Hot Isostatic Pressing (HIP) is a critical process in additive manufacturing and other metal manufacturing methods, designed to enhance the density, mechanical properties, and overall reliability of components. By applying uniform pressure and elevated temperatures, HIP eliminates internal voids and defects, resulting in parts with superior strength, fatigue resistance, and durability. This process is particularly beneficial for reducing porosity in castings and metal powders, improving material properties, and enabling the production of lighter, more efficient components. HIP also reduces scrap, minimizes quality assurance requirements, and can lower total production costs, making it a valuable tool in modern manufacturing.
Key Points Explained:
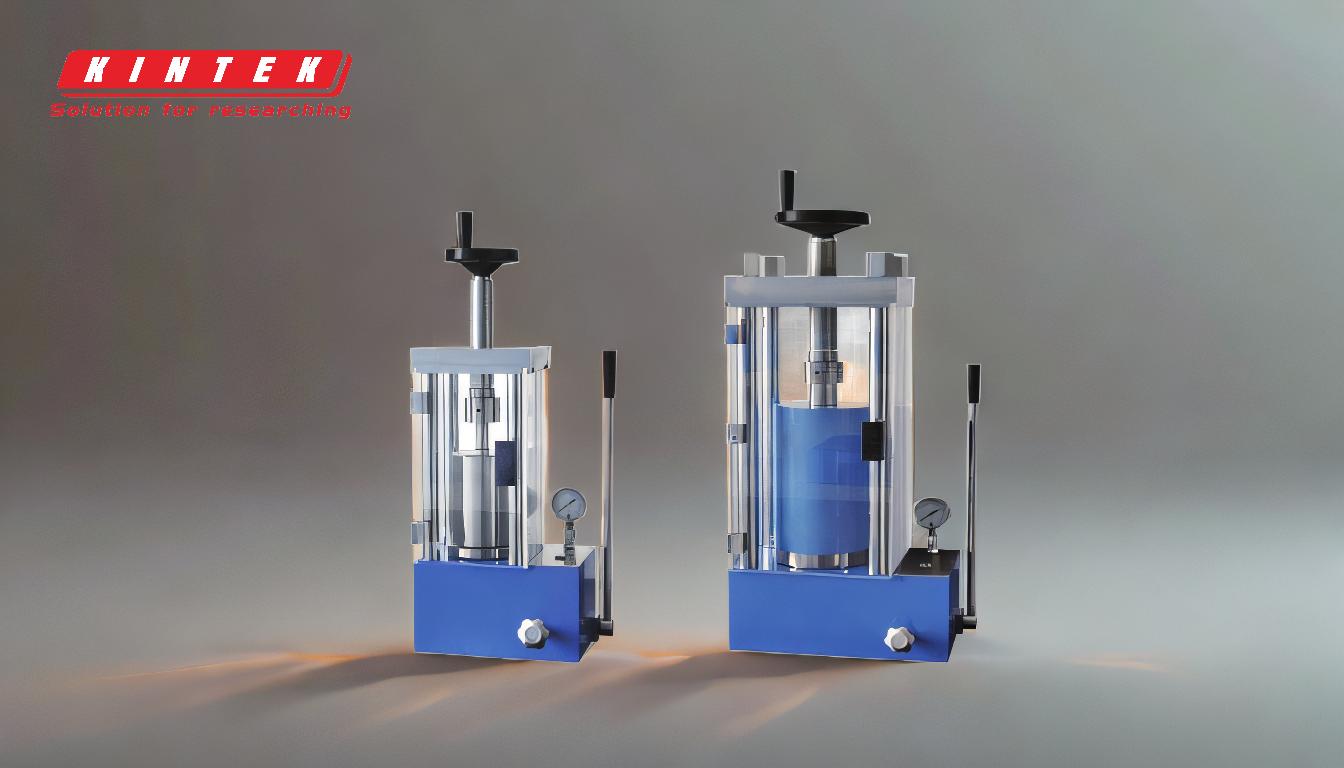
-
Definition and Process of Hot Isostatic Pressing (HIP):
- HIP is a manufacturing process where uniform pressure is applied to a hermetically sealed container filled with compacted metal powder or cast components. This pressure is typically delivered using gas or liquid and is combined with elevated temperatures to achieve densification.
- The process can be used to manufacture metal components directly or to densify parts produced through other methods like casting or powder metallurgy.
-
Applications in Additive Manufacturing:
- In additive manufacturing, HIP is used to improve the mechanical properties and workability of materials. It helps eliminate internal porosity and defects, which are common in 3D-printed parts.
- By densifying the material, HIP enhances the part's resistance to fractures, fatigue, and traction, making it suitable for demanding applications.
-
Key Benefits of HIP:
- Improved Material Properties: HIP increases product density, enhances mechanical properties (such as tensile strength and fatigue resistance), and reduces property scatter.
- Reduction of Defects: The process repairs internal porosity and microshrinkage in castings, resulting in parts with fewer defects.
- Cost Efficiency: HIP reduces scrap and losses, minimizes the need for radiographic inspections, and can lower total production costs.
- Lightweight and Durable Designs: HIP enables the production of lighter, near-net-shaped parts with superior performance and longer service life.
-
Advantages Over Traditional Manufacturing Methods:
- HIP allows for the replacement of wrought components with castings, reducing the need for extensive machining and material waste.
- It creates homogeneous microstructures, maximizing abrasion and corrosion resistance while improving fatigue resistance.
-
Integration with Other Manufacturing Processes:
- HIP is compatible with various metal manufacturing methods, including casting, forging, powder metallurgy, and additive manufacturing. This versatility makes it a valuable tool for producing high-quality, durable components across industries.
-
Economic and Operational Benefits:
- The savings from reduced quality assurance requirements and lower scrap rates often offset the costs of implementing HIP.
- By optimizing material properties and minimizing subsequent heat treatment requirements, HIP enhances part reliability and extends service life.
In summary, Hot Isostatic Pressing is a transformative process in additive manufacturing and metalworking, offering significant improvements in material properties, part reliability, and production efficiency. Its ability to eliminate defects, reduce costs, and produce high-performance components makes it an essential technology for modern manufacturing.
Summary Table:
Key Benefits of HIP | Details |
---|---|
Improved Material Properties | Increases density, enhances tensile strength, and reduces property scatter. |
Reduction of Defects | Repairs internal porosity and microshrinkage in castings. |
Cost Efficiency | Reduces scrap, minimizes inspections, and lowers production costs. |
Lightweight & Durable Designs | Produces near-net-shaped parts with superior performance and longer life. |
Discover how Hot Isostatic Pressing can transform your manufacturing process—contact us today!