Evaporation in thin film technology is a deposition process where a source material is heated to its evaporation point in a vacuum environment, causing it to vaporize and then condense onto a substrate to form a thin film. This method is widely used in microfabrication and macro-scale applications, such as creating metallized plastic films. The process relies on a vacuum to ensure that vapor particles travel directly to the substrate without contamination, resulting in a uniform and high-quality thin film. The heating can be achieved through electrical resistance, crucibles, or electron beams.
Key Points Explained:
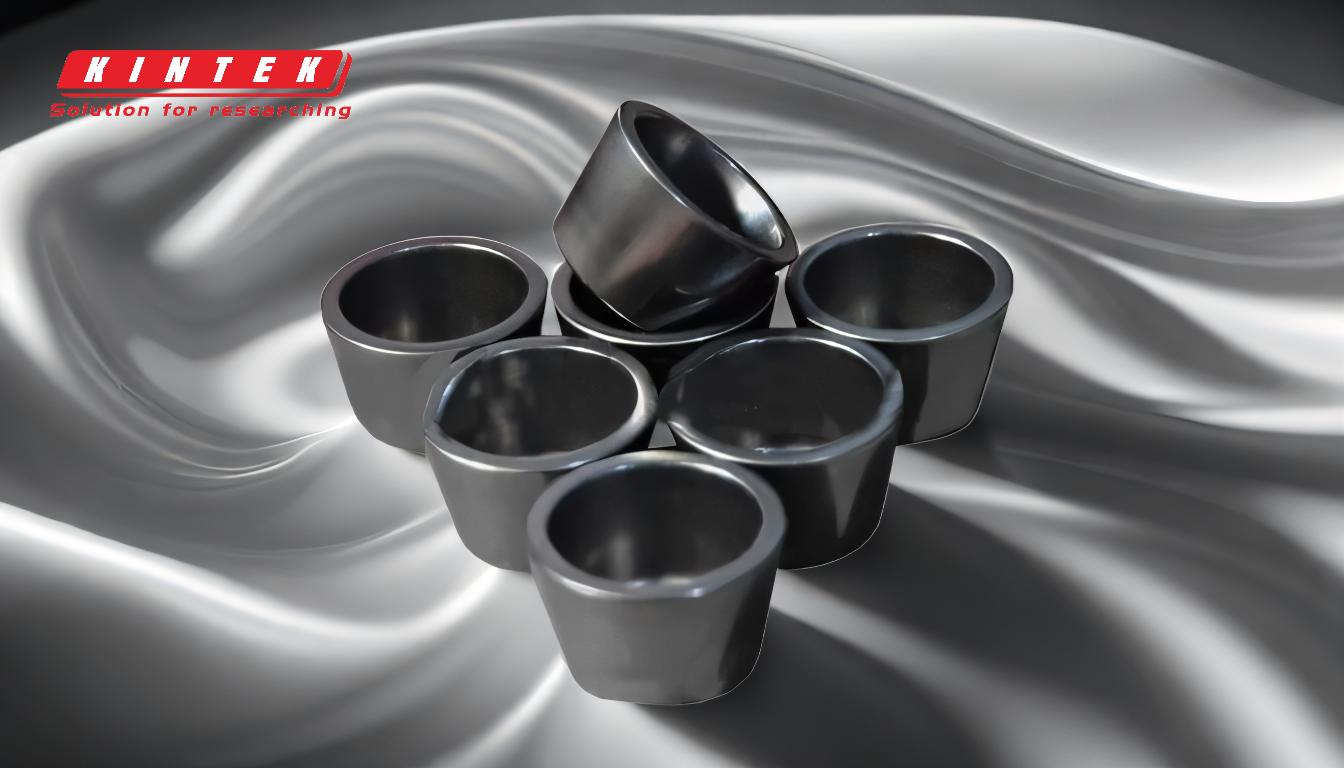
-
Definition of Evaporation in Thin Film Technology:
- Evaporation is a physical vapor deposition (PVD) technique where a source material is heated until it vaporizes in a vacuum. The vaporized material then travels through the vacuum and condenses onto a substrate, forming a thin film.
- This process is analogous to steam condensing on a cold surface, such as water droplets forming on a ceiling after a hot bath.
-
Role of Vacuum in the Process:
- A vacuum environment is critical for the evaporation process. It ensures that vapor particles travel directly to the substrate without interference from air molecules, which could cause contamination or uneven deposition.
- The vacuum also helps maintain the purity of the deposited material and enhances the uniformity of the thin film.
-
Heating Methods for Evaporation:
- Electrical Resistance Heating: The source material is placed on a wire or filament, which is heated electrically until the material evaporates.
- Crucible Heating: The material is placed in a crucible made of a material with a higher melting point, and the crucible is heated to evaporate the source material.
- Electron Beam Heating: A focused electron beam is used to heat and evaporate the source material. This method is particularly useful for materials with very high melting points.
-
Deposition Mechanism:
- Once the source material is vaporized, the vapor particles travel through the vacuum and deposit onto the substrate.
- The particles condense back into a solid state upon contact with the substrate, forming a thin film. The thickness and uniformity of the film depend on factors such as the evaporation rate, substrate temperature, and vacuum pressure.
-
Applications of Evaporation in Thin Film Technology:
- Microfabrication: Used in the production of semiconductors, optical coatings, and electronic devices.
- Macro-Scale Products: Examples include metallized plastic films used in packaging and decorative applications.
- Research and Development: Evaporation is a versatile technique for creating thin films with precise control over thickness and composition.
-
Advantages of Evaporation:
- High purity of deposited films due to the vacuum environment.
- Ability to deposit a wide range of materials, including metals, alloys, and compounds.
- Precise control over film thickness and uniformity.
-
Challenges and Considerations:
- The process requires specialized equipment, including vacuum chambers and heating systems.
- Materials with very high melting points may require advanced heating methods, such as electron beam evaporation.
- The substrate must be carefully prepared to ensure proper adhesion of the thin film.
By understanding these key points, one can appreciate the importance of evaporation in thin film technology and its role in creating high-quality thin films for various applications.
Summary Table:
Aspect | Details |
---|---|
Definition | Physical vapor deposition (PVD) technique using vacuum to create thin films. |
Role of Vacuum | Ensures purity, uniformity, and direct deposition of vapor onto substrate. |
Heating Methods | Electrical resistance, crucible, or electron beam heating. |
Applications | Semiconductors, optical coatings, metallized films, and R&D. |
Advantages | High purity, precise control, and versatility in material deposition. |
Challenges | Requires specialized equipment and careful substrate preparation. |
Discover how evaporation technology can enhance your thin film projects—contact us today for expert guidance!