Hydraulic press forging is a manufacturing process that uses a hydraulic press to shape metal into desired forms by applying controlled pressure. This method is particularly effective for creating high-strength, durable components with precise dimensions. Unlike traditional forging techniques that rely on mechanical force, hydraulic press forging uses fluid pressure to generate the necessary force, allowing for more uniform and controlled deformation of the metal. This process is widely used in industries such as automotive, aerospace, and heavy machinery, where the integrity and precision of metal components are critical. The use of a hydraulic hot press machine is common in this process, especially when working with materials that require high temperatures to achieve optimal malleability.
Key Points Explained:
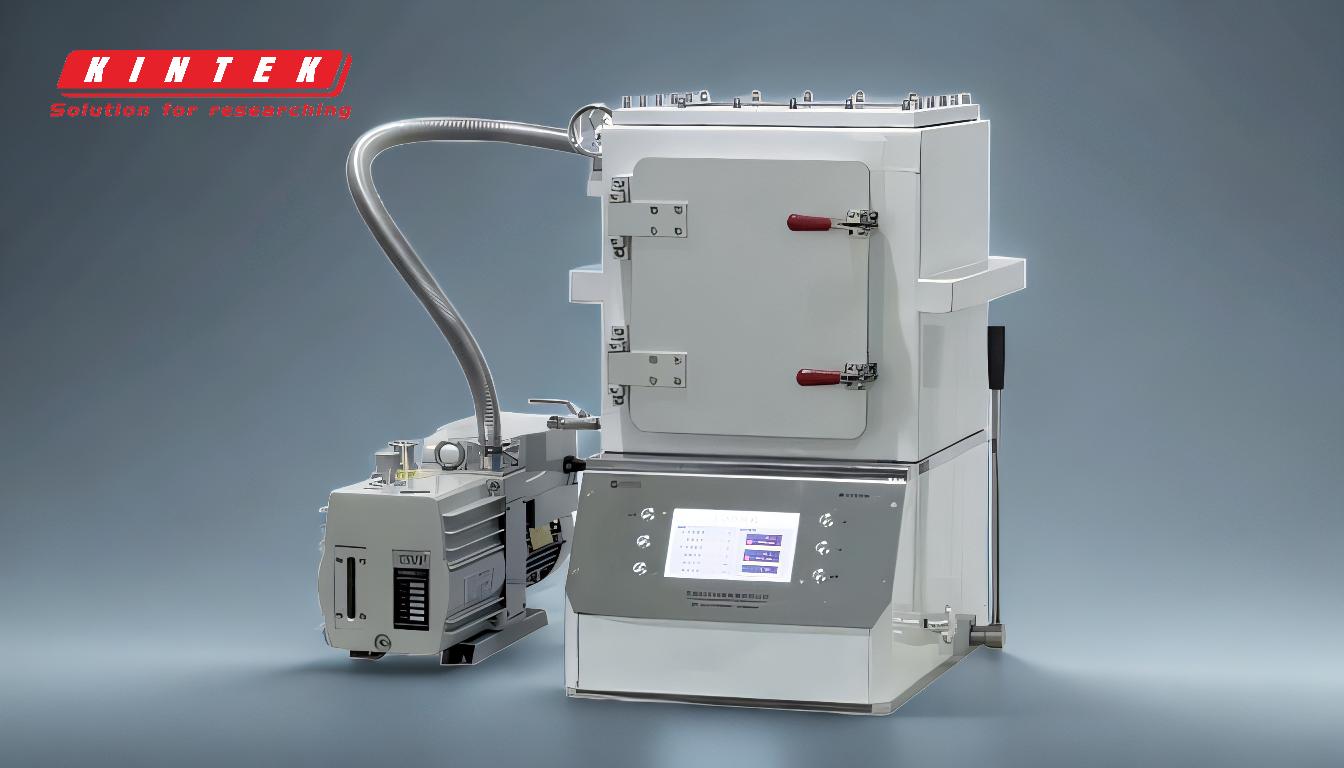
-
Definition and Process of Hydraulic Press Forging:
- Hydraulic press forging involves the use of a hydraulic press to apply force to a metal workpiece, shaping it into the desired form.
- The process typically involves placing the metal between two dies and applying pressure until the metal takes the shape of the dies.
- The hydraulic press uses fluid pressure to generate the force, which allows for precise control over the amount of pressure applied, resulting in more uniform deformation.
-
Advantages of Hydraulic Press Forging:
- Precision and Control: The ability to precisely control the pressure and speed of the press allows for highly accurate and repeatable results.
- Uniform Deformation: Unlike mechanical presses, hydraulic presses apply force evenly across the entire surface of the workpiece, reducing the risk of defects such as cracks or uneven thickness.
- Versatility: Hydraulic presses can be used to forge a wide range of materials, including steel, aluminum, and titanium, making them suitable for various industries.
- High-Strength Components: The process produces components with superior mechanical properties, including high strength and durability, which are essential for critical applications in industries like aerospace and automotive.
-
Applications of Hydraulic Press Forging:
- Automotive Industry: Used to manufacture critical components such as engine parts, transmission components, and suspension parts.
- Aerospace Industry: Essential for producing high-strength, lightweight components such as turbine blades and structural parts.
- Heavy Machinery: Used to create large, durable components for construction equipment, mining machinery, and other heavy-duty applications.
-
Hydraulic Hot Press Machine:
- A hydraulic hot press machine is specifically designed for forging operations that require high temperatures.
- These machines are equipped with heating elements to bring the metal to the optimal temperature for forging, which enhances the material's malleability and reduces the force required for deformation.
- The combination of heat and hydraulic pressure allows for the efficient production of complex shapes and high-strength components.
-
Comparison with Other Forging Methods:
- Mechanical Press Forging: Unlike hydraulic presses, mechanical presses use a flywheel to generate force, which can lead to less control over the forging process and higher risk of defects.
- Drop Forging: This method involves dropping a hammer onto the metal to shape it, which can result in less uniform deformation compared to hydraulic press forging.
- Roll Forging: While roll forging is effective for certain applications, it is less versatile than hydraulic press forging and may not be suitable for producing complex shapes.
-
Considerations for Equipment Selection:
- Force Capacity: The required force capacity of the hydraulic press depends on the size and type of components being forged.
- Temperature Control: For hot forging applications, the ability to control and maintain the temperature of the metal is crucial.
- Die Design: The design of the dies used in the press must be carefully considered to ensure that the final product meets the required specifications.
- Maintenance and Durability: Hydraulic presses require regular maintenance to ensure optimal performance and longevity, especially when used in high-temperature environments.
In summary, hydraulic press forging is a highly effective and versatile manufacturing process that offers numerous advantages over traditional forging methods. The use of a hydraulic hot press machine further enhances the process by allowing for the efficient production of high-strength, complex components. When selecting equipment for hydraulic press forging, it is important to consider factors such as force capacity, temperature control, die design, and maintenance requirements to ensure the best possible results.
Summary Table:
Aspect | Details |
---|---|
Definition | Uses hydraulic pressure to shape metal into desired forms with precision. |
Advantages | Precise control, uniform deformation, versatility, high-strength components. |
Applications | Automotive, aerospace, heavy machinery industries. |
Key Equipment | Hydraulic hot press machine for high-temperature forging. |
Comparison | Superior to mechanical, drop, and roll forging in control and versatility. |
Equipment Selection | Consider force capacity, temperature control, die design, and maintenance. |
Ready to explore hydraulic press forging for your industry? Contact our experts today to get started!