Induction heating equipment is a technology used to heat electrically conductive materials, such as metals, through electromagnetic induction. It generates heat by creating an alternating magnetic field using an induction coil powered by an alternating current (AC) source. This field induces eddy currents within the material, which produce heat due to electrical resistance. Induction heating is widely used in industrial applications like heat treatment, melting, brazing, and surface hardening, as well as in domestic applications like induction cooktops. The equipment typically includes components such as an RF power supply, induction coil, and cooling systems, and it is valued for its precision, efficiency, and ability to heat materials quickly and uniformly.
Key Points Explained:
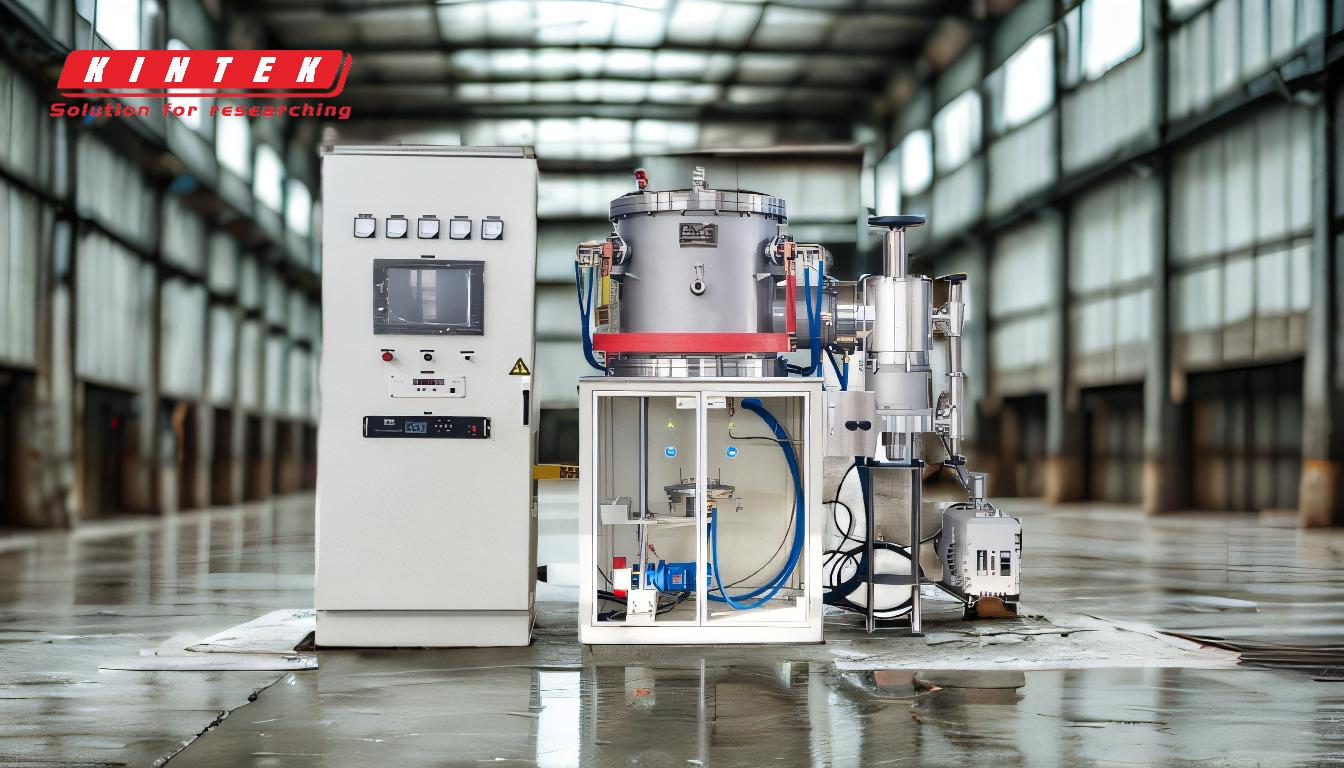
-
Definition and Principle of Induction Heating Equipment:
- Induction heating equipment uses electromagnetic induction to generate heat in conductive materials.
- An alternating current (AC) source powers an induction coil, creating an alternating magnetic field.
- When a conductive material is placed within this field, eddy currents are induced, producing heat due to the material's electrical resistance.
- This process is efficient, precise, and allows for localized heating without direct contact.
-
Components of Induction Heating Equipment:
- RF Power Supply: Provides the alternating current required to generate the magnetic field.
- Induction Coil: Typically made of copper, it creates the alternating magnetic field when energized by the power supply.
- Chiller: Cools the system to prevent overheating of components.
- Vacuum Unit: Used in specialized applications like vacuum furnaces for melting metals or creating alloys.
- Workpiece: The material to be heated, which must be electrically conductive.
-
Applications of Induction Heating Equipment:
-
Industrial Applications:
- Heat treatment (e.g., surface hardening, annealing).
- Melting refractory metals and alloys.
- Brazing, soldering, and welding.
- Zone refining and crystal growth in the semiconductor industry.
-
Medical Applications:
- Heating biological tissues for therapeutic purposes.
-
Domestic Applications:
- Induction cooktops for efficient and precise cooking.
-
Specialized Uses:
- Tamper-resistant cap sealing in pharmaceuticals.
- Heating liquid and gaseous conductors.
- Improving energy efficiency in plastic injection molding.
-
Industrial Applications:
-
Advantages of Induction Heating Equipment:
- Precision: Allows for targeted heating of specific areas.
- Efficiency: Converts electrical energy directly into heat with minimal losses.
- Speed: Heats materials rapidly compared to traditional methods.
- Consistency: Provides uniform heating, ensuring high-quality results.
- Safety: No open flames or direct contact with heat sources, reducing risks.
-
Emerging Trends and Future Developments:
- Expansion into heating low-resistivity materials and biological tissues.
- Ongoing research to optimize process parameters for new applications.
- Integration with advanced technologies for enhanced control and automation.
- Development of more compact and energy-efficient systems for diverse industries.
-
Common Industrial Processes Using Induction Heating:
- Surface Hardening: Heating the surface of steel parts to high temperatures followed by rapid quenching, leaving the core unaffected.
- Brazing and Soldering: Joining metals using filler materials melted by induction heating.
- Hot Forging: Heating small workpieces (e.g., round bars) to high temperatures for shaping.
- Melting: Used in inductive furnaces to melt metals for casting or alloy production.
-
Key Considerations for Equipment Selection:
- Material properties (e.g., resistivity, magnetic permeability).
- Required heating depth and temperature range.
- Application-specific requirements (e.g., surface hardening, melting).
- System size, power capacity, and cooling needs.
- Budget and energy efficiency considerations.
Induction heating equipment is a versatile and essential tool in modern manufacturing and domestic applications, offering unparalleled precision, efficiency, and adaptability across a wide range of industries.
Summary Table:
Key Aspect | Details |
---|---|
Principle | Uses electromagnetic induction to heat conductive materials via eddy currents. |
Components | RF power supply, induction coil, chiller, vacuum unit, workpiece. |
Applications | Heat treatment, melting, brazing, surface hardening, induction cooktops. |
Advantages | Precision, efficiency, speed, consistency, and safety. |
Future Trends | Heating low-resistivity materials, automation, compact systems. |
Selection Considerations | Material properties, heating depth, temperature range, budget, and cooling. |
Ready to explore induction heating solutions? Contact us today for expert guidance!