The levitation melting technique is a non-contact method used to melt metals without allowing them to come into contact with any crucible or heating elements. This is achieved by suspending the metal in mid-air using an electromagnetic field generated by an alternating current. The process leverages the principles of electromagnetic induction and Lenz’s law, where the metal is levitated due to the opposing magnetic fields created by induced currents. This technique ensures that the molten metal remains pure and uncontaminated, making it ideal for high-precision applications.
Key Points Explained:
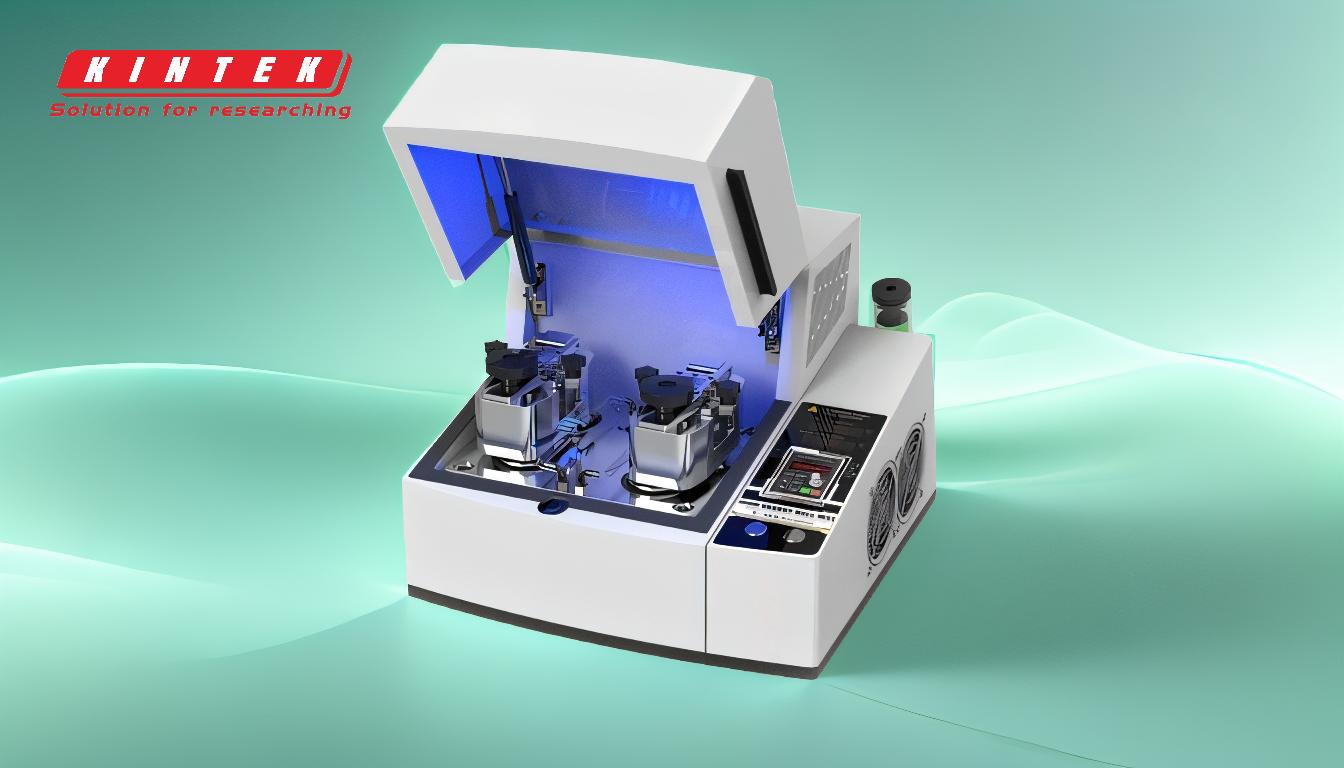
-
Non-Contact Melting Method:
- Levitation melting is a non-contact technique, meaning the metal does not touch any crucible or heating elements during the melting process. This is crucial for maintaining the purity of the metal, as it prevents contamination that could occur from contact with other materials.
- The absence of physical contact also reduces wear and tear on equipment, extending the lifespan of the melting apparatus.
-
Electromagnetic Levitation:
- The metal is suspended in mid-air using an electromagnetic field. This field is generated by an alternating current, which induces a current within the metal billet.
- The induced current creates its own magnetic field, which opposes the original magnetic field, resulting in levitation. This principle is similar to the phenomenon observed when dropping a strong magnet down a copper pipe, where the magnet's motion induces currents that create an opposing field.
-
Induction Levitation and Lenz’s Law:
- Induction levitation is based on Lenz’s law, which states that an induced current will flow in a direction that opposes the change that produced it. In the context of levitation melting, this means that the metal will generate a magnetic field that opposes the applied electromagnetic field, causing it to levitate.
- This principle is harnessed in induction furnaces, where a constantly changing magnetic field induces currents in the metal, creating the necessary opposing fields for levitation.
-
Advantages of Levitation Melting:
- Purity: Since the metal does not come into contact with any crucible or heating elements, it remains uncontaminated, which is essential for high-purity applications such as in the aerospace and semiconductor industries.
- Precision: The technique allows for precise control over the melting process, enabling the production of metals with specific properties and compositions.
- Efficiency: The non-contact nature of the process reduces energy losses associated with heat transfer through physical contact, making it more energy-efficient.
-
Applications:
- Levitation melting is widely used in industries that require high-purity metals, such as aerospace, where even minor impurities can compromise the integrity of components.
- It is also used in research and development for creating new alloys and studying the properties of molten metals under controlled conditions.
In summary, the levitation melting technique is a sophisticated method that leverages electromagnetic principles to melt metals without contamination. Its non-contact nature, combined with the precision and purity it offers, makes it an invaluable tool in industries where material integrity is paramount.
Summary Table:
Key Aspect | Details |
---|---|
Non-Contact Melting | Prevents contamination by avoiding contact with crucibles or heating elements. |
Electromagnetic Levitation | Metal is suspended using an electromagnetic field generated by alternating current. |
Lenz’s Law Application | Induced currents create opposing magnetic fields, enabling levitation. |
Advantages | - Purity: No contamination. - Precision: Controlled melting. - Efficiency: Energy-saving. |
Applications | Aerospace, semiconductor industries, and R&D for high-purity metals. |
Learn how levitation melting can revolutionize your metal processing—contact us today!