Physical Vapor Deposition (PVD) is a sophisticated thin-film coating technology used to deposit materials onto a substrate in a vacuum environment. The process involves converting solid precursor materials into a gaseous state through physical means such as thermal evaporation, sputtering, or laser ablation. These vaporized atoms, molecules, or ions then travel through the vacuum chamber and condense onto the substrate, forming a thin, uniform coating. PVD is widely used to create highly durable, corrosion-resistant, and temperature-tolerant coatings, with applications ranging from electronics to aerospace. The process is highly controllable, allowing for precise thickness and composition of the deposited films, typically ranging from 1 to 10 micrometers.
Key Points Explained:
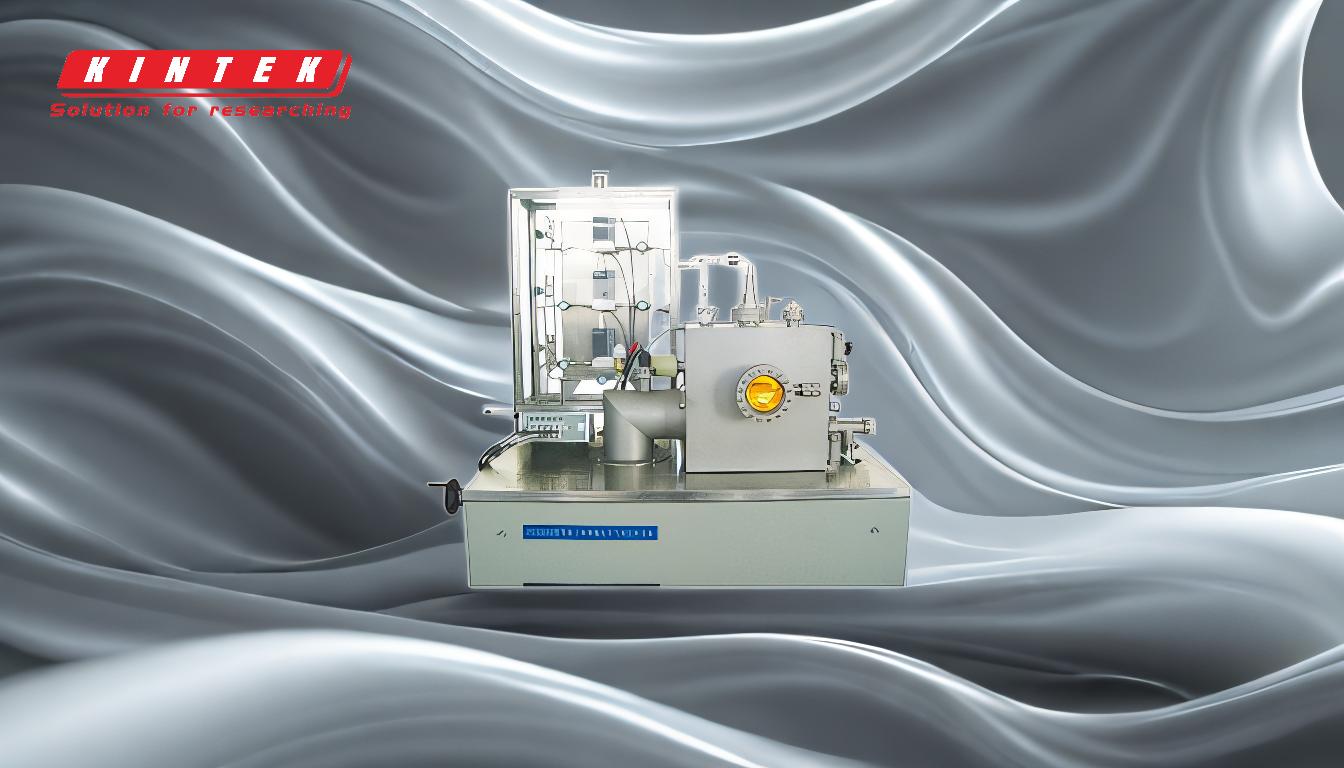
-
Definition and Overview of PVD:
- PVD is a thin-film deposition process that involves converting solid materials into a gaseous state and then depositing them onto a substrate in a vacuum environment. This process is used to create coatings of pure metals, metallic alloys, and ceramics.
-
Key Steps in the PVD Process:
- Vaporization: The solid precursor material is vaporized using methods such as thermal evaporation, sputtering, or laser ablation.
- Transport: The vaporized atoms, molecules, or ions travel through the vacuum chamber to the substrate.
- Deposition: The vaporized material condenses onto the substrate, forming a thin, uniform coating.
-
Methods of Vaporization:
- Thermal Evaporation: The solid material is heated until it vaporizes.
- Sputtering: A high-energy plasma is used to dislodge atoms from the target material, which then deposit onto the substrate.
- Laser Ablation: A high-power laser is used to vaporize the material.
-
Vacuum Environment:
- The PVD process is carried out in a vacuum chamber to minimize the presence of background gases, which could otherwise react with the vaporized material and affect the quality of the coating.
-
Control and Monitoring:
- The thickness and rate of the deposited film are controlled using advanced monitoring techniques, such as quartz crystal rate monitors. This ensures precise control over the coating's properties.
-
Applications of PVD:
- PVD coatings are used in a wide range of industries, including electronics, aerospace, automotive, and medical devices. The coatings provide enhanced durability, corrosion resistance, and thermal stability.
-
Advantages of PVD:
- Durability: PVD coatings are highly durable and resistant to wear and corrosion.
- Precision: The process allows for precise control over the thickness and composition of the coatings.
- Versatility: PVD can be used to deposit a wide variety of materials, including metals, alloys, and ceramics.
-
Challenges and Considerations:
- Cost: The equipment and materials used in PVD can be expensive.
- Complexity: The process requires a high level of technical expertise and precise control over the deposition parameters.
- Substrate Compatibility: Not all substrates are suitable for PVD, and surface preparation is often required to ensure proper adhesion of the coating.
-
Future Trends in PVD:
- Nanotechnology: Advances in PVD technology are enabling the deposition of nanosized thin films, which have applications in nanotechnology and advanced electronics.
- Sustainability: There is a growing focus on developing more environmentally friendly PVD processes and materials.
In summary, Physical Vapor Deposition (PVD) is a versatile and precise thin-film coating technology that offers numerous advantages in terms of durability, precision, and versatility. Despite its challenges, PVD continues to be a critical technology in various high-tech industries, with ongoing advancements paving the way for new applications and improved performance.
Summary Table:
Aspect | Details |
---|---|
Definition | Thin-film deposition process in a vacuum environment. |
Key Steps | Vaporization, Transport, Deposition. |
Vaporization Methods | Thermal Evaporation, Sputtering, Laser Ablation. |
Applications | Electronics, Aerospace, Automotive, Medical Devices. |
Advantages | Durability, Precision, Versatility. |
Challenges | High cost, technical complexity, substrate compatibility. |
Future Trends | Nanotechnology, Sustainability. |
Discover how PVD can enhance your projects—contact our experts today!