generation and sputtering.
- Magnet Array: Generates the magnetic field necessary for electron trapping and plasma enhancement.
- Gas Inlet: Introduces inert gas (usually argon) into the chamber to create the plasma.
-
Process Steps:
- The chamber is evacuated to create a vacuum.
- Inert gas (argon) is introduced into the chamber.
- A high voltage is applied to the target, creating a plasma of ionized gas atoms, ions, and free electrons.
- The magnetic field traps electrons, increasing ionization and plasma density.
- Positively charged ions are attracted to the negatively charged target, bombarding it and ejecting atoms.
- Ejected atoms travel through the vacuum and deposit onto the substrate, forming a thin film.
-
Advantages of DC Magnetron Sputtering:
- Low Deposition Temperature: Suitable for temperature-sensitive substrates.
- High Deposition Rates: Efficient and fast coating process.
- Uniform and Dense Films: Produces high-quality, uniform coatings.
- Versatility: Can deposit a wide range of materials, including metals, ceramics, and alloys.
- Scalability: Capable of coating large areas and complex geometries.
-
Applications:
- Optical Coatings: Used in lenses, mirrors, and anti-reflective coatings.
- Semiconductor Industry: For depositing thin films in microelectronics.
- Decorative Coatings: Applied to consumer goods for aesthetic purposes.
- Protective Coatings: Used to enhance wear resistance, corrosion resistance, and durability of materials.
-
Comparison with Other Sputtering Techniques:
- DC magnetron sputtering is more efficient than traditional diode sputtering due to the use of magnetic fields.
- It operates at lower pressures and higher deposition rates compared to RF (radio frequency) sputtering.
- Unlike reactive sputtering, DC magnetron sputtering does not involve chemical reactions, making it simpler for depositing pure materials.
In summary, DC magnetron sputtering is a versatile and efficient PVD technique that leverages magnetic fields to enhance plasma density and sputtering rates. Its ability to produce high-quality, uniform films at low temperatures makes it a preferred choice for various industrial applications.
Summary Table:
Aspect | Details |
---|---|
Basic Principle | Uses a negative voltage to attract ions, ejecting target atoms onto a substrate. |
Role of Magnetic Fields | Traps electrons, increasing ionization and sputtering rates. |
Key Components | Target, anode, vacuum chamber, magnet array, gas inlet. |
Process Steps | Evacuate chamber, introduce argon, apply voltage, deposit thin film. |
Advantages | Low temperature, high deposition rates, uniform films, versatile, scalable. |
Applications | Optical coatings, semiconductors, decorative and protective coatings. |
Discover how DC magnetron sputtering can enhance your projects—contact us today for expert advice!