Free sintering is a specific type of sintering process where powdered materials are heated below their melting point to form a solid mass without the application of external pressure. Unlike pressure-assisted sintering methods, free sintering relies solely on heat to induce atomic diffusion and bonding between particles. This process is widely used in industries such as ceramics, powder metallurgy, and materials science to create dense, durable, and high-performance components. Free sintering is particularly advantageous for materials with high melting points and for producing complex shapes with minimal distortion.
Key Points Explained:
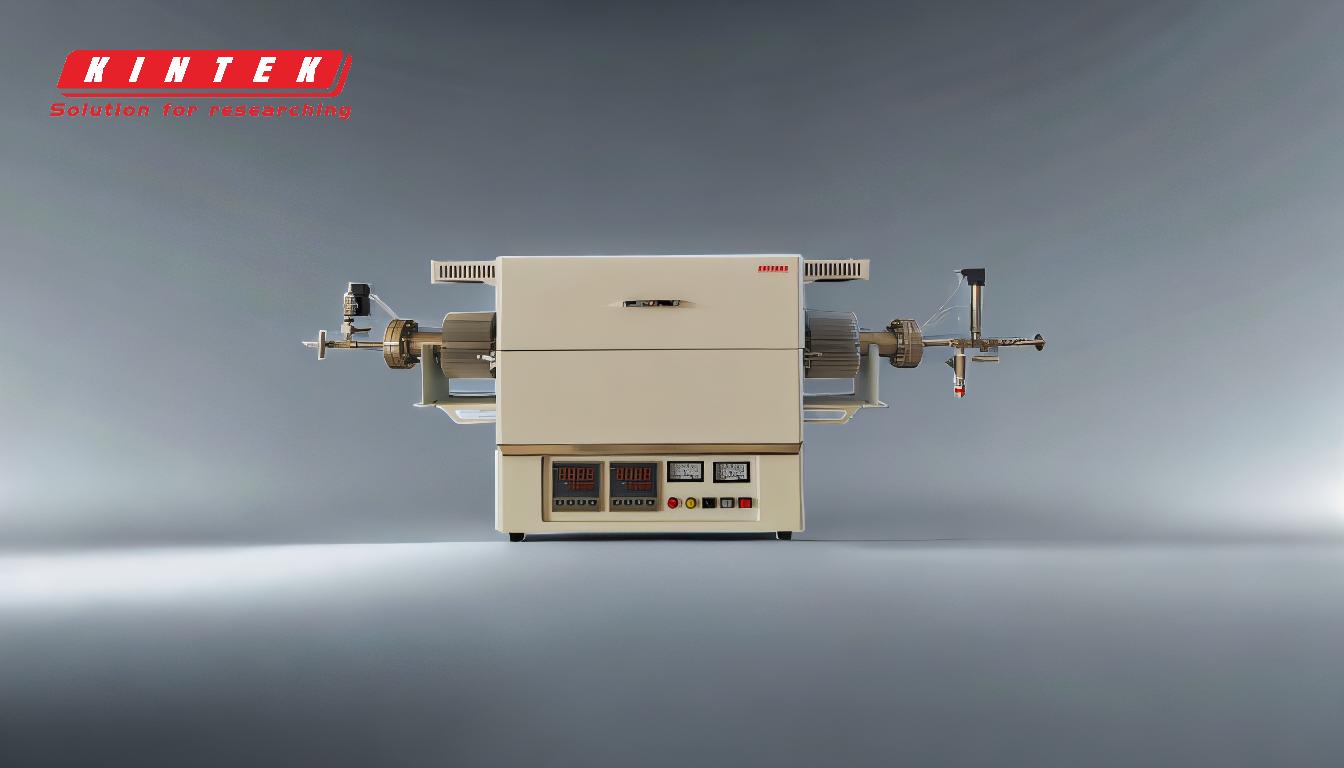
-
Definition of Free Sintering
- Free sintering is a heat treatment process where powdered materials are compacted into a solid mass by heating them below their melting point, without applying external pressure.
- It relies on natural solid-state diffusion, where atoms migrate across particle boundaries, fusing them together to form a dense, cohesive structure.
- This process is distinct from pressure-assisted sintering, which uses external force to enhance densification.
-
Mechanism of Free Sintering
- During free sintering, the material is heated in a controlled environment (e.g., a furnace) to a temperature just below its melting point.
- Heat energy activates atomic diffusion, allowing particles to bond at their contact points.
- Porosity within the material is reduced as particles rearrange and densify, improving mechanical and physical properties.
- The absence of external pressure means the process is slower but results in minimal deformation or stress in the final product.
-
Applications of Free Sintering
- Ceramics: Used to produce pottery, tiles, and advanced ceramic components like insulators and refractories.
- Powder Metallurgy: Commonly employed for manufacturing metal parts such as gears, bearings, and electrical contacts.
- High-Melting-Point Materials: Ideal for materials like tungsten, molybdenum, and ceramics that are difficult to melt and shape using traditional methods.
- Complex Shapes: Free sintering is suitable for creating intricate geometries with minimal distortion, as it does not rely on external pressure that could alter the shape.
-
Advantages of Free Sintering
- Cost-Effective: Eliminates the need for expensive pressure equipment, reducing production costs.
- Versatility: Applicable to a wide range of materials, including metals, ceramics, and composites.
- Minimal Distortion: Produces components with precise dimensions and minimal warping.
- Enhanced Properties: Improves mechanical strength, thermal conductivity, and electrical conductivity by reducing porosity and enhancing atomic bonding.
-
Limitations of Free Sintering
- Slower Process: Compared to pressure-assisted sintering, free sintering takes longer due to the reliance on heat alone.
- Material Constraints: Not all materials are suitable for free sintering; some may require additional pressure to achieve full densification.
- Porosity Control: Achieving uniform density and eliminating residual porosity can be challenging without external pressure.
-
Comparison with Other Sintering Methods
- Pressure-Assisted Sintering: Uses external pressure to accelerate densification, resulting in faster processing times but potentially higher costs and equipment complexity.
- Hot Isostatic Pressing (HIP): Combines heat and high-pressure gas to achieve near-theoretical density, ideal for critical applications but more expensive.
- Spark Plasma Sintering (SPS): Applies electrical current and pressure for rapid sintering, suitable for advanced materials but requiring specialized equipment.
-
Key Factors Influencing Free Sintering
- Temperature: Must be carefully controlled to avoid melting while ensuring sufficient atomic diffusion.
- Atmosphere: The sintering environment (e.g., inert gas, vacuum) prevents oxidation and contamination.
- Particle Size and Shape: Smaller, uniform particles sinter more effectively due to increased surface area and contact points.
- Heating Rate and Cooling Rate: Controlled heating and cooling prevent thermal stresses and ensure optimal material properties.
-
Industrial Relevance
- Free sintering is widely used in industries requiring high-performance materials, such as aerospace, automotive, electronics, and energy.
- It enables the production of components with tailored properties, such as enhanced strength, wear resistance, and thermal stability.
- The process is scalable, making it suitable for both small-scale prototyping and large-scale manufacturing.
By understanding the principles, applications, and advantages of free sintering, manufacturers can leverage this process to produce high-quality components efficiently and cost-effectively.
Summary Table:
Aspect | Details |
---|---|
Definition | Heating powdered materials below melting point without external pressure. |
Mechanism | Atomic diffusion bonds particles, reducing porosity and enhancing density. |
Applications | Ceramics, powder metallurgy, high-melting-point materials, complex shapes. |
Advantages | Cost-effective, versatile, minimal distortion, enhanced material properties. |
Limitations | Slower process, material constraints, porosity control challenges. |
Key Factors | Temperature, atmosphere, particle size, heating/cooling rates. |
Industrial Relevance | Aerospace, automotive, electronics, energy, and scalable manufacturing. |
Discover how free sintering can optimize your material processing—contact our experts today!