Microwave sintering of ceramic materials is an advanced sintering technique that utilizes microwave energy to heat and densify ceramic materials. This method offers several advantages over traditional sintering, including fast heating speeds, uniform temperature distribution, energy efficiency, and the ability to produce high-quality ceramic materials with improved mechanical properties. Microwave sintering is particularly effective for preparing high-performance ceramics, including sub-meter or micron-level materials, due to its ability to inhibit grain growth and achieve high densification rates. The process involves the absorption of microwave energy by the ceramic material, which generates heat internally, leading to rapid and uniform heating. This technique is scalable and environmentally friendly, making it a promising option for advanced ceramic material preparation.
Key Points Explained:
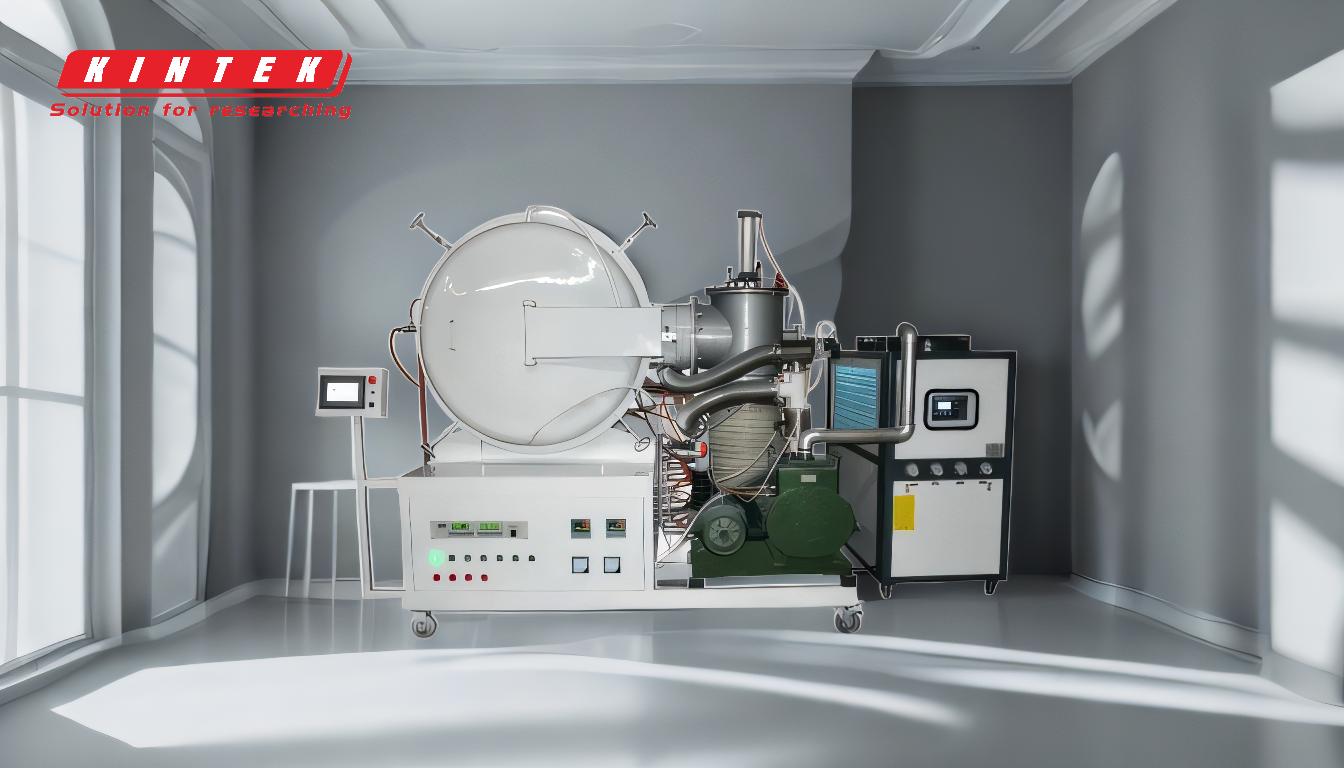
-
Definition and Mechanism of Microwave Sintering:
- Microwave sintering is a process where ceramic materials are heated using microwave energy. The material absorbs microwave radiation, which causes dielectric loss, generating heat internally. This internal heating results in uniform temperature distribution and a small internal temperature gradient, enabling low-temperature and rapid sintering.
-
Advantages of Microwave Sintering:
- Fast Heating Speed: Microwave sintering allows for rapid heating, which increases the densification speed and inhibits grain growth, leading to finer microstructures and improved mechanical properties.
- Uniform Temperature Distribution: The internal heating mechanism ensures uniform temperature distribution, reducing the risk of thermal stress and cracking.
- Energy Efficiency: Microwave sintering is more energy-efficient compared to traditional methods, as it directly heats the material rather than relying on external heat sources.
- Environmental Friendliness: The process reduces energy consumption and minimizes pollution, making it an environmentally friendly option.
- High-Quality Products: The uniform heating and rapid sintering process result in high-quality ceramic materials with improved mechanical properties.
-
Applications of Microwave Sintering:
- High-Performance Ceramics: Microwave sintering is widely used in the preparation of high-performance ceramic materials, including those used in aerospace, electronics, and biomedical applications.
- Sub-Meter and Micron-Level Ceramics: The technique is particularly effective for preparing sub-meter or even micron-level ceramic materials, offering high production efficiency and low unit cost.
- Complex Shapes and Structures: Microwave sintering can be used to produce ceramic components with complex shapes and structures that are difficult to achieve with conventional sintering methods.
-
Challenges and Solutions:
- Cooling Challenges: One of the challenges of microwave sintering is the cooling of the operating equipment. This can be addressed with auxiliary cooling systems to maintain optimal operating conditions.
- Susceptor Materials: Microwave sintering often requires the use of susceptor plates and materials in the sintering trays to absorb microwave energy and convert it to heat. These materials must be carefully selected to ensure efficient energy absorption and heat transfer.
-
Comparison with Traditional Sintering Methods:
- Heating Mechanism: Unlike traditional sintering methods that rely on external heat sources, microwave sintering uses internal heating, which results in faster and more uniform heating.
- Energy Consumption: Microwave sintering is more energy-efficient, reducing overall energy consumption and operational costs.
- Material Properties: The rapid and uniform heating in microwave sintering leads to better control over material properties, such as grain size and density, resulting in superior mechanical properties.
-
Future Prospects:
- Scalability: Microwave sintering is scalable and can be adapted for larger volume production, making it suitable for industrial applications.
- Advanced Materials: The technique holds promise for the preparation of advanced ceramic materials with tailored properties for specific applications.
- Research and Development: Ongoing research and development in microwave sintering are expected to further enhance its capabilities and expand its applications in various industries.
In summary, microwave sintering is a cutting-edge technique that offers numerous advantages over traditional sintering methods, including faster heating, uniform temperature distribution, energy efficiency, and the ability to produce high-quality ceramic materials. Its applications in high-performance ceramics and advanced material preparation make it a valuable tool in modern manufacturing and research.
Summary Table:
Aspect | Details |
---|---|
Heating Mechanism | Internal heating via microwave energy absorption |
Advantages | Fast heating, uniform temperature, energy efficiency, eco-friendly |
Applications | High-performance ceramics, sub-meter/micron materials, complex shapes |
Challenges | Cooling equipment, susceptor material selection |
Comparison with Traditional Methods | Faster, more energy-efficient, superior material properties |
Future Prospects | Scalability, advanced materials, ongoing R&D |
Ready to explore microwave sintering for your ceramic needs? Contact us today to learn more!