Molybdenum disilicide (MoSi2) is a versatile intermetallic compound and refractory ceramic widely used in high-temperature applications due to its exceptional thermal, electrical, and chemical properties. It is primarily employed in heating elements for industrial furnaces, capable of withstanding temperatures up to 1800 °C. Its applications span across industries such as glass manufacturing, ceramics, metallurgy, electronics, and heat treatment processes. MoSi2 forms a protective silicon dioxide layer at high temperatures, enhancing its oxidation resistance and durability. Additionally, its electrical conductivity and thermal shock resistance make it suitable for specialized applications like thermocouples and components in aerospace technology.
Key Points Explained:
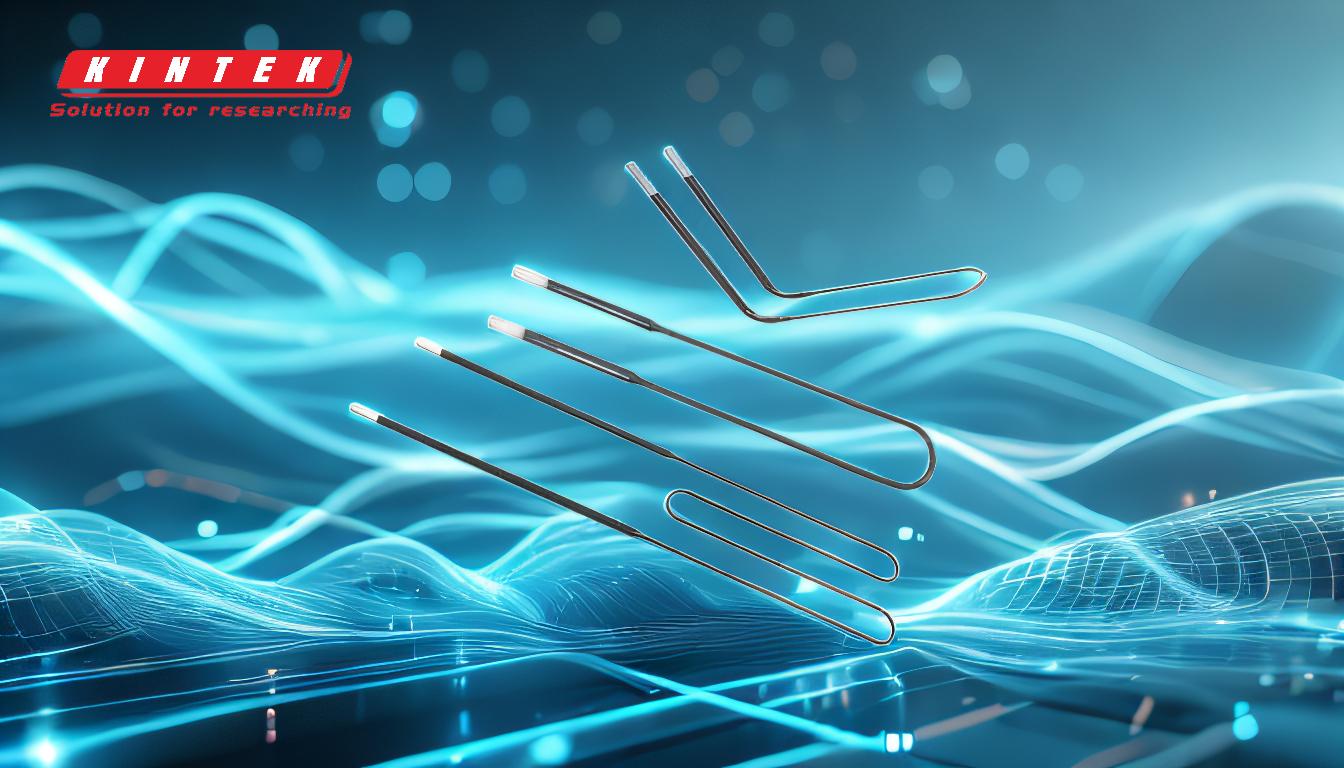
-
High-Temperature Heating Elements:
- MoSi2 is extensively used in heating elements for industrial and laboratory furnaces. These elements can operate at temperatures up to 1800 °C, making them ideal for high-temperature processes.
- Applications include:
- Glass manufacturing.
- Ceramic sintering.
- Heat treatment furnaces.
- Semiconductor diffusion furnaces.
- Its ability to form a protective silicon dioxide layer at high temperatures ensures long-term durability and resistance to oxidation.
-
Industrial Applications:
- Glass Industry: MoSi2 heating elements are used in glass kilns for melting and forming glass products.
- Ceramics: It is employed in sintering furnaces for producing advanced ceramics and refractory materials.
- Metallurgy: Used in smelting and casting furnaces for metal processing.
- Electronics: Utilized in semiconductor diffusion furnaces for manufacturing electronic components.
-
Specialized Equipment:
- MoSi2 heating elements are integrated into various high-temperature equipment, including:
- Vacuum furnaces.
- Tunnel kilns.
- Roller kilns.
- Experimental electric furnaces.
- Denture sintering furnaces.
- These applications leverage its thermal stability and electrical conductivity.
- MoSi2 heating elements are integrated into various high-temperature equipment, including:
-
Aerospace and Defense:
- MoSi2's thermal shock resistance and electrical properties make it suitable for specialized components in aerospace technology, such as:
- High-temperature thermocouples.
- Components for rockets and missiles.
- MoSi2's thermal shock resistance and electrical properties make it suitable for specialized components in aerospace technology, such as:
-
Advantages of MoSi2:
- High Melting Point: With a melting point of 2030 °C, it is suitable for extreme temperature environments.
- Oxidation Resistance: The formation of a silicon dioxide passivation layer protects it from further oxidation.
- Thermal Shock Resistance: It can withstand rapid temperature changes without cracking or degrading.
- Electrical Conductivity: Enables efficient heating in electric furnaces.
-
Diverse Industry Use:
- MoSi2 is a critical material in industries requiring high-temperature processing, including:
- Magnetic materials production.
- Refractory materials manufacturing.
- Crystal growth processes.
- Its versatility and reliability make it a preferred choice for high-temperature furnace heating.
- MoSi2 is a critical material in industries requiring high-temperature processing, including:
In summary, molybdenum disilicide is a crucial material in high-temperature industrial processes, offering unmatched thermal stability, oxidation resistance, and electrical conductivity. Its applications range from glass and ceramics to aerospace technology, making it indispensable in modern manufacturing and research.
Summary Table:
Key Features | Applications |
---|---|
High melting point (2030 °C) | Heating elements for industrial furnaces (up to 1800 °C) |
Oxidation resistance | Glass manufacturing, ceramic sintering, metallurgy, electronics |
Thermal shock resistance | Aerospace components, thermocouples, rocket and missile parts |
Electrical conductivity | Semiconductor diffusion furnaces, vacuum furnaces, tunnel kilns |
Versatile industry use | Magnetic materials, refractory materials, crystal growth processes |
Learn how MoSi2 can enhance your high-temperature processes—contact our experts today!