High-frequency induction heaters are advanced devices that utilize electromagnetic induction to generate heat in conductive materials, such as metals and semiconductors, without direct contact. They operate by creating a high-frequency alternating magnetic field, which induces eddy currents within the material, causing it to heat up due to electrical resistance. This technology is widely used in industrial processes like brazing, forging, quenching, and melting, as well as in specialized applications such as semiconductor manufacturing, medical treatments, and domestic induction cooktops. High-frequency induction heaters are valued for their efficiency, precision, and versatility, making them a cornerstone in modern manufacturing and material processing.
Key Points Explained:
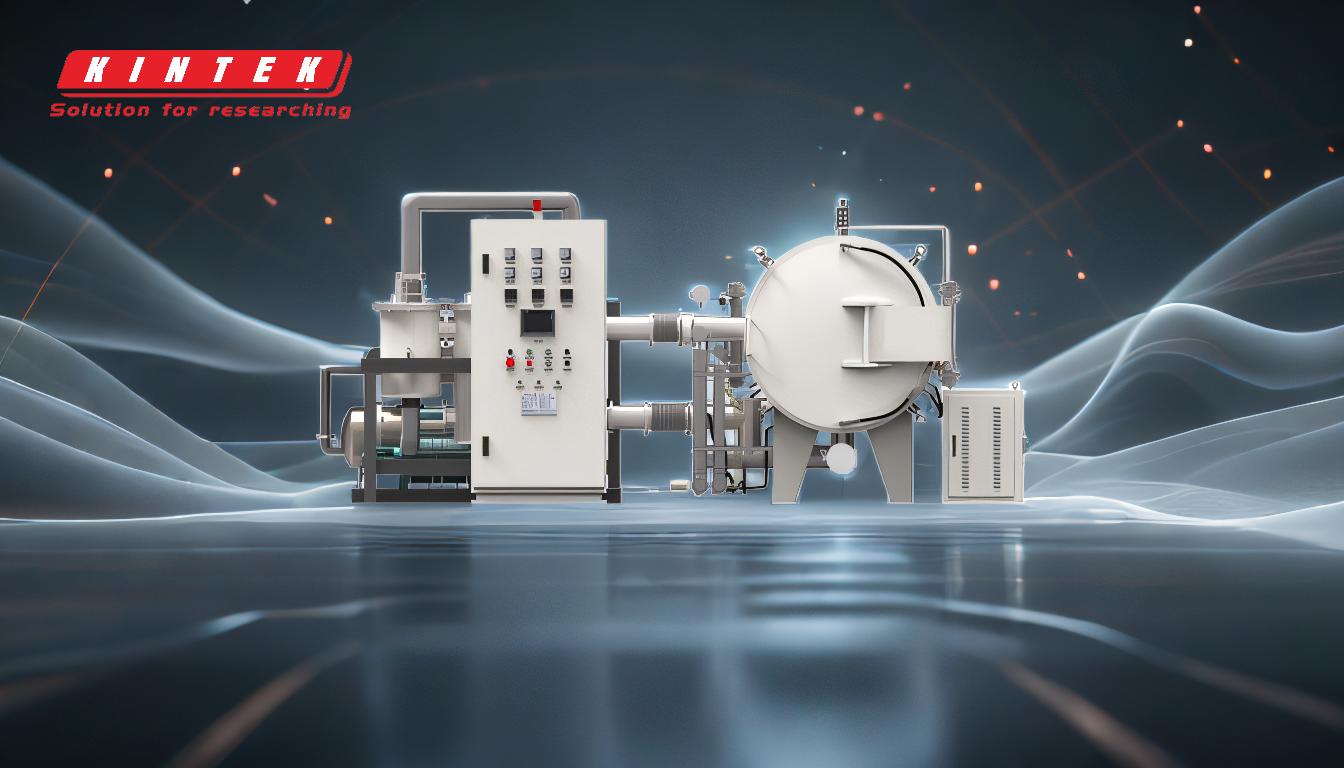
-
Definition and Working Principle:
- High-frequency induction heaters use electromagnetic induction to generate heat in conductive materials.
- An alternating magnetic field is created by passing high-frequency alternating current through a coil.
- This magnetic field induces eddy currents within the conductive material, causing it to heat up due to its electrical resistance.
-
Applications in Industry:
- Brazing and Soldering: Used for joining metals with precision and minimal heat distortion.
- Hot Forging: Ideal for heating small workpieces, such as round bars below 15mm, for shaping.
- Quenching: Provides localized heating for surface hardening with a layer depth of 1~2mm.
- Melting and Alloying: Used in induction furnaces to melt metals and create specialized alloys.
- Semiconductor Manufacturing: Applied in processes like Czochralski crystal growth and zone refining.
-
Advantages Over Traditional Heating Methods:
- Efficiency: Induction heating is highly energy-efficient as it directly heats the material without intermediate steps.
- Precision: Offers precise temperature control, essential for processes like heat treatment and brazing.
- Speed: Rapid heating reduces processing time, improving productivity.
- Cleanliness: No combustion or direct contact, minimizing contamination and oxidation.
-
Specialized Applications:
- Medical Uses: Heating biological tissues for therapeutic purposes.
- Plastic Molding: Enhances energy efficiency in injection molding machines.
- Tamper-Resistant Sealing: Used in pharmaceutical and beverage industries for secure bottle cap sealing.
- Domestic Induction Cooktops: Provides fast and efficient cooking with precise temperature control.
-
Future Trends and Research:
- Technological Advancements: Ongoing research aims to optimize process parameters for emerging applications.
- Expanding Applications: Potential uses in alternative energy systems and highly engineered materials.
- Global Impact: Induction heating is expected to empower developing countries by providing efficient and cost-effective heating solutions.
-
Key Components and Design:
- Coil Design: The induction coil is crucial for generating the magnetic field and must be tailored to the specific application.
- Power Supply: High-frequency power supplies are required to generate the alternating current.
- Cooling Systems: Efficient cooling is necessary to maintain the performance and longevity of the equipment.
-
Challenges and Considerations:
- Material Compatibility: Not all materials are suitable for induction heating; conductivity and magnetic properties are critical factors.
- Cost: Initial setup costs can be high, though operational savings often offset this over time.
- Process Optimization: Achieving consistent results requires careful control of parameters like frequency, power, and heating time.
In summary, high-frequency induction heaters are versatile and efficient tools that have revolutionized heating processes across various industries. Their ability to provide precise, rapid, and clean heating makes them indispensable in modern manufacturing, medical applications, and everyday domestic use. As technology advances, their applications are expected to grow, further solidifying their role in shaping the future of material processing and energy utilization.
Summary Table:
Aspect | Details |
---|---|
Working Principle | Uses electromagnetic induction to generate heat in conductive materials. |
Key Applications | Brazing, forging, quenching, melting, semiconductor manufacturing, medical uses. |
Advantages | High efficiency, precision, speed, and cleanliness. |
Specialized Uses | Plastic molding, tamper-resistant sealing, domestic induction cooktops. |
Future Trends | Expanding applications in alternative energy and engineered materials. |
Challenges | Material compatibility, initial cost, and process optimization. |
Ready to explore the benefits of high-frequency induction heaters? Contact us today for expert guidance!