Heat treatment furnaces are specialized heating chambers designed to hold and heat steel stock to impart specific properties such as hardness, strength, or ductility. These furnaces are classified based on their structure, heat source, and the type of heat treatment they perform. They range from low-temperature furnaces for tempering to high-temperature furnaces for processes like hardening and carburizing. Modern advancements include vacuum resistance furnaces, which use inert gases like argon to create controlled environments for precise heat treatment. These furnaces are critical in industries like aerospace, where components require highly reproducible and uniform properties.
Key Points Explained:
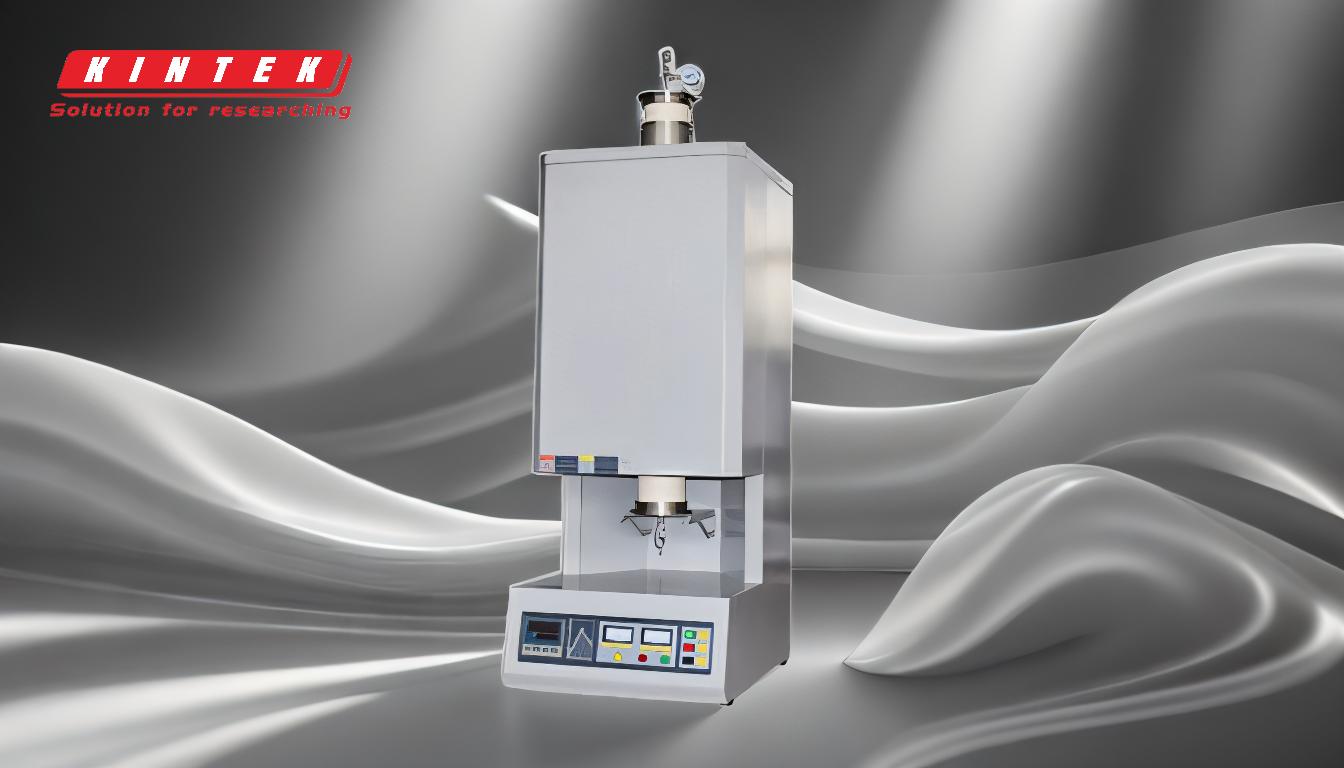
-
Definition and Purpose of Heat Treatment Furnaces:
- Heat treatment furnaces are heating chambers designed to hold steel or other materials and heat them to specific temperatures to alter their physical and mechanical properties.
- They are essential for processes like hardening, tempering, annealing, and carburizing, which improve material properties such as strength, durability, and wear resistance.
-
Classification Based on Structure:
- Heat treatment furnaces can be categorized by their physical structure:
- Vertical vs. Horizontal: Vertical furnaces are space-efficient, while horizontal furnaces are better for larger or longer components.
- Single Chamber vs. Multi-Chamber: Single-chamber furnaces are simpler, while multi-chamber furnaces (e.g., three-chamber types) allow for sequential processing steps.
- Vacuum Furnaces: These are modern, endothermic types where the entire shell acts as a vacuum container, ensuring a controlled environment.
- Heat treatment furnaces can be categorized by their physical structure:
-
Classification Based on Heat Source:
- Heat treatment furnaces use various heat sources, including:
- Solid Fuels: Coal, pulverized coal, and coke.
- Liquid Fuels: Gasoline and kerosene.
- Gaseous Fuels: Coal gas and producer gas.
- The choice of fuel depends on factors like availability, cost, and technical suitability for the specific treatment process.
- Heat treatment furnaces use various heat sources, including:
-
Classification Based on Temperature Range:
- Heat treatment furnaces are designed for specific temperature ranges depending on the process:
- Low-Temperature Furnaces (0–700°C): Used for tempering and sub-critical annealing, often with forced air circulation or liquid baths (oil, lead, or salt).
- General-Purpose Furnaces (700–1050°C): Suitable for hardening, normalizing, and carburizing of carbon and low alloy steels.
- High-Temperature Furnaces (1000–1400°C): Used for heat treatment of high-speed steels and other high-temperature cycles.
- Heat treatment furnaces are designed for specific temperature ranges depending on the process:
-
Types of Heat Treatment Furnaces:
- Roller Hearth Furnaces: Ideal for continuous processing of large volumes of material.
- Pusher Furnaces: Used for batch processing, where materials are pushed through the furnace.
- Box Furnaces: Versatile and suitable for small to medium-sized batches.
- Pot/Pit Furnaces: Designed for specific treatments like salt bath heat treatment.
- Conveyor Belt Furnaces: Used for continuous, high-volume processing.
- Integral-Quench Furnaces: Combine heating and quenching in a single unit for efficiency.
-
Specialized Furnaces for Aerospace Applications:
- Aerospace heat treatment requires highly precise and controlled processes. Furnaces used in this industry include:
- Fabricated Muffles and Retorts: For controlled atmosphere heat treatment.
- Vacuum Retorts and Lids: To create oxygen-free environments.
- Heat Treating Salt Pots: For specific treatments requiring molten salts.
- Pit Furnace Retorts and Liners: For large or heavy components.
- Atmosphere Furnace Fan Systems: To ensure uniform temperature distribution.
- Furnace Rolls and Internal Alloy Systems: For high-temperature resistance and durability.
- Aerospace heat treatment requires highly precise and controlled processes. Furnaces used in this industry include:
-
Vacuum Heat Treatment Furnaces:
- These furnaces use a vacuum chamber to remove oxygen and replace it with inert gases like argon.
- The process involves heating the chamber to temperatures up to 2400°F (1315°C) at a controlled rate, followed by cooling.
- The "soak" time (duration at peak temperature) is determined by the material and desired properties.
- Computer-controlled systems ensure uniformity and repeatability, making vacuum furnaces ideal for high-precision applications.
-
Applications and Industry Relevance:
- Heat treatment furnaces are indispensable in industries like aerospace, automotive, and manufacturing, where material properties must meet stringent standards.
- They enable the production of components with enhanced mechanical properties, ensuring reliability and performance in demanding applications.
By understanding these key points, purchasers can make informed decisions when selecting heat treatment furnaces, ensuring they meet the specific needs of their applications.
Summary Table:
Category | Details |
---|---|
Structure | Vertical, Horizontal, Single Chamber, Multi-Chamber, Vacuum Furnaces |
Heat Source | Solid Fuels (coal, coke), Liquid Fuels (gasoline, kerosene), Gaseous Fuels |
Temperature Range | Low-Temperature (0–700°C), General-Purpose (700–1050°C), High-Temperature (1000–1400°C) |
Types | Roller Hearth, Pusher, Box, Pot/Pit, Conveyor Belt, Integral-Quench Furnaces |
Specialized Applications | Aerospace (Fabricated Muffles, Vacuum Retorts, Salt Pots, Pit Furnace Retorts) |
Advantages | Precise temperature control, uniform heating, enhanced material properties |
Ready to find the perfect heat treatment furnace for your needs? Contact our experts today!