Physical Vapor Deposition (PVD) is a thin-film deposition technique used to create highly precise and uniform coatings on various substrates. It involves the physical transfer of material from a solid source to a substrate in a vacuum environment. PVD is widely used in industries such as electronics, optics, and cutting tools due to its ability to produce durable, high-quality thin films. In contrast, Chemical Vapor Deposition (CVD), including advanced methods like microwave plasma chemical vapor deposition, relies on chemical reactions to deposit thin films. Both PVD and CVD have evolved significantly since their early development, as documented in the 1966 book Vapor Deposition by Powell, Oxley, and Blocher.
Key Points Explained:
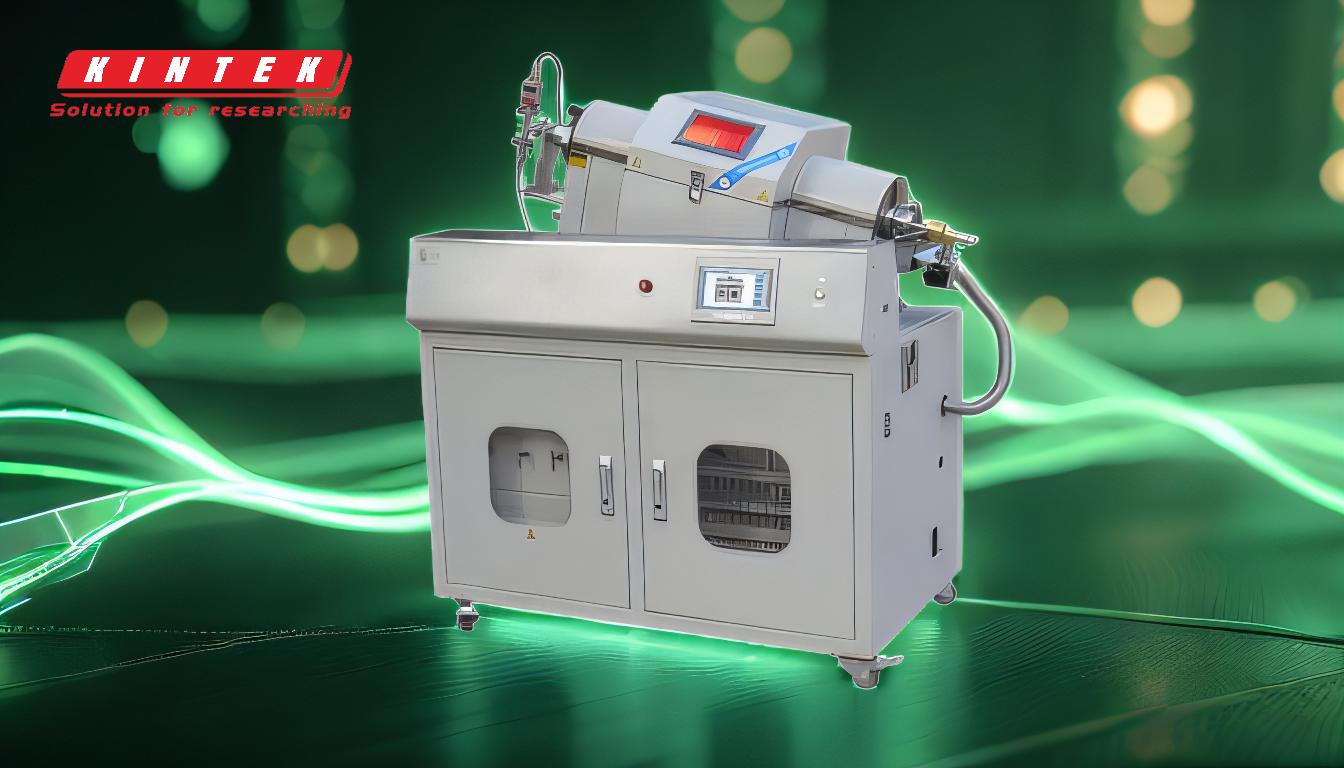
-
Definition and Process of PVD:
- PVD is a vacuum-based process where a solid material is vaporized and then condensed onto a substrate to form a thin film.
- Common PVD methods include sputtering, evaporation, and ion plating.
- Sputtering, a widely used PVD technique, involves bombarding a target material with ions to eject atoms, which then deposit onto the substrate.
-
Applications of PVD:
- PVD is used in industries such as electronics, optics, and cutting tools.
- It is ideal for creating high-temperature coatings, conductive coatings for SEM specimens, and coatings for heat-sensitive materials like plastics or biological samples.
- PVD coatings enhance properties like wear resistance, corrosion resistance, and electrical conductivity.
-
Comparison with CVD:
- CVD involves chemical reactions to deposit thin films, often requiring high temperatures and specialized precursors.
- Unlike PVD, CVD can grow complex structures like carbon nanotubes and GaN nanowires.
- CVD is used in electronics for semiconductor thin films, in cutting tools for wear-resistant coatings, and in solar cell manufacturing for photovoltaic materials.
-
Historical Development:
- The techniques of PVD and CVD were first documented in the 1966 book Vapor Deposition by Powell, Oxley, and Blocher.
- This book highlighted the early applications of these methods in creating thin films for various industries.
-
Advantages of PVD:
- PVD produces highly uniform and precise thin films with excellent adhesion to the substrate.
- It operates at lower temperatures compared to CVD, making it suitable for heat-sensitive materials.
- PVD coatings are durable and can be tailored to achieve specific functional properties.
-
Industrial Relevance:
- PVD and CVD are integral to modern manufacturing and supply chains.
- They enable the production of advanced materials and coatings that are critical for technological advancements in electronics, renewable energy, and materials science.
By understanding the principles and applications of PVD and CVD, manufacturers can choose the appropriate technique based on their specific requirements, ensuring optimal performance and quality of thin-film products.
Summary Table:
Aspect | Details |
---|---|
Definition | Vacuum-based process for depositing thin films via physical material transfer. |
Common Methods | Sputtering, evaporation, ion plating. |
Applications | Electronics, optics, cutting tools, SEM specimens, heat-sensitive materials. |
Advantages | Uniform coatings, lower temperatures, durable, tailored functional properties. |
Comparison with CVD | PVD: Physical transfer; CVD: Chemical reactions, higher temperatures. |
Historical Context | Documented in Vapor Deposition (1966) by Powell, Oxley, and Blocher. |
Discover how PVD can enhance your thin-film applications—contact us today for expert guidance!