Physical Vapor Deposition (PVD) and Chemical Vapor Deposition (CVD) are two widely used techniques for depositing thin films onto substrates. PVD relies on physical processes, such as evaporation or sputtering, to transform a solid material into a vapor that then condenses onto the substrate. In contrast, CVD uses chemical reactions involving gaseous precursors to form a solid film on the substrate. While PVD operates at lower temperatures and avoids corrosive byproducts, CVD allows for uniform coating of complex geometries and higher deposition rates. Both methods are essential in industries like semiconductors, optics, and coatings, offering unique advantages depending on the application.
Key Points Explained:
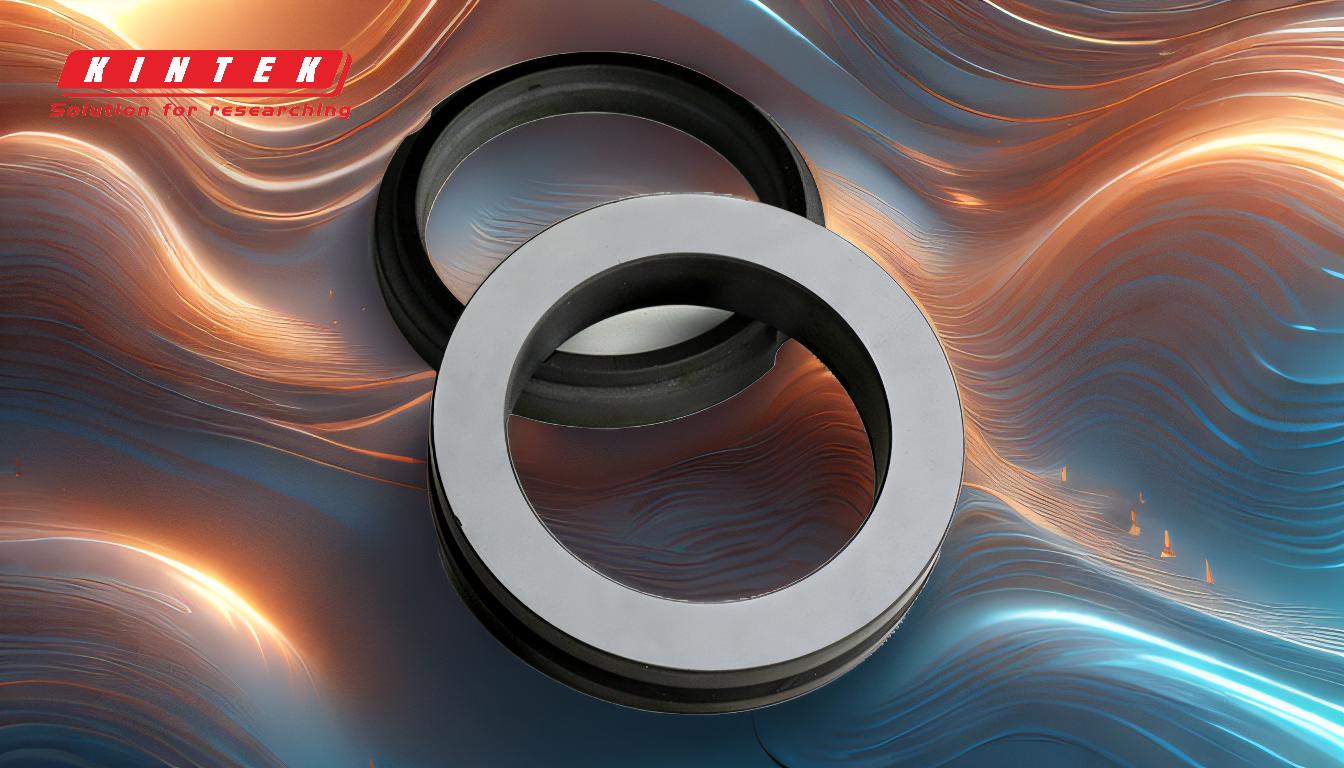
-
Definition and Basic Principles:
- PVD: Physical Vapor Deposition involves transforming a solid material into vapor through physical means (e.g., heating, sputtering). The vapor then condenses onto the substrate to form a thin film.
- CVD: Chemical Vapor Deposition involves gaseous precursors that chemically react or decompose on the substrate surface to form a solid film. This process relies on chemical reactions rather than physical transformations.
-
Process Mechanisms:
-
PVD:
- The solid material is heated above its melting point or bombarded with ions (sputtering) to generate vapor.
- The vaporized atoms or molecules travel to the substrate and deposit as a thin film.
- Common PVD methods include evaporation, sputtering, electron beam, and wire explosion.
-
CVD:
- Gaseous precursors are introduced into a reaction chamber.
- The gases chemically react or decompose on the heated substrate surface, forming a solid film.
- CVD can be thermally activated or plasma-enhanced to improve reaction efficiency.
-
PVD:
-
Key Differences:
-
Material State:
- PVD uses solid materials that are vaporized physically.
- CVD uses gaseous precursors that chemically transform into a solid film.
-
Line of Sight:
- PVD requires a direct line of sight between the target material and the substrate, limiting its ability to coat complex geometries uniformly.
- CVD does not require a line of sight, enabling uniform coating of intricate shapes and multiple parts simultaneously.
-
Temperature and Byproducts:
- PVD operates at lower temperatures and does not produce corrosive byproducts.
- CVD often requires high temperatures, which can lead to corrosive gaseous byproducts and potential impurities in the film.
-
Material State:
-
Advantages and Limitations:
-
PVD:
- Advantages: Lower deposition temperatures, no corrosive byproducts, high material utilization efficiency (e.g., EBPVD offers high deposition rates).
- Limitations: Limited to line-of-sight deposition, lower deposition rates compared to CVD.
-
CVD:
- Advantages: Uniform coating of complex geometries, higher deposition rates, ability to coat multiple parts in one reaction.
- Limitations: High temperatures and corrosive byproducts, potential for impurities in the film.
-
PVD:
-
Applications:
-
PVD:
- Commonly used for decorative coatings, wear-resistant coatings, and semiconductor devices.
- Examples include titanium nitride coatings on cutting tools and aluminum coatings on packaging materials.
-
CVD:
- Widely used in semiconductor manufacturing, optical coatings, and protective coatings.
- Examples include silicon dioxide and silicon nitride films in microelectronics and diamond-like carbon coatings.
-
PVD:
-
Material Utilization and Efficiency:
- PVD: High material utilization efficiency, especially in methods like EBPVD, where deposition rates range from 0.1 to 100 μm/min.
- CVD: Efficient for coating complex shapes and multiple parts simultaneously, but may involve higher material costs due to the use of gaseous precursors.
-
Environmental and Safety Considerations:
- PVD: Generally safer and more environmentally friendly due to lower temperatures and absence of corrosive byproducts.
- CVD: Requires careful handling of reactive gases and management of corrosive byproducts, which can pose safety and environmental challenges.
By understanding these key points, a purchaser of equipment or consumables can make informed decisions about whether PVD or CVD is more suitable for their specific application, considering factors like substrate geometry, deposition rate, temperature sensitivity, and environmental impact.
Summary Table:
Aspect | PVD | CVD |
---|---|---|
Material State | Solid materials vaporized physically | Gaseous precursors chemically transformed into a solid film |
Line of Sight | Requires direct line of sight; limited for complex geometries | No line of sight required; uniform coating of intricate shapes |
Temperature | Lower temperatures; no corrosive byproducts | High temperatures; potential corrosive byproducts |
Deposition Rate | Lower compared to CVD | Higher deposition rates |
Applications | Decorative coatings, wear-resistant coatings, semiconductors | Semiconductors, optical coatings, protective coatings |
Environmental Impact | Safer and more environmentally friendly | Requires careful handling of reactive gases and byproducts |
Need help choosing between PVD and CVD for your application? Contact our experts today for personalized advice!