In vacuum heat treatment, partial pressure refers to the pressure exerted by a specific gas within a mixture of gases in a vacuum environment. This concept is crucial because it allows precise control over the atmosphere during the heat treatment process, ensuring desired outcomes such as surface finishes, material properties, and contamination prevention. By manipulating partial pressures, manufacturers can optimize conditions for specific materials and processes, such as preventing oxidation or enhancing diffusion rates. This approach is particularly valuable in industries requiring high precision, such as aerospace and medical device manufacturing.
Key Points Explained:
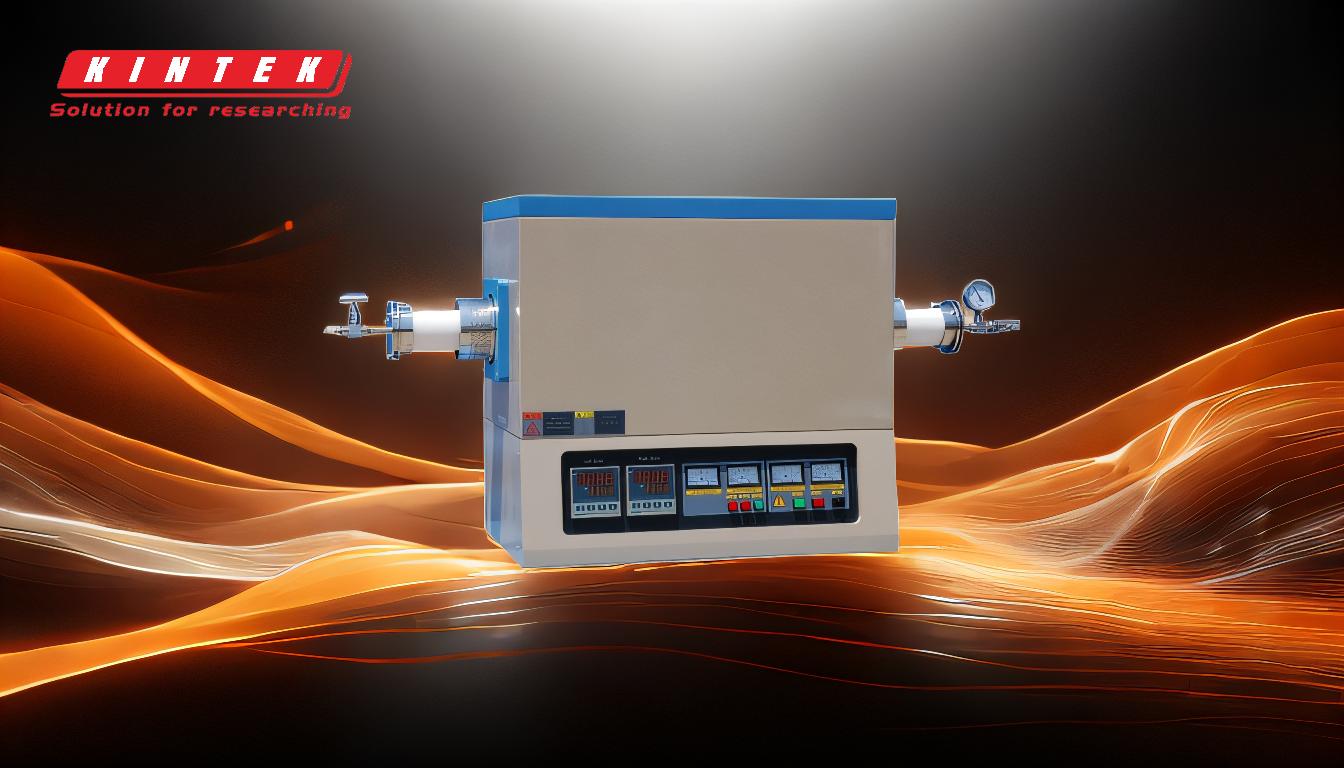
-
Understanding Partial Pressure in Vacuum Heat Treatment:
- Partial pressure is the pressure contributed by a single gas in a mixture of gases within a vacuum chamber. In vacuum heat treatment, this concept is used to control the atmosphere and achieve specific material properties.
- For example, introducing a small amount of nitrogen or argon at a controlled partial pressure can prevent oxidation while maintaining the benefits of a vacuum environment.
-
Role of Vacuum in Heat Treatment:
- A vacuum environment removes air and other contaminants, creating a controlled atmosphere. This is essential for processes like annealing, brazing, and hardening, where even trace amounts of oxygen or moisture can degrade material quality.
- The vacuum reduces the density of undesirable atoms, minimizing contamination and allowing for precise thermal management.
-
Benefits of Partial Pressure Control:
- Precision: By adjusting the partial pressure of specific gases, manufacturers can fine-tune the heat treatment process to meet exact requirements.
- Surface Quality: Controlled partial pressures can enhance surface finishes, such as preventing discoloration or improving adhesion in coating processes.
- Material Integrity: Maintaining optimal partial pressures ensures that materials retain their desired mechanical and chemical properties.
-
Applications in Industry:
- Partial pressure control is widely used in industries like aerospace, where components must withstand extreme conditions without degradation.
- It is also critical in medical device manufacturing, where materials must meet stringent biocompatibility and performance standards.
-
Challenges and Considerations:
- Achieving and maintaining precise partial pressures requires advanced equipment and monitoring systems.
- The choice of gases and their partial pressures must be carefully tailored to the specific material and treatment process.
By leveraging the principles of partial pressure in vacuum heat treatment, manufacturers can achieve superior results, ensuring that materials meet the highest standards of quality and performance.
Summary Table:
Aspect | Details |
---|---|
Definition | Pressure exerted by a specific gas in a vacuum environment. |
Role in Heat Treatment | Controls atmosphere to prevent oxidation, enhance diffusion, and improve results. |
Key Benefits | - Precision control - Enhanced surface quality - Improved material integrity |
Applications | Aerospace, medical device manufacturing, and other high-precision industries. |
Challenges | Requires advanced equipment and tailored gas selection for optimal results. |
Discover how partial pressure control can optimize your heat treatment process—contact our experts today!