Protective atmosphere heat treatment is a specialized process used to alter the physical and chemical properties of materials, such as metals, by heating them in a controlled environment. This environment is devoid of reactive gases like oxygen, which can cause oxidation or other undesirable reactions. The process involves purging the furnace of its existing atmosphere and replacing it with an inert or reducing gas, such as nitrogen, argon, or hydrogen. This ensures that the material being treated does not react with the surrounding atmosphere, preserving its integrity and enhancing its properties. Two main types of furnaces are used: those that seal the gas inside and those that use a retort to contain the protective atmosphere.
Key Points Explained:
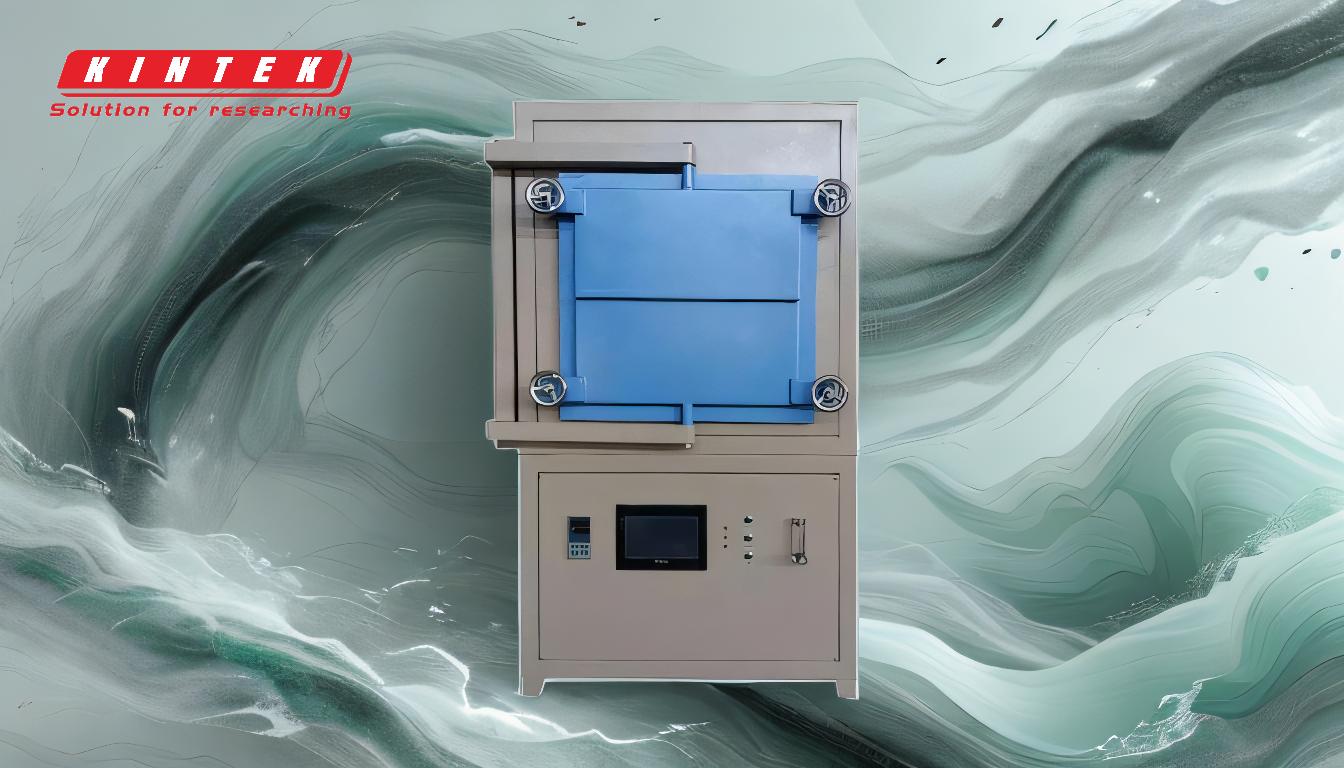
-
Purpose of Protective Atmosphere Heat Treatment:
- The primary goal of this process is to prevent oxidation, decarburization, and other surface reactions that can degrade the material's quality.
- It is particularly important for materials that are sensitive to oxygen or other reactive gases, such as certain metals and alloys.
-
Types of Protective Atmospheres:
- Inert Gases: Gases like nitrogen and argon are commonly used because they do not react with the material being treated.
- Reducing Gases: Hydrogen is often used in reducing atmospheres to remove oxygen from the surface of the material, preventing oxidation.
-
Furnace Types:
- Sealed Furnaces: These furnaces are designed to completely seal the protective gas inside, ensuring that no external atmosphere can enter. This is ideal for processes that require a very high level of atmospheric control.
- Retort Furnaces: These use a retort, which is a sealed container placed inside the furnace. The retort holds the protective atmosphere around the material, allowing for more flexible and controlled heat treatment processes.
-
Process Steps:
- Purging: The existing atmosphere in the furnace is removed by purging it with the desired protective gas.
- Heating: The material is heated to the required temperature in the protective atmosphere.
- Cooling: After the desired reactions have occurred, the material is cooled, often still within the protective atmosphere to prevent any post-treatment reactions.
-
Applications:
- Metallurgy: Used extensively in the heat treatment of metals to improve hardness, strength, and durability.
- Ceramics and Composites: Protective atmospheres are also used in the treatment of ceramics and composite materials to prevent surface degradation.
-
Advantages:
- Surface Quality: Maintains or improves the surface quality of the material by preventing oxidation and other surface reactions.
- Material Properties: Enhances the material's mechanical properties, such as hardness and strength, without compromising its integrity.
- Consistency: Provides a consistent and controlled environment, leading to more predictable and repeatable results.
-
Challenges:
- Cost: The use of specialized gases and equipment can be expensive.
- Complexity: The process requires precise control of the atmosphere and temperature, which can be technically challenging.
Protective atmosphere heat treatment is a critical process in materials science, offering significant benefits in terms of material quality and performance. However, it requires careful control and specialized equipment to achieve the desired outcomes.
Summary Table:
Aspect | Details |
---|---|
Purpose | Prevents oxidation, decarburization, and surface reactions to maintain material quality. |
Protective Atmospheres | Inert gases (nitrogen, argon) and reducing gases (hydrogen) for controlled environments. |
Furnace Types | Sealed furnaces (complete gas sealing) and retort furnaces (flexible atmosphere control). |
Process Steps | Purging, heating, and cooling within the protective atmosphere. |
Applications | Metallurgy (hardness, strength) and ceramics/composites (surface protection). |
Advantages | Improved surface quality, enhanced mechanical properties, and consistent results. |
Challenges | High cost and technical complexity due to precise control requirements. |
Discover how protective atmosphere heat treatment can optimize your material processing—contact our experts today!