A filter press is a critical piece of equipment used in various industries for solid-liquid separation. It operates by applying pressure to a slurry, forcing the liquid (filtrate) through filter cloths or plates while retaining the solid particles (filter cake). This process is widely used in industries such as wastewater treatment, chemical processing, mining, and food production. The lab filter press is a smaller-scale version designed for laboratory use, enabling researchers and engineers to test filtration processes before scaling up to industrial applications. Filter presses are valued for their efficiency, ability to handle high-pressure filtration, and versatility in processing different types of slurries.
Key Points Explained:
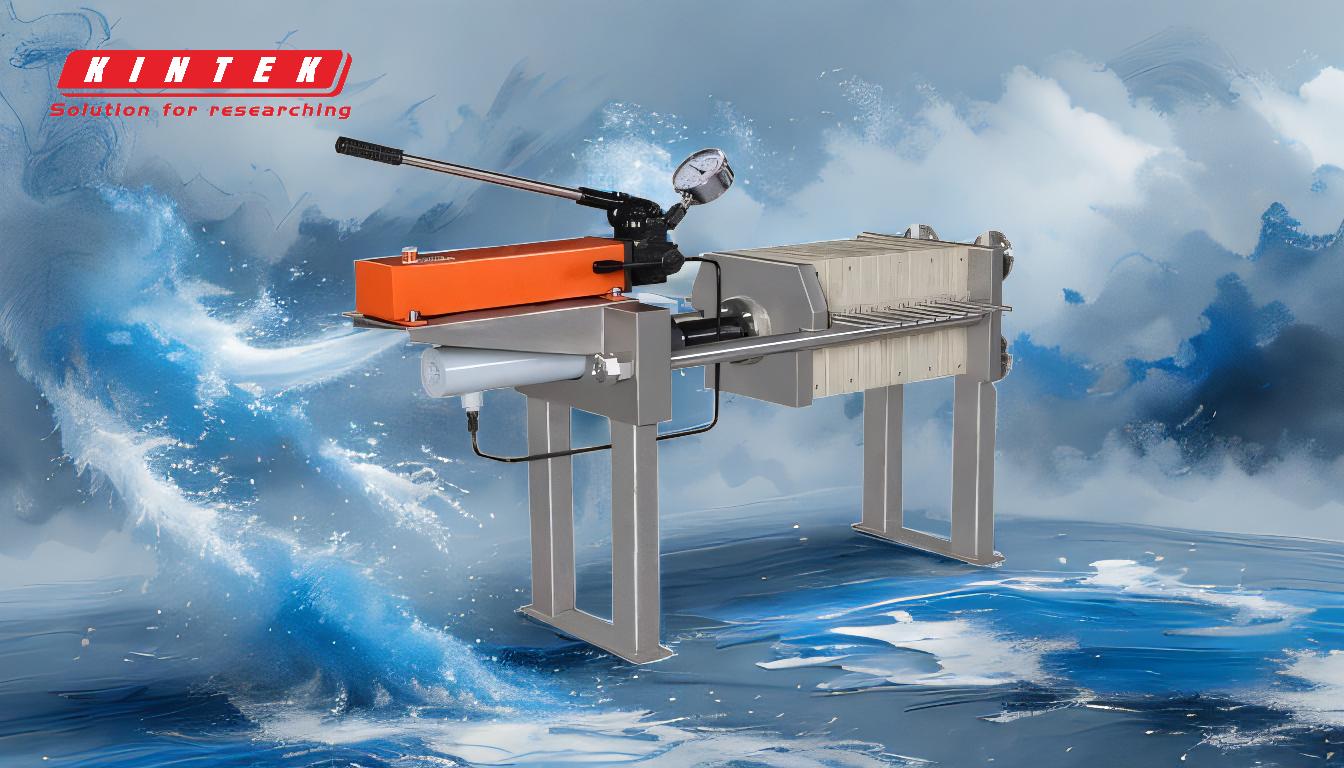
-
What is a Filter Press?
- A filter press is a mechanical device used to separate solids from liquids using pressure filtration. It consists of a series of filter plates lined with filter cloths, which trap solid particles while allowing the liquid to pass through.
- The process begins by pumping a slurry into the filter press. As pressure builds, the liquid is forced through the filter cloths, leaving behind a solid filter cake.
-
Components of a Filter Press
- Filter Plates: These are the core components that hold the filter cloths and create chambers for the slurry. Plates can be made of materials like polypropylene, stainless steel, or cast iron, depending on the application.
- Filter Cloths: These are the medium through which filtration occurs. They are selected based on the particle size and chemical compatibility with the slurry.
- Frame: The frame holds the plates and cloths in place and provides structural support.
- Hydraulic System: This system applies the necessary pressure to the plates to ensure efficient filtration.
- Feed Pump: Used to pump the slurry into the filter press.
-
How Does a Filter Press Work?
- The slurry is pumped into the filter press, filling the chambers between the plates.
- Pressure is applied, forcing the liquid (filtrate) through the filter cloths and out of the system.
- The solid particles accumulate on the cloths, forming a filter cake.
- Once the chambers are full, the filter press is opened, and the filter cake is removed for disposal or further processing.
-
Applications of Filter Presses
- Wastewater Treatment: Used to dewater sludge and recover water for reuse.
- Mining: Separates valuable minerals from slurry in mineral processing.
- Chemical Industry: Filters out impurities or recovers solid products from chemical solutions.
- Food and Beverage: Used in processes like juice clarification or starch extraction.
- Pharmaceuticals: Ensures the purity of liquid products by removing solid contaminants.
-
Advantages of Filter Presses
- High Efficiency: Capable of handling large volumes of slurry and producing dry filter cakes.
- Versatility: Can be customized with different plate materials, cloth types, and configurations to suit specific applications.
- Cost-Effective: Reduces waste disposal costs by producing drier filter cakes, which are easier and cheaper to handle.
- Scalability: Lab-scale filter presses allow for process optimization before scaling up to industrial systems.
-
Types of Filter Presses
- Recessed Plate Filter Press: Features recessed plates that create chambers for the slurry. Commonly used in wastewater treatment and mining.
- Membrane Filter Press: Includes flexible membranes that can be inflated to squeeze additional liquid from the filter cake, resulting in a drier product.
- Plate and Frame Filter Press: Consists of alternating plates and frames, offering flexibility for different filtration needs.
- Lab Filter Press: A smaller version designed for testing and research purposes, allowing for process optimization before full-scale implementation.
-
Considerations for Purchasing a Filter Press
- Application Requirements: Determine the type of slurry, particle size, and desired filtration outcomes.
- Material Compatibility: Ensure the plates and cloths are compatible with the chemicals and temperatures involved.
- Capacity and Throughput: Choose a filter press that meets the required processing volume.
- Automation Level: Decide between manual, semi-automatic, or fully automatic systems based on operational needs.
- Maintenance and Support: Consider ease of maintenance and availability of spare parts and technical support.
-
Maintenance and Operation
- Regular cleaning of filter cloths and plates is essential to maintain efficiency.
- Inspect the hydraulic system and feed pump for wear and tear.
- Replace worn-out filter cloths to prevent leaks and ensure consistent filtration performance.
In summary, filter presses are indispensable tools in industries requiring solid-liquid separation. Their efficiency, versatility, and scalability make them a preferred choice for applications ranging from wastewater treatment to mining. The lab filter press plays a crucial role in research and development, enabling the optimization of filtration processes before industrial implementation. When selecting a filter press, it is essential to consider factors such as application requirements, material compatibility, and maintenance needs to ensure optimal performance and longevity.
Summary Table:
Aspect | Details |
---|---|
Function | Separates solids from liquids using pressure filtration. |
Key Components | Filter plates, filter cloths, frame, hydraulic system, feed pump. |
Applications | Wastewater treatment, mining, chemical processing, food production. |
Advantages | High efficiency, versatility, cost-effectiveness, scalability. |
Types | Recessed plate, membrane, plate and frame, lab filter press. |
Maintenance | Regular cleaning, inspection of hydraulic system, and cloth replacement. |
Ready to optimize your filtration process? Contact us today to find the perfect filter press for your needs!