Working with inert gases requires careful attention to safety, handling, and environmental considerations. While inert gases are generally non-reactive, their use in specific applications, such as mixtures with low hydrogen percentages, introduces unique risks and precautions. Understanding the properties, safe handling practices, and potential hazards of inert gases is crucial to ensure safety and efficiency in their use.
Key Points Explained:
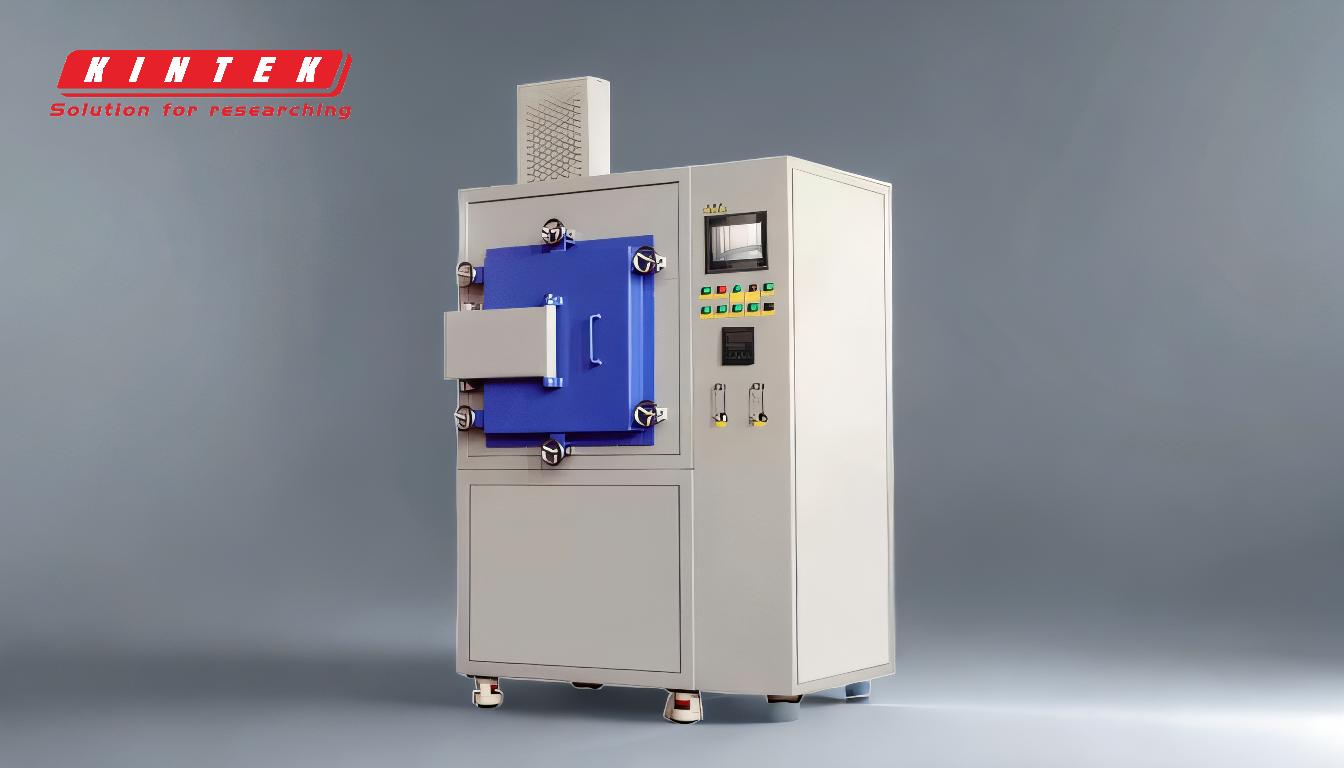
-
Understanding Inert Gas Properties
- Inert gases, such as nitrogen (N₂), argon (Ar), and helium (He), are chemically non-reactive under most conditions. This makes them useful for applications like blanketing, purging, and preventing oxidation.
- However, their lack of reactivity does not mean they are entirely safe. Inert gases can displace oxygen in confined spaces, leading to asphyxiation hazards.
-
Handling Inert Gas Mixtures with Hydrogen
- Mixtures of inert gases with low hydrogen percentages (e.g., >5.5 mol% hydrogen in nitrogen or >3 mol% hydrogen in argon) can be used without the stringent safety measures required for pure hydrogen.
- These mixtures are less prone to ignition and explosion risks compared to higher hydrogen concentrations. However, they still require careful monitoring to avoid accidental over-pressurization or leaks.
-
Safety Measures for Inert Gas Use
- Ventilation: Ensure proper ventilation in workspaces to prevent the accumulation of inert gases, which can displace oxygen and create hazardous conditions.
- Leak Detection: Regularly inspect equipment for leaks, especially when using gas mixtures. Hydrogen, even in low concentrations, can escape through small openings.
- Pressure Monitoring: Use pressure regulators and monitors to prevent over-pressurization of systems, which can lead to equipment failure or gas release.
-
Storage and Transportation
- Store inert gases in approved, well-labeled cylinders or tanks. Ensure storage areas are well-ventilated and away from heat sources or flammable materials.
- During transportation, secure cylinders to prevent tipping or damage, which could result in leaks or ruptures.
-
Personal Protective Equipment (PPE)
- When working with inert gases, wear appropriate PPE, such as gloves, safety goggles, and, in some cases, respiratory protection, especially in confined spaces.
- For mixtures containing hydrogen, flame-resistant clothing may be necessary to mitigate fire risks.
-
Emergency Preparedness
- Have emergency response plans in place, including procedures for gas leaks, fires, or asphyxiation incidents.
- Ensure all personnel are trained in the proper use of gas detection equipment and emergency shut-off systems.
-
Environmental Considerations
- Inert gases, while non-toxic, can contribute to environmental issues if released in large quantities. For example, argon is a greenhouse gas, and its release should be minimized.
- Proper disposal and recycling of gas cylinders and associated equipment are essential to reduce environmental impact.
-
Regulatory Compliance
- Adhere to local and international regulations governing the use, storage, and transportation of inert gases. This includes compliance with OSHA, EPA, and other relevant standards.
- Maintain accurate records of gas usage, inspections, and safety training to ensure compliance and accountability.
By understanding these key points, individuals and organizations can safely and effectively work with inert gases, minimizing risks and maximizing the benefits of their applications.
Summary Table:
Key Aspect | Details |
---|---|
Properties | Non-reactive gases like nitrogen, argon, and helium; can displace oxygen. |
Handling Mixtures | Low hydrogen percentages reduce risks; monitor for leaks and overpressure. |
Safety Measures | Ventilation, leak detection, and pressure monitoring are critical. |
Storage & Transportation | Use approved cylinders; secure during transport to prevent leaks. |
PPE | Gloves, goggles, and flame-resistant clothing for hydrogen mixtures. |
Emergency Preparedness | Train personnel on gas detection and emergency shut-off systems. |
Environmental Impact | Minimize argon release; recycle cylinders to reduce environmental harm. |
Regulatory Compliance | Follow OSHA, EPA, and other standards; maintain accurate records. |
Ensure your team is prepared to handle inert gases safely—contact us today for expert guidance!