Hot forging is a manufacturing process where metal is heated to a high temperature and then shaped using compressive forces. This technique is widely used across various industries due to its ability to produce strong, durable, and high-quality metal components. The process is particularly beneficial for creating parts that require high strength, precision, and resistance to wear and tear. Hot forging is commonly used in the automotive, aerospace, construction, and heavy machinery industries, among others. It is ideal for producing complex shapes and large components that would be difficult or impossible to achieve through other manufacturing methods.
Key Points Explained:
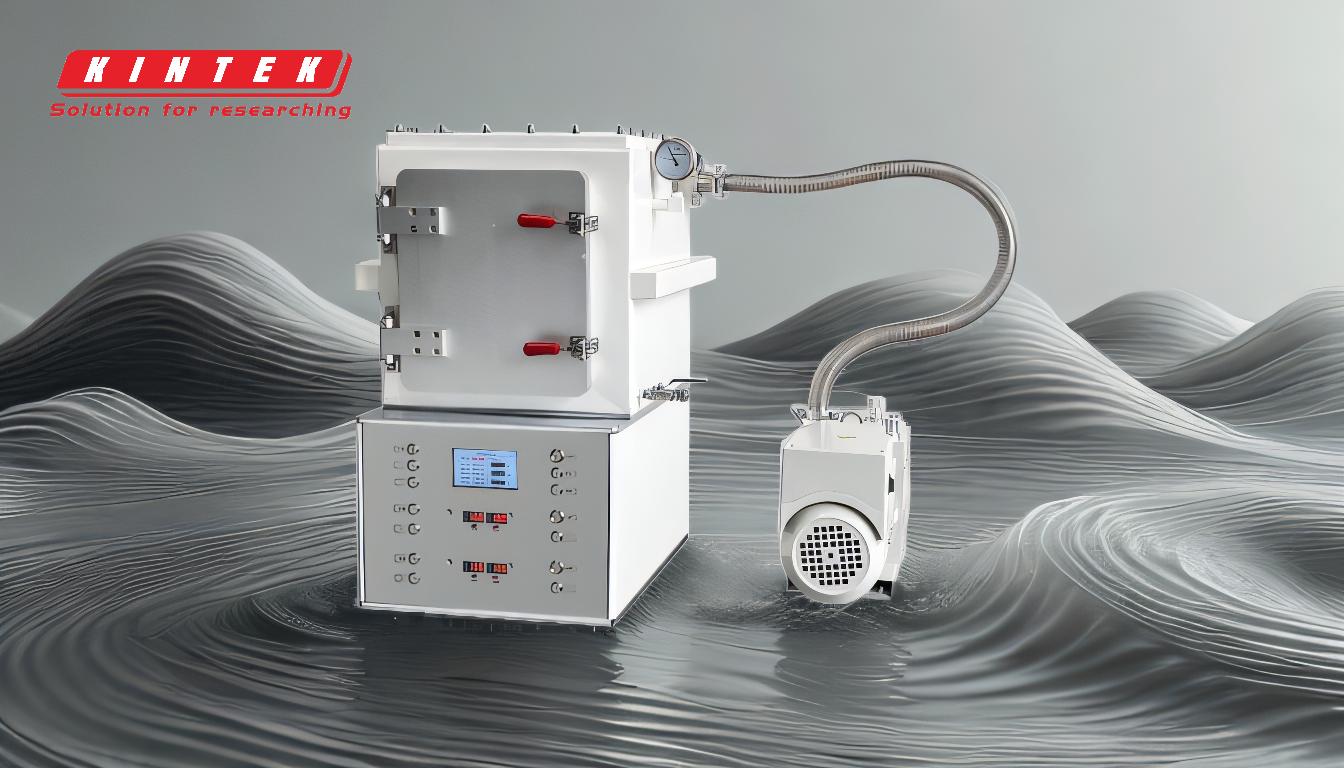
-
Definition and Process of Hot Forging:
- Hot forging involves heating metal to a temperature above its recrystallization point, typically between 950°C and 1250°C, depending on the material.
- Once heated, the metal is placed in a die and subjected to compressive forces, either through hammering or pressing, to shape it into the desired form.
- The high temperature makes the metal more malleable, allowing it to be shaped with less force and reducing the risk of cracking or other defects.
-
Advantages of Hot Forging:
- Improved Mechanical Properties: Hot forging enhances the grain structure of the metal, resulting in improved strength, toughness, and fatigue resistance.
- Complex Shapes: The process allows for the creation of complex and intricate shapes that would be challenging to achieve with cold forging or machining.
- Material Efficiency: Hot forging minimizes material waste, as excess metal can often be recycled or reused.
- Cost-Effective for Large Parts: For large components, hot forging is often more cost-effective than other methods, as it reduces the need for extensive machining.
-
Common Applications of Hot Forging:
- Automotive Industry: Hot forging is used to produce critical components such as crankshafts, connecting rods, gears, and axle beams. These parts require high strength and durability to withstand the stresses of vehicle operation.
- Aerospace Industry: The aerospace sector relies on hot forging for manufacturing high-strength components like turbine blades, landing gear parts, and structural elements. The process ensures that these parts can endure extreme conditions and stresses.
- Construction and Heavy Machinery: Hot forging is used to create large, durable parts such as bolts, nuts, and structural components for buildings, bridges, and heavy equipment.
- Oil and Gas Industry: Components like valves, flanges, and fittings used in the oil and gas industry are often produced through hot forging due to their need for high strength and resistance to corrosion.
-
Materials Suitable for Hot Forging:
- Steel and Alloy Steels: These are the most commonly forged materials due to their strength and versatility. Hot forging improves their mechanical properties, making them suitable for high-stress applications.
- Aluminum Alloys: Although aluminum has a lower forging temperature compared to steel, hot forging is still used to produce lightweight, high-strength components.
- Titanium Alloys: Known for their high strength-to-weight ratio and corrosion resistance, titanium alloys are often hot forged for aerospace and medical applications.
- Copper and Brass: These materials are hot forged to produce components that require good electrical conductivity and corrosion resistance.
-
Comparison with Cold Forging:
- Temperature: Cold forging is performed at or near room temperature, while hot forging requires heating the metal to high temperatures.
- Material Properties: Hot forging improves the ductility and workability of the metal, making it easier to shape complex parts. Cold forging, on the other hand, can increase the strength and hardness of the metal through strain hardening.
- Surface Finish: Cold forging typically results in a better surface finish and tighter tolerances, while hot forging may require additional finishing processes.
- Cost and Complexity: Hot forging is generally more cost-effective for large and complex parts, whereas cold forging is more suitable for smaller, simpler components.
-
Future Trends in Hot Forging:
- Automation and Robotics: The integration of automation and robotics in hot forging processes is increasing efficiency, reducing labor costs, and improving consistency in part quality.
- Advanced Materials: The development of new alloys and materials with enhanced properties is expanding the applications of hot forging in industries like aerospace and renewable energy.
- Sustainability: Efforts are being made to reduce the environmental impact of hot forging by improving energy efficiency, recycling materials, and minimizing waste.
Hot forging remains a vital process in modern manufacturing, offering a combination of strength, precision, and versatility that is unmatched by other methods. Its applications across various industries highlight its importance in producing high-performance components that meet the demanding requirements of today's technology and infrastructure.
Summary Table:
Aspect | Details |
---|---|
Definition | Heating metal above its recrystallization point and shaping with compressive forces. |
Temperature Range | 950°C to 1250°C, depending on the material. |
Advantages | Improved strength, complex shapes, material efficiency, cost-effectiveness. |
Applications | Automotive (crankshafts, gears), aerospace (turbine blades), construction (bolts, nuts). |
Materials | Steel, aluminum alloys, titanium alloys, copper, and brass. |
Comparison with Cold Forging | Hot forging is better for large, complex parts; cold forging suits smaller, simpler components. |
Future Trends | Automation, advanced materials, and sustainability improvements. |
Interested in hot forging for your industry? Contact us today to learn more!