Furnace soldering is a specialized process that involves joining metal components using a filler metal (solder) in a controlled high-temperature environment provided by a furnace. This method is widely used in industries such as electronics, metallurgy, and ceramics, where precise temperature control and uniform heating are critical. The furnace ensures that the solder melts and flows evenly, creating strong, reliable bonds between the parts. This technique is particularly useful for applications requiring high-temperature resistance, such as in the production of electronic components, ceramic sintering, or metallurgical processes.
Key Points Explained:
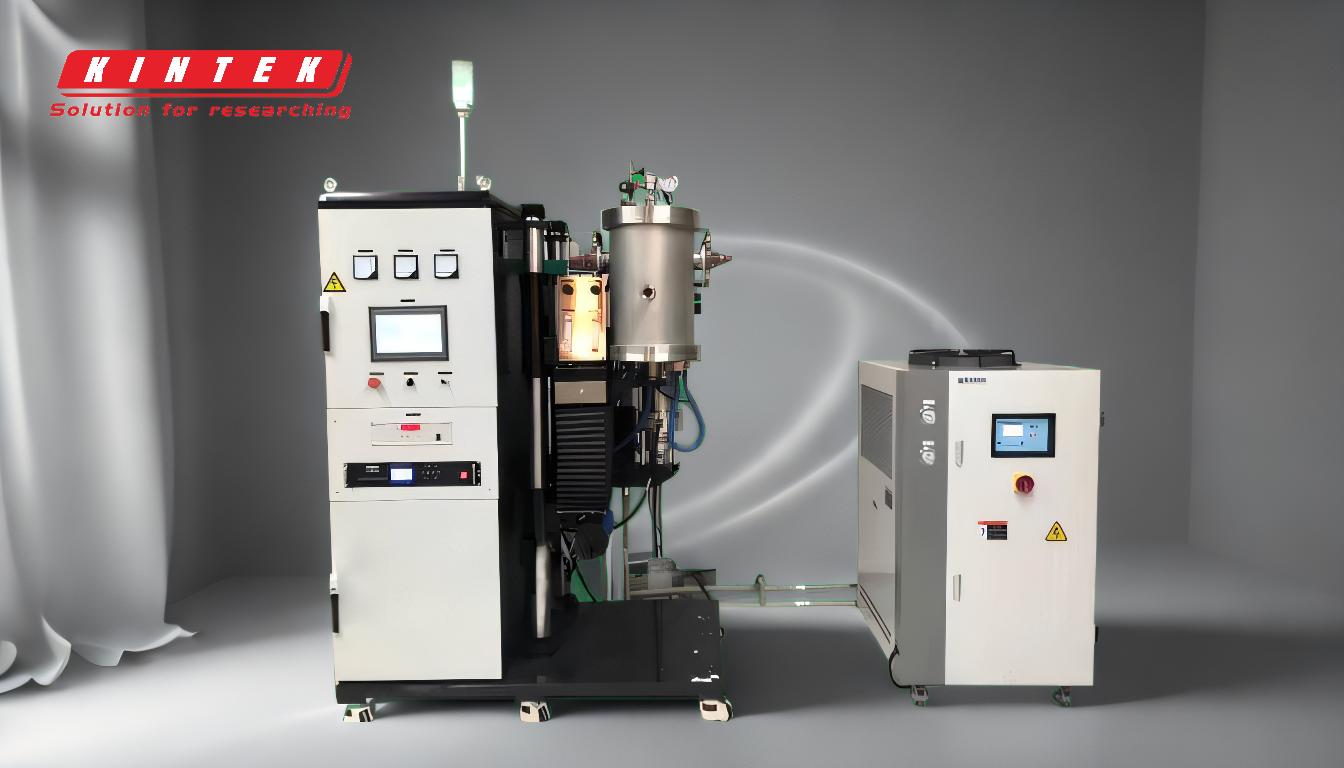
-
Definition and Process of Furnace Soldering:
- Furnace soldering is a joining process that uses a furnace to provide controlled heat, allowing a filler metal (solder) to melt and bond metal components.
- The process involves placing the parts to be joined, along with the solder, into the furnace. The furnace then heats the assembly to a specific temperature, ensuring the solder melts and flows evenly across the joint.
-
Applications of Furnace Soldering:
- Furnace soldering is widely used in industries such as:
- Electronics: For creating reliable connections in circuit boards and electronic components.
- Metallurgy: For joining metal parts in high-temperature environments.
- Ceramics: For sintering and bonding ceramic materials.
- Glass and Chemical Industries: For processes requiring precise temperature control and uniform heating.
- Furnace soldering is widely used in industries such as:
-
Advantages of Furnace Soldering:
- Uniform Heating: The furnace provides consistent and even heat distribution, ensuring strong and reliable bonds.
- High-Temperature Capability: Suitable for applications requiring high-temperature resistance, such as in metallurgical and ceramic processes.
- Controlled Atmosphere: Some furnaces allow for controlled atmospheres (e.g., inert gases) to prevent oxidation and improve solder flow.
-
Materials and Equipment:
- Furnace Types: Different types of furnaces, such as muffle furnaces, are used depending on the application and required temperature range.
- Solder Materials: The choice of solder depends on the materials being joined and the operating temperature. Common solder materials include tin-lead alloys, silver-based alloys, and other high-temperature solders.
-
Process Considerations:
- Temperature Control: Precise temperature control is essential to ensure the solder melts and flows correctly without damaging the components.
- Joint Preparation: Proper cleaning and preparation of the joint surfaces are critical to achieving a strong bond.
- Cooling Rate: Controlled cooling is often necessary to prevent thermal stress and ensure the integrity of the joint.
-
Comparison with Other Soldering Methods:
- Furnace Soldering vs. Hand Soldering: Furnace soldering offers better consistency and uniformity compared to hand soldering, which relies on manual heat application.
- Furnace Soldering vs. Wave Soldering: While wave soldering is used for mass production of electronic components, furnace soldering is more suitable for specialized applications requiring high precision and controlled atmospheres.
-
Challenges and Solutions:
- Oxidation: Oxidation can occur during the soldering process, leading to weak joints. Using a controlled atmosphere furnace or flux can mitigate this issue.
- Thermal Stress: Rapid heating or cooling can cause thermal stress. Gradual temperature changes and proper cooling techniques can help prevent this.
By understanding these key points, equipment and consumable purchasers can make informed decisions about the suitability of furnace soldering for their specific applications and choose the right materials and equipment to achieve optimal results.
Summary Table:
Aspect | Details |
---|---|
Definition | A process using a furnace to melt solder and bond metal components. |
Applications | Electronics, metallurgy, ceramics, glass, and chemical industries. |
Advantages | Uniform heating, high-temperature capability, controlled atmosphere. |
Materials | Solder types: tin-lead, silver-based, high-temperature alloys. |
Equipment | Furnace types: muffle furnaces, controlled atmosphere furnaces. |
Process Considerations | Temperature control, joint preparation, cooling rate. |
Challenges | Oxidation, thermal stress. |
Discover how furnace soldering can enhance your industrial processes—contact us today for expert advice!