Pressure-assisted sintering is a specialized form of sintering that combines heat with external pressure to enhance the densification and bonding of powdered materials. Unlike traditional sintering, which relies primarily on heat to promote atomic diffusion, pressure-assisted sintering applies additional mechanical force to accelerate the process, improve material density, and achieve superior mechanical properties. This method is particularly useful for materials that are difficult to sinter using conventional methods, such as ceramics and high-performance alloys. By integrating pressure, the process reduces porosity, enhances grain bonding, and produces components with higher strength and durability.
Key Points Explained:
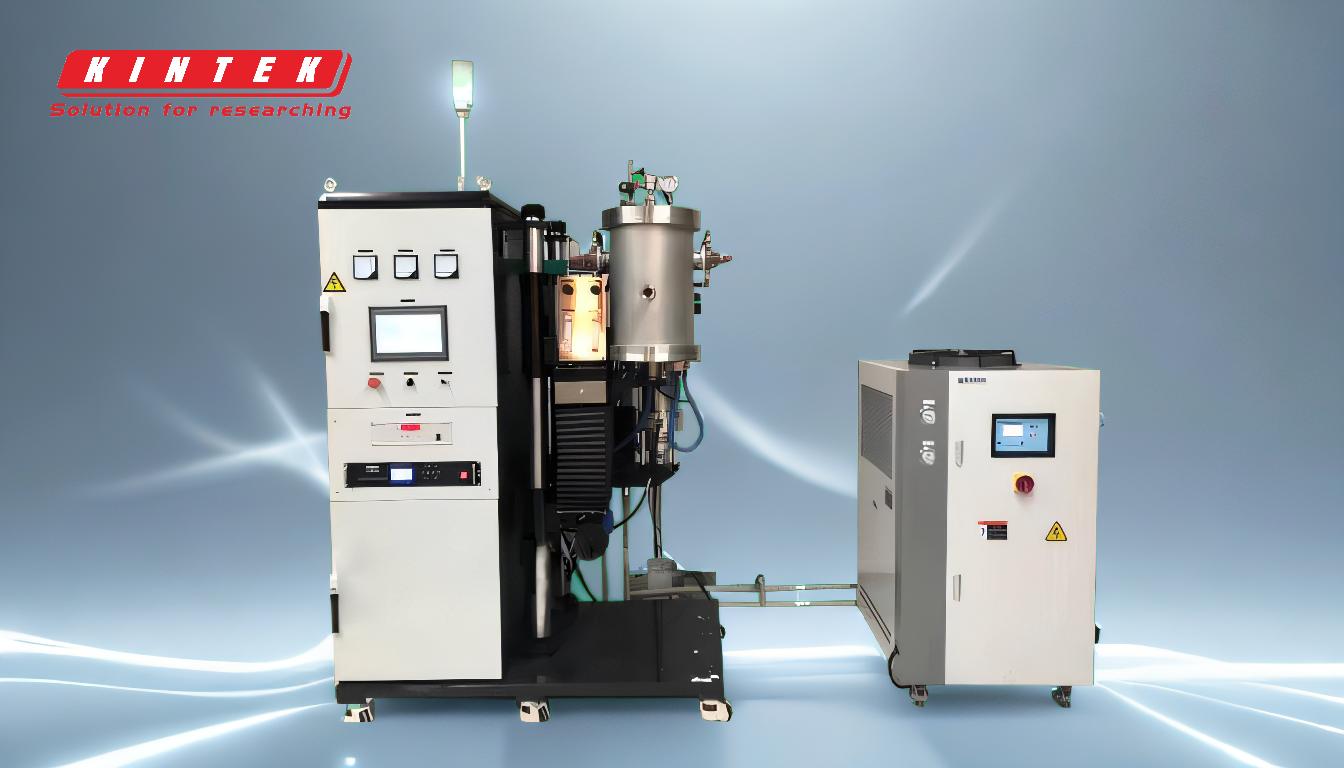
-
Definition of Pressure-Assisted Sintering:
- Pressure-assisted sintering is a manufacturing technique that applies both heat and external pressure to consolidate powdered materials into a dense, solid structure. The combination of these forces accelerates atomic diffusion and reduces porosity, resulting in a stronger and more durable final product.
-
How It Differs from Traditional Sintering:
- Traditional sintering relies solely on heat to promote atomic diffusion and particle bonding. In contrast, pressure-assisted sintering introduces mechanical pressure, which compacts the material more effectively, leading to higher density and improved mechanical properties.
-
Key Components of the Process:
- Heat: Applied to raise the temperature of the material, facilitating atomic diffusion and particle bonding.
- Pressure: Externally applied force that compacts the material, reducing voids and enhancing densification.
- Atmosphere Control: Often conducted in controlled environments (e.g., vacuum or inert gas) to prevent oxidation or contamination.
-
Advantages of Pressure-Assisted Sintering:
- Enhanced Density: The application of pressure reduces porosity, resulting in a denser and more uniform material.
- Improved Mechanical Properties: Higher density leads to better strength, hardness, and wear resistance.
- Faster Processing: The combination of heat and pressure accelerates the sintering process compared to traditional methods.
- Versatility: Suitable for a wide range of materials, including ceramics, metals, and composites.
-
Applications of Pressure-Assisted Sintering:
- Ceramics: Used to produce high-performance ceramic components with superior strength and thermal stability.
- Powder Metallurgy: Commonly employed in the production of metal parts, such as gears, bearings, and cutting tools.
- Advanced Materials: Ideal for sintering materials with high melting points or those that are difficult to densify using conventional methods.
-
Types of Pressure-Assisted Sintering:
- Hot Pressing: Combines heat and uniaxial pressure in a die to achieve densification. Commonly used for ceramics and composites.
- Hot Isostatic Pressing (HIP): Applies heat and uniform pressure from all directions using a gas medium. Suitable for complex shapes and high-performance alloys.
- Spark Plasma Sintering (SPS): Uses pulsed electric current and pressure to rapidly sinter materials, often at lower temperatures and shorter times.
-
Challenges and Considerations:
- Equipment Cost: Pressure-assisted sintering requires specialized equipment, such as hot presses or HIP systems, which can be expensive.
- Process Control: Precise control of temperature, pressure, and atmosphere is critical to achieving consistent results.
- Material Limitations: Not all materials are suitable for pressure-assisted sintering, particularly those that are sensitive to high pressure or temperature.
-
Future Trends:
- Nanomaterials: Increasing use of pressure-assisted sintering for consolidating nanostructured materials, which require precise control over particle bonding.
- Additive Manufacturing Integration: Combining pressure-assisted sintering with 3D printing techniques to produce complex, high-performance components.
- Sustainability: Development of energy-efficient sintering methods to reduce environmental impact.
By leveraging the combined effects of heat and pressure, pressure-assisted sintering offers a powerful solution for producing high-quality materials with exceptional properties. Its applications span a wide range of industries, from aerospace to biomedical engineering, making it a critical process in modern manufacturing.
Summary Table:
Aspect | Details |
---|---|
Definition | Combines heat and external pressure to densify powdered materials. |
Key Components | Heat, pressure, and controlled atmosphere. |
Advantages | Enhanced density, improved mechanical properties, faster processing. |
Applications | Ceramics, powder metallurgy, advanced materials. |
Types | Hot pressing, hot isostatic pressing (HIP), spark plasma sintering (SPS). |
Challenges | High equipment cost, precise process control, material limitations. |
Future Trends | Nanomaterials, additive manufacturing integration, sustainability. |
Unlock the potential of pressure-assisted sintering for your materials—contact our experts today!