The MPCVD (Microwave Plasma Chemical Vapor Deposition) method is a sophisticated technique used for the deposition of high-quality diamond films. It utilizes microwave energy to excite gases into a plasma state, which then facilitates the deposition process. This method is particularly noted for its efficiency, stability, and the high quality of the resulting films. It operates without electrodes, which enhances its energy efficiency and allows for continuous operation over extended periods. The process is scalable and can be adapted for larger substrates, making it highly versatile for various industrial applications.
Key Points Explained:
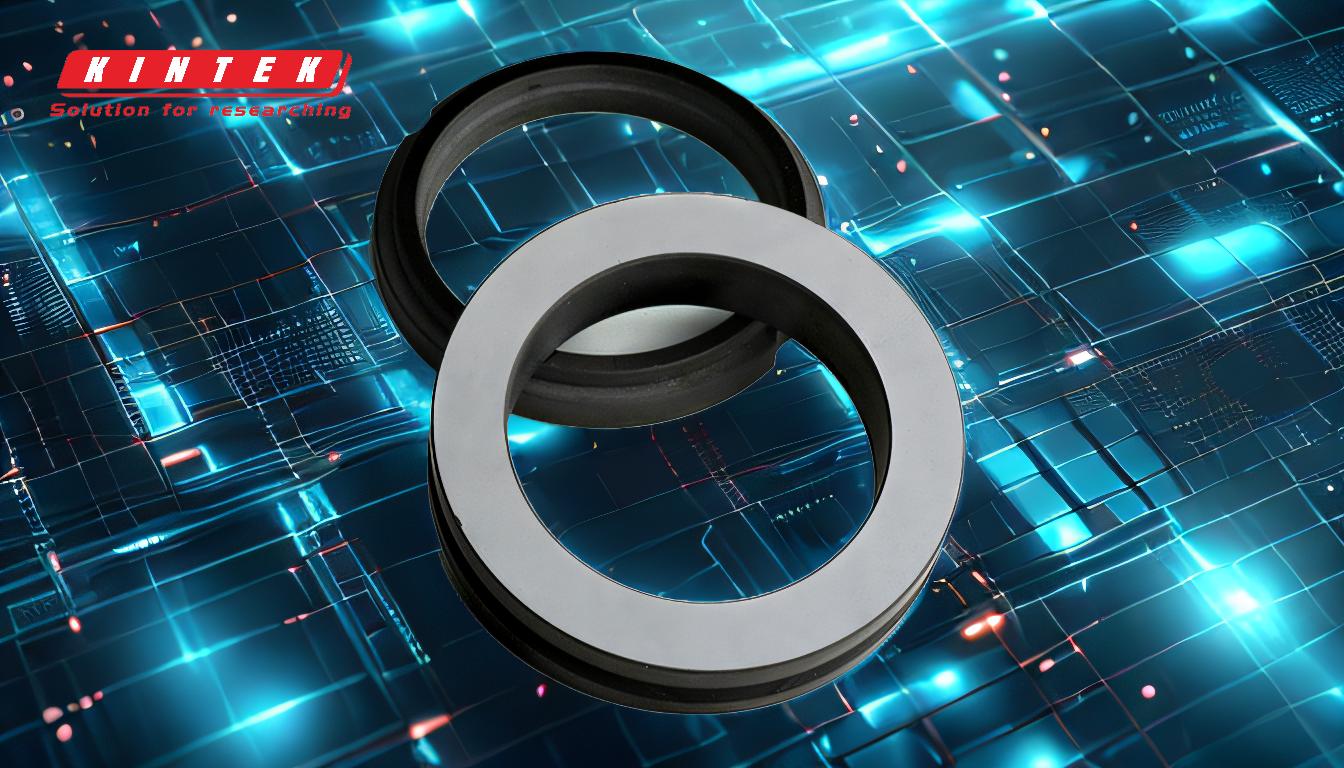
-
Principle of MPCVD:
- The MPCVD method employs microwave energy to transform the deposited gas into a plasma state. This is achieved through the electromagnetic field generated by microwaves, which causes electrons in the cavity to collide and oscillate vigorously.
- These collisions enhance the dissociation of the reactive gas, leading to the generation of a high-density plasma. The ionization degree of the feed gas can surpass 10%, resulting in a cavity filled with supersaturated atomic hydrogen and carbon-containing groups. This environment significantly improves both the deposition rate and the quality of the diamond film.
-
Advantages of MPCVD:
- Electrode-less Process: The absence of electrodes not only makes the process more energy-efficient but also reduces contamination, which is crucial for the purity of the deposited film.
- Stability and Reproducibility: The non-isothermal plasma generated is stable and reproducible, allowing for continuous deposition over many hours or even days without degradation in film quality.
- Modular and Scalable: The use of modular units with a 1-2 KW microwave power supply makes the system readily adaptable and scalable for larger substrates, enhancing its applicability in various industrial settings.
-
Comparison with Remote PECVD:
- Unlike MPCVD, the remote PECVD method generates plasma of reactant gases and any inert gas remotely. The active species are then transported to a plasma-free region where they react with additional reactants to form precursor molecules.
- The film deposition occurs in this plasma-free region, which can reduce the risk of plasma-induced damage to the substrate. However, this method may not achieve the same high ionization degree and plasma density as MPCVD, potentially affecting the deposition rate and film quality.
By understanding these key aspects, purchasers and users of MPCVD equipment can better appreciate the method's capabilities and advantages, ensuring they select the most appropriate technology for their specific needs in diamond film deposition.
Summary Table:
Aspect | Details |
---|---|
Principle | Uses microwave energy to create high-density plasma for diamond deposition. |
Advantages | Electrode-less, energy-efficient, stable, reproducible, and scalable. |
Comparison to PECVD | Higher ionization degree and plasma density for superior film quality. |
Discover how MPCVD can revolutionize your diamond film deposition process—contact our experts today!