A microwave sintering furnace is a specialized type of furnace that uses microwave radiation as a heating source to sinter materials, particularly ceramics. Unlike conventional sintering methods, which rely on external heating elements, microwave sintering leverages the dielectric properties of materials to generate heat internally. This results in uniform heating, reduced energy consumption, and faster sintering times. Microwave sintering furnaces can operate in controlled atmospheres, including vacuum, inert, or reducing environments, and are available in both batch and continuous processing configurations. They are highly efficient, energy-saving, and capable of producing high-quality, fine-grained materials with minimal oxidation or contamination. These furnaces are widely used in advanced material preparation and offer significant advantages over traditional sintering methods.
Key Points Explained:
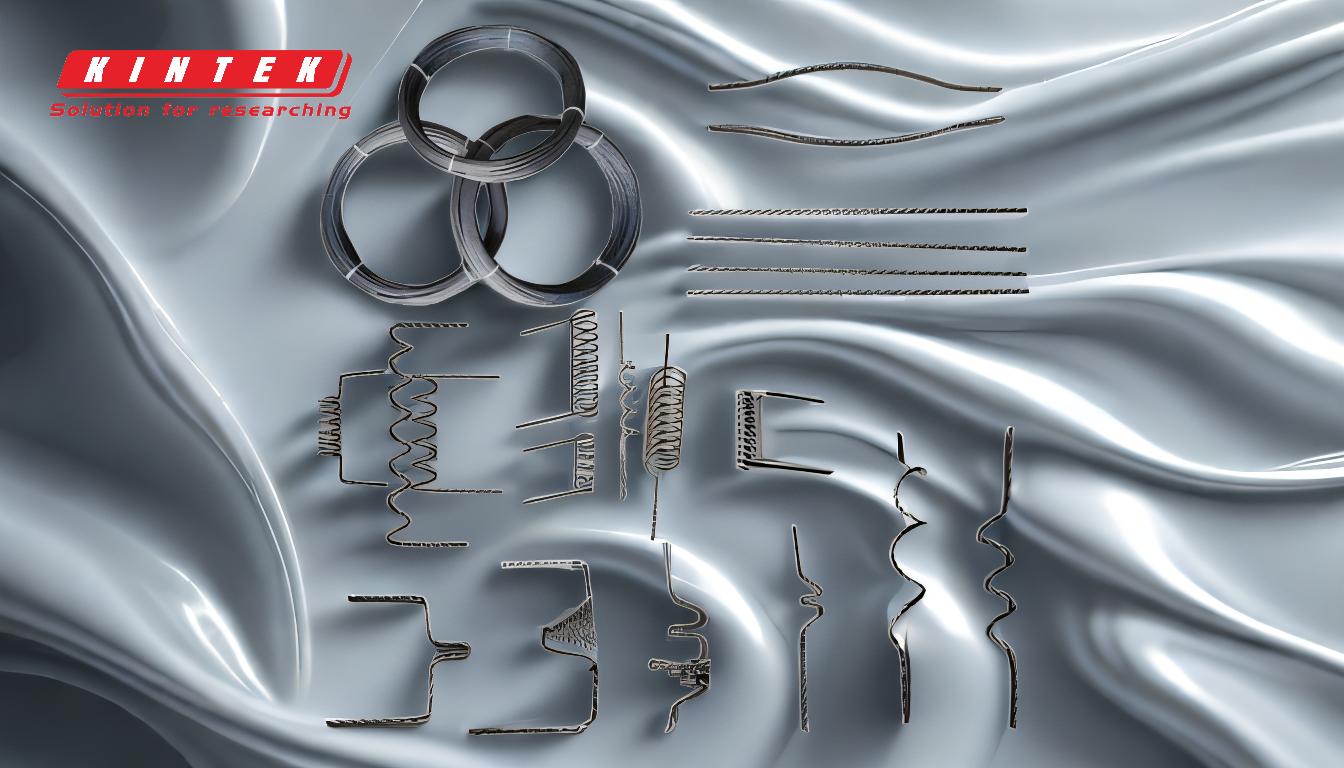
-
Heating Mechanism:
- Microwave sintering furnaces use microwave radiation to heat materials internally through dielectric loss. This process is fundamentally different from conventional furnaces, which rely on external heat sources.
- The microwave energy couples with the microstructure of ceramic materials, generating heat that raises the material to the sintering temperature.
- This internal heating mechanism ensures uniform temperature distribution and minimizes thermal gradients, which is critical for producing high-quality sintered materials.
-
Advantages Over Conventional Sintering:
- Fast Heating Speed: Microwave sintering significantly reduces heating times compared to traditional methods.
- Lower Sintering Temperatures: Materials can be sintered at lower temperatures, which is beneficial for heat-sensitive materials.
- Energy Efficiency: The process consumes less energy due to its rapid and targeted heating capabilities.
- Improved Material Properties: Microwave sintering results in better material density and fine-grained microstructures, enhancing mechanical and thermal properties.
- Environmental Friendliness: The closed environment prevents oxidation and contamination, making it a cleaner process.
-
Design and Components:
- A typical microwave sintering furnace consists of:
- Microwave Source: Generates the microwave radiation used for heating.
- Heating Cavity: The chamber where the material is placed and heated.
- Material Transfer System: Facilitates the movement of materials in continuous processing setups.
- Advanced features include non-contact temperature monitoring, step-less power control, and digital displays for power and temperature.
- A typical microwave sintering furnace consists of:
-
Operational Flexibility:
- Microwave sintering furnaces can operate in various atmospheres, including inert, reducing, or oxidizing environments, as well as under vacuum conditions.
- They are available in batch and continuous configurations, with continuous furnaces capable of processing 50 to 1000 kg/day.
-
Applications:
- Microwave sintering is particularly advantageous for ceramic materials, where uniform heating and fine-grained microstructures are essential.
- It is also used in advanced material preparation, including composites, metals, and nanomaterials, due to its ability to achieve low-temperature and rapid sintering.
-
Hybrid Furnaces:
- Some microwave sintering furnaces combine microwave energy with electrical heaters for materials that do not absorb microwaves effectively at lower temperatures.
- This hybrid approach ensures efficient heating across a wide range of materials and temperature ranges.
-
Process Control and Automation:
- Modern microwave sintering furnaces feature advanced process control systems, including high-end PID controllers and industrial PLCs with touch screen interfaces.
- These systems enable precise control over heating rates, temperature, and atmosphere, ensuring consistent and reproducible results.
For more detailed information on sintering furnaces, you can explore sintering furnace.
Summary Table:
Feature | Description |
---|---|
Heating Mechanism | Uses microwave radiation for internal heating via dielectric loss, ensuring uniform temperature. |
Advantages | - Fast heating speed |
- Lower sintering temperatures
- Energy-efficient
- Improved material properties | | Design Components | - Microwave source
- Heating cavity
- Material transfer system
- Advanced control features | | Operational Flexibility | Operates in vacuum, inert, or reducing atmospheres; available in batch or continuous setups. | | Applications | Ideal for ceramics, composites, metals, and nanomaterials due to rapid, low-temperature sintering.| | Hybrid Furnaces | Combines microwave energy with electrical heaters for broader material compatibility. | | Process Control | Features PID controllers, PLCs, and touch screens for precise temperature and atmosphere control. |
Transform your material processing with a microwave sintering furnace—contact us today to learn more!