Ashing in a muffle furnace is a process where combustible samples are heated at high temperatures in the presence of oxygen to burn off organic material, leaving behind inorganic, non-combustible ash. This process is crucial for analyzing the residual ash, which can provide insights into the composition of the sample. The muffle furnace is designed to ensure uniform heating and efficient airflow, promoting complete combustion and removing smoke. Ashing is commonly used in laboratory settings for applications such as determining the mass of residual material, preparing samples for further analysis, or removing matrix constituents that might interfere with analytical measurements.
Key Points Explained:
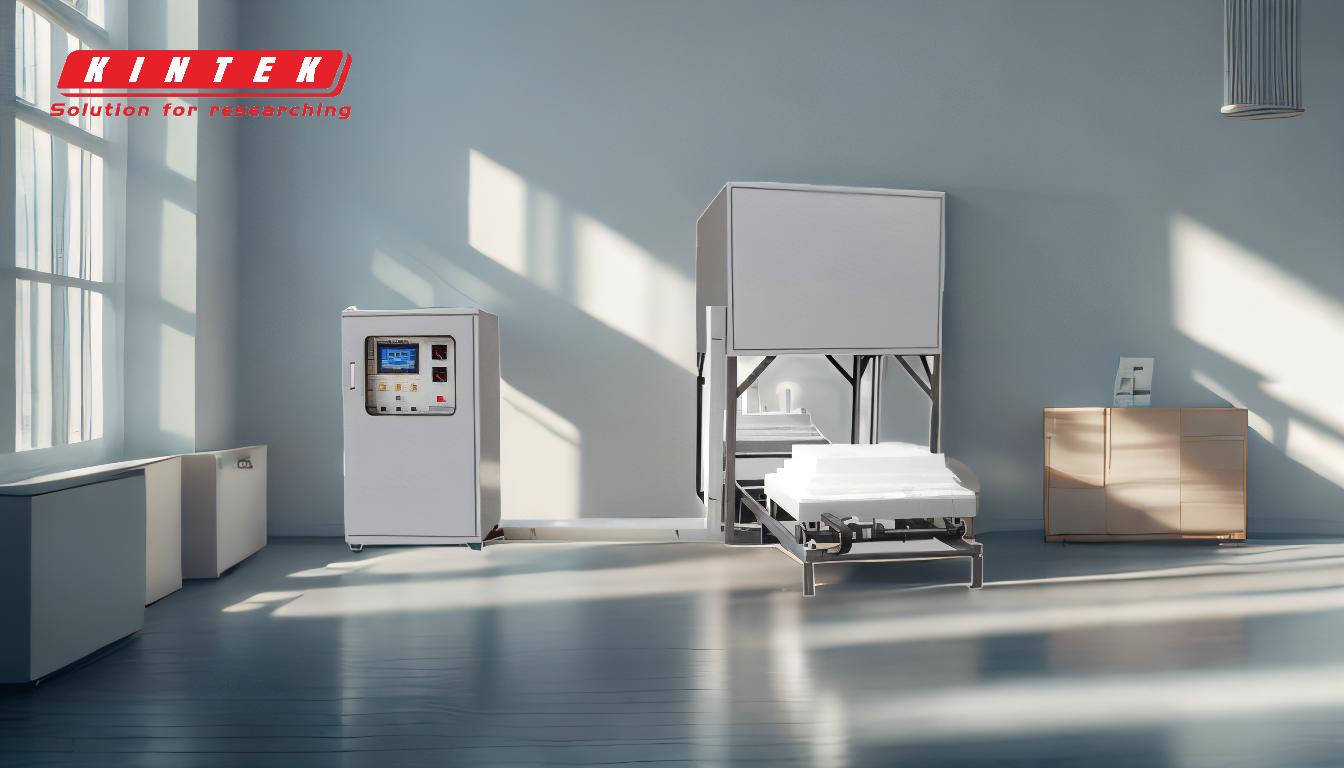
-
Purpose of Ashing in a Muffle Furnace:
- Ashing is primarily used to remove organic material from a sample by heating it at high temperatures in the presence of oxygen. This process leaves behind inorganic, non-combustible ash, which can be analyzed to determine the composition of the sample.
- It is a critical step in sample preparation for various analytical techniques, such as XRF, mass spectroscopy, and ash fusibility tests.
-
Role of the Muffle Furnace:
- A muffle furnace is specifically designed for high-temperature applications, including ashing. It features a heat-resistant inner container (the muffle) that protects the sample from direct exposure to heat, ensuring gentle and uniform heating.
- The furnace uses mechanical convection to direct airflow out of an exhaust muffle, which aids in sample combustion and removes smoke generated during the process. This design eliminates the need for a fume hood in many cases.
-
Applications of Ashing:
- Sample Preparation: Ashing is used to prepare samples for further analysis by removing organic matrix constituents that might interfere with the measurement of the analyte.
- Ash Content Determination: It is commonly used to determine the proportional mass of residual material (ash) in a sample, which is important in industries such as food, pharmaceuticals, and materials science.
- Inorganic Analysis: The resulting ash can be analyzed to characterize inorganic components, providing valuable information about the sample's composition.
-
Process of Ashing:
- The sample is placed in the muffle furnace and heated to high temperatures (typically between 500°C and 900°C) in the presence of oxygen.
- The organic material in the sample combusts, leaving behind inorganic ash. The process is carefully controlled to ensure complete combustion and minimize contamination.
- The resulting ash is then collected and analyzed to determine its composition or used for further testing.
-
Advantages of Using a Muffle Furnace for Ashing:
- Uniform Heating: The muffle furnace ensures that the sample is heated uniformly, which is essential for consistent and accurate results.
- Efficient Airflow: The furnace's design promotes high airflow through the chamber, aiding in the combustion process and removing smoke, which improves the quality of the ash residue.
- Safety: The muffle furnace's design minimizes the risk of contamination and exposure to harmful fumes, making it a safe option for laboratory use.
-
Comparison with Other Ashing Methods:
- While other methods, such as wet ashing, can also be used to remove organic material, dry ashing in a muffle furnace is often preferred for its simplicity, efficiency, and ability to handle larger sample volumes.
- Wet ashing involves the use of acids and other chemicals, which can introduce contaminants and require additional safety precautions.
In summary, ashing in a muffle furnace is a vital process for removing organic material from samples, leaving behind inorganic ash for analysis. The muffle furnace's design ensures uniform heating, efficient airflow, and safety, making it an essential tool in laboratory settings for sample preparation and analysis.
Summary Table:
Aspect | Details |
---|---|
Purpose | Removes organic material, leaving inorganic ash for analysis. |
Temperature Range | Typically 500°C to 900°C. |
Applications | Sample preparation, ash content determination, inorganic analysis. |
Advantages | Uniform heating, efficient airflow, safety, and minimal contamination. |
Comparison to Wet Ashing | Simpler, more efficient, and safer for larger sample volumes. |
Ready to optimize your lab processes with a muffle furnace? Contact us today to learn more!