Physical vapor deposition (PVD) is a sophisticated thin-film coating process where a solid material is vaporized in a vacuum environment and then deposited onto a substrate to form a thin, durable layer. This method is widely used across industries such as electronics, automotive, medical devices, and decorative products due to its ability to produce coatings with excellent mechanical, optical, chemical, and electronic properties. PVD is categorized based on the technique used to convert the solid material into vapor, and it is particularly valued for its ability to create high-quality, reflective coatings without the need for additional polishing.
Key Points Explained:
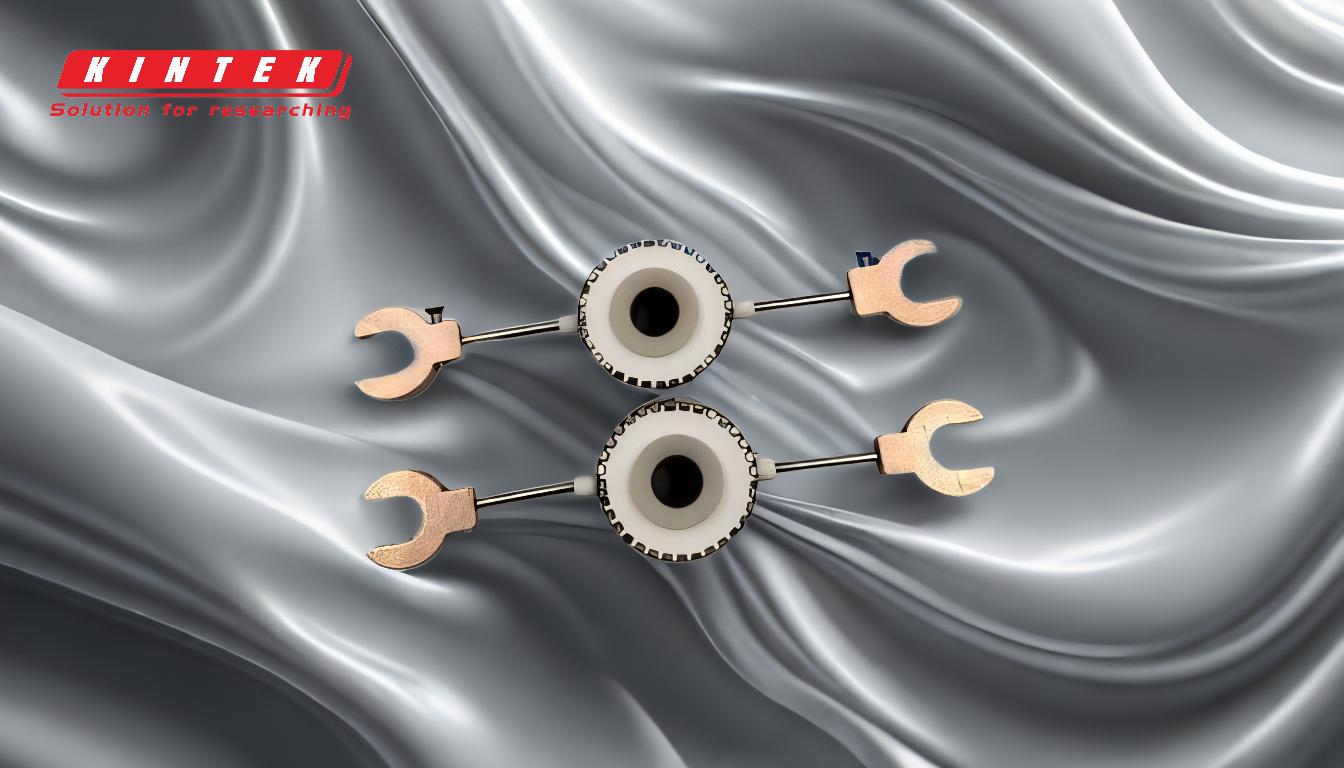
-
Definition and Process of PVD:
- PVD involves converting a solid target material into a vapor phase within a vacuum environment. The vaporized material then condenses onto a substrate, forming a thin film that is only a few atoms thick.
- The process ensures that the atoms or molecules reach the substrate without colliding with residual gas molecules, resulting in a high-quality coating.
-
Categories of PVD:
- PVD is divided into different categories based on the method used to convert the solid material into vapor. Common techniques include sputtering, evaporation, and ion plating.
- Each technique has specific applications and advantages, depending on the desired properties of the coating.
-
Applications of PVD:
- Electronics and Semiconductors: PVD is used to manufacture semiconductor devices, thin-film solar panels, and electronic packaging, where precise and durable coatings are essential.
- Decorative Products: The technology is widely used in the production of jewelry, door and window hardware, kitchen and bathroom fixtures, and other decorative items, providing a high-quality metallic finish without the need for polishing.
- Automotive and Medical Devices: PVD coatings are applied to automotive parts and medical devices to enhance durability, corrosion resistance, and aesthetic appeal.
-
Advantages of PVD Coatings:
- Durability: PVD coatings are highly durable and resistant to wear, making them ideal for applications that require long-lasting performance.
- Aesthetic Quality: The coatings provide a reflective, metallic luster that enhances the appearance of the product without additional finishing processes.
- Versatility: PVD can be used to deposit a wide range of materials, including metals, alloys, and ceramics, making it suitable for diverse applications.
-
Industrial Significance:
- PVD technology plays a critical role in modern manufacturing, enabling the production of high-performance coatings that meet stringent mechanical, optical, and chemical requirements.
- Its ability to produce thin, uniform films makes it indispensable in industries such as electronics, optics, and decorative arts.
By understanding the principles and applications of PVD, manufacturers can leverage this technology to enhance the performance and aesthetics of their products, ensuring they meet the demands of various industries.
Summary Table:
Aspect | Details |
---|---|
Definition | Converts solid material into vapor in a vacuum, depositing it as a thin film. |
Categories | Sputtering, evaporation, ion plating. |
Applications | Electronics, decorative products, automotive, medical devices. |
Advantages | Durable, reflective, versatile, and high-quality coatings. |
Industrial Significance | Essential for high-performance coatings in modern manufacturing. |
Discover how PVD can transform your products—contact our experts today!