HIP (Hot Isostatic Pressing) and CIP (Cold Isostatic Pressing) are two critical processes in powder metallurgy used to consolidate metal powders into dense, high-quality components. HIP involves applying high temperature and pressure to metal powders, resulting in a homogeneous, annealed microstructure with minimal impurities. CIP, on the other hand, uses room temperature and high pressure to compact powders into a "green" state, which can then be sintered or further processed. Both methods are essential for producing components with superior mechanical properties and dimensional accuracy.
Key Points Explained:
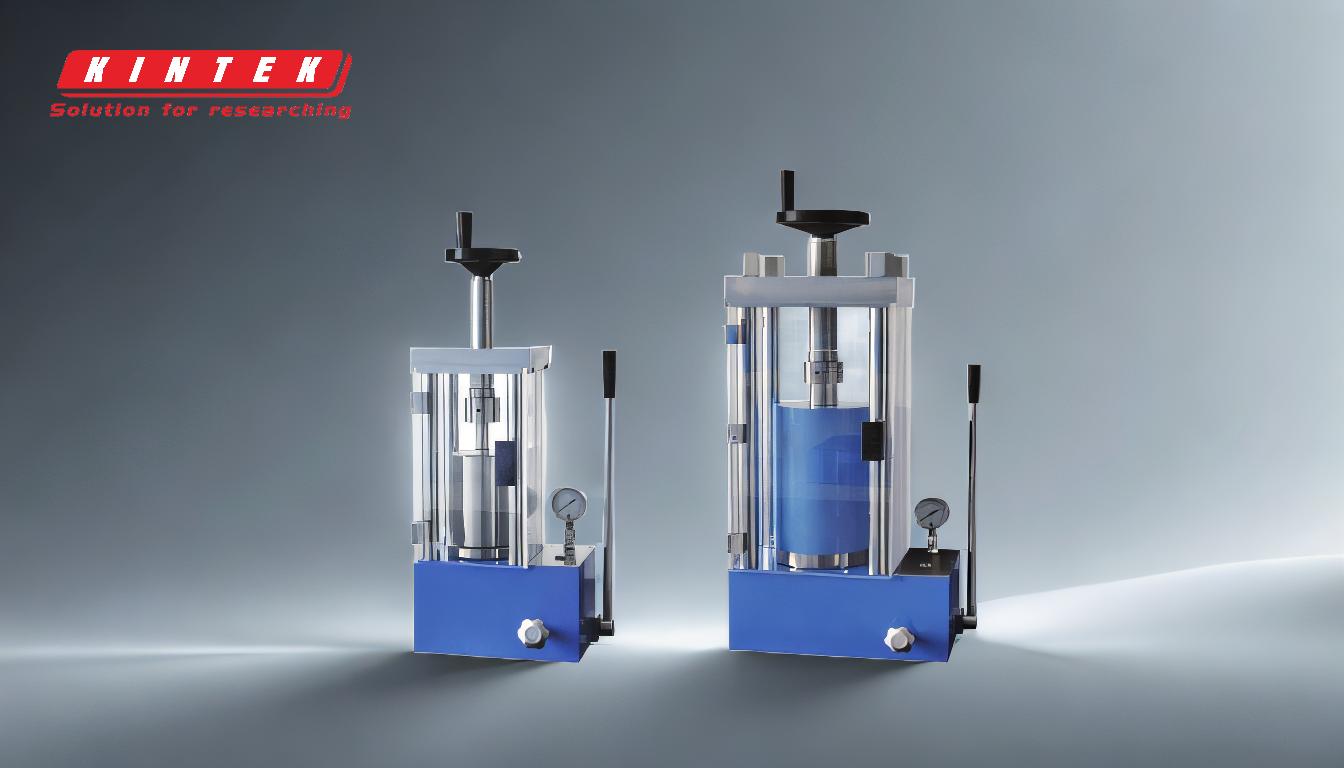
-
What is HIP (Hot Isostatic Pressing)?
- HIP is a process that combines high temperature and high pressure to consolidate metal powders into a dense, solid component.
- The process typically involves temperatures ranging from 900°C to 1200°C and pressures between 100 MPa and 200 MPa.
- The high temperature and pressure facilitate deformation, creep, and diffusion, leading to a homogeneous microstructure with minimal porosity and impurities.
- HIP is particularly useful for materials that are difficult to process using traditional methods, such as superalloys, titanium, and ceramics.
- The resulting components have excellent mechanical properties, including high strength, toughness, and fatigue resistance.
-
What is CIP (Cold Isostatic Pressing)?
- CIP is a process that uses high pressure at room temperature to compact metal powders into a "green" state.
- The pressure is applied uniformly from all directions, typically using a liquid medium such as water or oil, ensuring even compaction.
- CIP is often used as a preliminary step before sintering or other heat treatment processes.
- The "green" compacts produced by CIP have sufficient strength to be handled and machined but require further processing to achieve full density and mechanical properties.
- CIP is suitable for a wide range of materials, including metals, ceramics, and composites.
-
Key Differences Between HIP and CIP:
- Temperature: HIP operates at high temperatures (900°C to 1200°C), while CIP is conducted at room temperature.
- Pressure: Both processes use high pressure, but HIP typically involves higher pressures (100 MPa to 200 MPa) compared to CIP.
- Microstructure: HIP produces a fully dense, homogeneous microstructure with minimal porosity, while CIP produces a "green" compact that requires further processing.
- Applications: HIP is used for high-performance components in aerospace, medical, and energy industries, while CIP is often used for simpler shapes and less demanding applications.
-
Advantages of HIP:
- Produces components with near-net shape, reducing the need for extensive machining.
- Eliminates internal defects such as voids and porosity, improving mechanical properties.
- Suitable for a wide range of materials, including those that are difficult to process using conventional methods.
- Enhances material properties such as strength, toughness, and fatigue resistance.
-
Advantages of CIP:
- Uniform compaction from all directions ensures even density and minimal distortion.
- Suitable for complex shapes and large components.
- Lower cost compared to HIP, as it does not require high temperatures.
- Can be used for a wide range of materials, including metals, ceramics, and composites.
-
Applications of HIP and CIP:
- HIP Applications: Aerospace components (turbine blades, engine parts), medical implants (hip and knee replacements), and high-performance industrial parts (valves, seals).
- CIP Applications: Ceramic components (insulators, cutting tools), metal parts (gears, bearings), and composite materials.
-
Considerations for Equipment Purchasers:
- HIP Equipment: Look for systems that offer precise temperature and pressure control, uniform heating, and efficient cooling. Consider the size and capacity of the chamber, as well as the ability to handle different materials.
- CIP Equipment: Focus on systems with uniform pressure distribution, easy loading and unloading, and compatibility with various powder types. Consider the size of the chamber and the pressure range.
By understanding the differences and advantages of HIP and CIP, equipment and consumable purchasers can make informed decisions about which process is best suited for their specific needs. Both methods play a crucial role in powder metallurgy, offering unique benefits for producing high-quality components.
Summary Table:
Aspect | HIP (Hot Isostatic Pressing) | CIP (Cold Isostatic Pressing) |
---|---|---|
Temperature | High (900°C to 1200°C) | Room Temperature |
Pressure | High (100 MPa to 200 MPa) | High (Uniform Pressure) |
Microstructure | Fully dense, homogeneous, minimal porosity | 'Green' compact, requires further processing |
Applications | Aerospace, medical implants, high-performance industrial parts | Ceramic components, metal parts, composite materials |
Advantages | Near-net shape, eliminates defects, enhances strength, toughness, and fatigue resistance | Uniform compaction, cost-effective, suitable for complex shapes and large components |
Ready to choose the right process for your needs? Contact our experts today to learn more about HIP and CIP solutions!