Electron-beam (e-beam) technology is a versatile and precise tool used across a wide range of industries and applications. It leverages the properties of electron beams to achieve high-temperature resistance, wear resistance, chemical resistance, and specific optical properties. Key applications include semiconductor manufacturing, micro- and nanoelectromechanical systems, microscopy, and the fabrication of polymers. E-beam evaporation and coating are particularly valuable in industries like aerospace, automotive, energy, and electronics, where they are used to create durable, high-performance coatings and optical thin films. This technology is also essential in processes like electron lithography, cable isolation treatment, and the curing of color printing.
Key Points Explained:
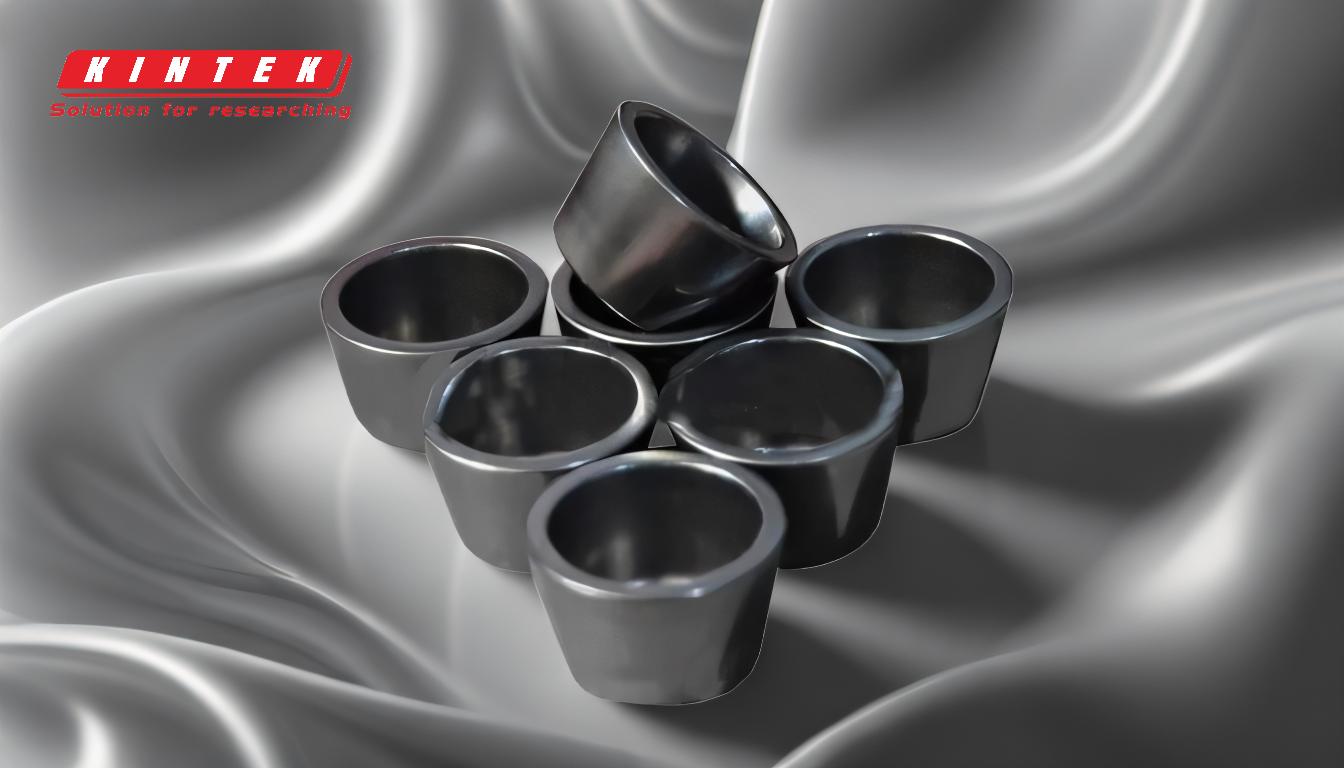
-
Semiconductor Manufacturing:
- E-beam technology is crucial in the production of semiconductors, where it is used for precise patterning and lithography. This allows for the creation of sub-micrometer and nano-dimensional images, which are essential for modern microelectronics.
-
Micro- and Nanoelectromechanical Systems (MEMS/NEMS):
- E-beam technology is employed in the fabrication and modification of MEMS and NEMS. These systems are used in a variety of applications, including sensors, actuators, and other miniature devices.
-
Microscopy:
- Electron beams are used in microscopy to achieve high-resolution imaging. This is particularly useful in materials science and biology, where detailed images of tiny structures are required.
-
Cable Isolation Treatment:
- E-beam technology is used to treat cable isolation, enhancing its durability and resistance to environmental factors. This is important for ensuring the longevity and reliability of electrical cables.
-
Electron Lithography:
- This process involves using electron beams to create intricate patterns on surfaces. It is widely used in the production of microelectronics and other high-precision components.
-
Microelectronics and Color Printing:
- E-beam curing is used in microelectronics and color printing to achieve high-quality, durable finishes. This process is essential for producing components with specific optical and mechanical properties.
-
Fabrication and Modification of Polymers:
- E-beam technology is used to fabricate and modify polymers, including liquid-crystal films. This is important for creating materials with specific properties, such as flexibility, transparency, and durability.
-
E-beam Evaporation and Coating:
- Aerospace and Automotive Industries: E-beam evaporation is used to create high-temperature and wear-resistant coatings, which are essential for components exposed to extreme conditions.
- Energy and Construction: This technology is used to produce coatings that offer chemical resistance and durability, making them suitable for harsh environments.
- Maritime Industry: E-beam coatings are used to create chemical barriers for marine fittings, protecting them from corrosive environments.
- Optical Thin Films: E-beam evaporation is used to produce optical thin films for applications like laser optics, solar panels, eyeglasses, and architectural glass. These films provide conductive, reflective, and transmissive qualities.
-
Directional Coating and Fine Layers:
- E-beam coating is highly directional and produces very fine layers. This makes it ideal for applications requiring precise coating, such as shadowing and replicas.
-
Consumer Goods:
- E-beam technology is also used in the production of consumer goods, where it helps achieve specific optical properties and durability.
In summary, e-beam technology is a critical tool in modern manufacturing and research, offering precision, durability, and versatility across a wide range of applications. Its ability to produce high-performance coatings and intricate patterns makes it indispensable in industries ranging from aerospace to consumer electronics.
Summary Table:
Application | Key Benefits |
---|---|
Semiconductor Manufacturing | Precise patterning, sub-micrometer lithography |
MEMS/NEMS Fabrication | Miniature device creation, sensors, actuators |
Microscopy | High-resolution imaging for materials science and biology |
Cable Isolation Treatment | Enhanced durability and environmental resistance |
Electron Lithography | Intricate patterns for microelectronics and high-precision components |
Microelectronics & Color Printing | Durable finishes, specific optical and mechanical properties |
Polymer Fabrication & Modification | Flexible, transparent, and durable materials |
E-beam Evaporation & Coating | High-performance coatings for aerospace, automotive, energy, and maritime |
Optical Thin Films | Conductive, reflective, and transmissive properties for optics and solar panels |
Consumer Goods | Specific optical properties and durability |
Unlock the potential of e-beam technology for your industry—contact our experts today!