Pressure-assisted sintering is a specialized sintering process that combines heat with external pressure to enhance the densification and bonding of powdered materials. Unlike conventional sintering, which relies solely on heat to achieve particle bonding, pressure-assisted sintering applies additional mechanical pressure to accelerate the process, reduce porosity, and improve the mechanical properties of the final product. This method is particularly useful for materials that are difficult to sinter under normal conditions, such as ceramics and high-performance alloys. By applying pressure, the process achieves higher densities and better material integrity at lower temperatures compared to traditional sintering methods.
Key Points Explained:
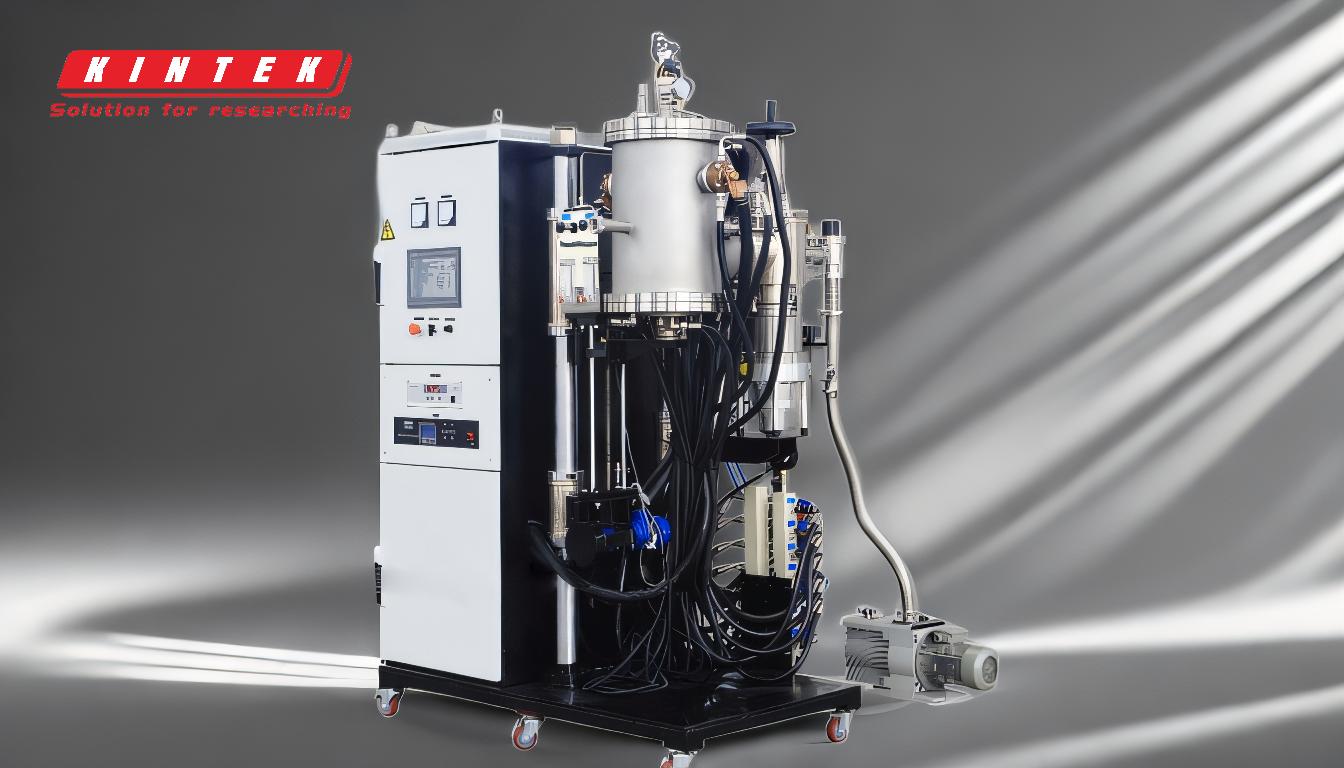
-
Definition and Purpose of Pressure-Assisted Sintering:
- Pressure-assisted sintering is a process that combines heat and external pressure to densify and bond powdered materials.
- The primary goal is to reduce porosity, enhance material density, and improve mechanical properties such as strength, toughness, and wear resistance.
- This method is especially beneficial for materials that are challenging to sinter under standard conditions, such as ceramics, refractory metals, and advanced composites.
-
Mechanism of Pressure-Assisted Sintering:
- During the process, the powdered material is heated to a temperature below its melting point, similar to conventional sintering.
- Simultaneously, external pressure is applied to compress the powder particles, promoting faster densification and stronger interparticle bonding.
- The combination of heat and pressure accelerates atomic diffusion, reduces sintering time, and minimizes grain growth, resulting in a finer microstructure.
-
Types of Pressure-Assisted Sintering:
- Hot Pressing: A common form of pressure-assisted sintering where the powder is heated and pressed simultaneously in a die. This method is widely used for ceramics and advanced materials.
- Hot Isostatic Pressing (HIP): Involves applying uniform pressure from all directions using a gas (e.g., argon) in a high-pressure vessel. HIP is ideal for producing near-net-shape components with minimal defects.
- Spark Plasma Sintering (SPS): Uses pulsed electric current and uniaxial pressure to achieve rapid sintering. SPS is known for its ability to sinter materials at lower temperatures and shorter times compared to conventional methods.
-
Advantages of Pressure-Assisted Sintering:
- Enhanced Densification: The application of pressure significantly reduces porosity, leading to higher density and better mechanical properties.
- Lower Sintering Temperatures: Pressure-assisted sintering allows for densification at lower temperatures, which is beneficial for materials prone to thermal degradation.
- Improved Microstructure: The process results in a finer and more uniform grain structure, enhancing material performance.
- Versatility: Suitable for a wide range of materials, including ceramics, metals, and composites.
-
Applications of Pressure-Assisted Sintering:
- Ceramics: Used to produce high-performance ceramic components for aerospace, automotive, and biomedical applications.
- Refractory Metals: Ideal for sintering tungsten, molybdenum, and other refractory metals used in high-temperature environments.
- Advanced Composites: Enables the production of composite materials with tailored properties for specific applications.
- Additive Manufacturing: Pressure-assisted sintering techniques like SPS are increasingly used in 3D printing to produce dense and complex parts.
-
Comparison with Conventional Sintering:
- Conventional sintering relies solely on heat to achieve particle bonding, which can result in higher porosity and longer processing times.
- Pressure-assisted sintering offers faster densification, lower porosity, and improved mechanical properties due to the combined effect of heat and pressure.
- While conventional sintering is simpler and more cost-effective, pressure-assisted sintering is preferred for high-performance materials and applications requiring superior properties.
-
Challenges and Considerations:
- Equipment Cost: Pressure-assisted sintering requires specialized equipment, such as hot presses or HIP systems, which can be expensive.
- Process Complexity: The need to control both temperature and pressure adds complexity to the process, requiring precise monitoring and optimization.
- Material Limitations: Not all materials are suitable for pressure-assisted sintering, and some may require specific conditions to achieve desired results.
In summary, pressure-assisted sintering is a powerful technique that leverages both heat and pressure to produce high-density, high-performance materials. Its ability to achieve superior properties at lower temperatures makes it a valuable process for advanced manufacturing and materials science. However, the higher equipment costs and process complexity must be carefully considered when selecting this method for specific applications.
Summary Table:
Aspect | Details |
---|---|
Definition | Combines heat and pressure to densify and bond powdered materials. |
Key Benefits | Higher density, lower porosity, improved strength, and finer microstructure. |
Types | Hot Pressing, Hot Isostatic Pressing (HIP), Spark Plasma Sintering (SPS). |
Applications | Ceramics, refractory metals, advanced composites, additive manufacturing. |
Advantages | Lower sintering temperatures, enhanced densification, and material versatility. |
Challenges | High equipment costs, process complexity, and material limitations. |
Ready to enhance your material performance with pressure-assisted sintering? Contact our experts today to learn more!