Physical Vapor Deposition (PVD) is a versatile and widely used technology in various industries, including manufacturing, decorative products, and tool enhancement. PVD involves the deposition of thin films onto substrates through the vaporization of source materials in a vacuum environment. This process enhances product characteristics such as durability, wear resistance, and aesthetic appeal, often at a lower cost and with minimal environmental impact. PVD is particularly valuable in applications like durable-decorative coatings, performance coatings, and alternatives to traditional chrome plating. The process can be achieved through methods like thermal evaporation, where materials are heated to form a vapor that condenses on the substrate, creating a high-quality coating.
Key Points Explained:
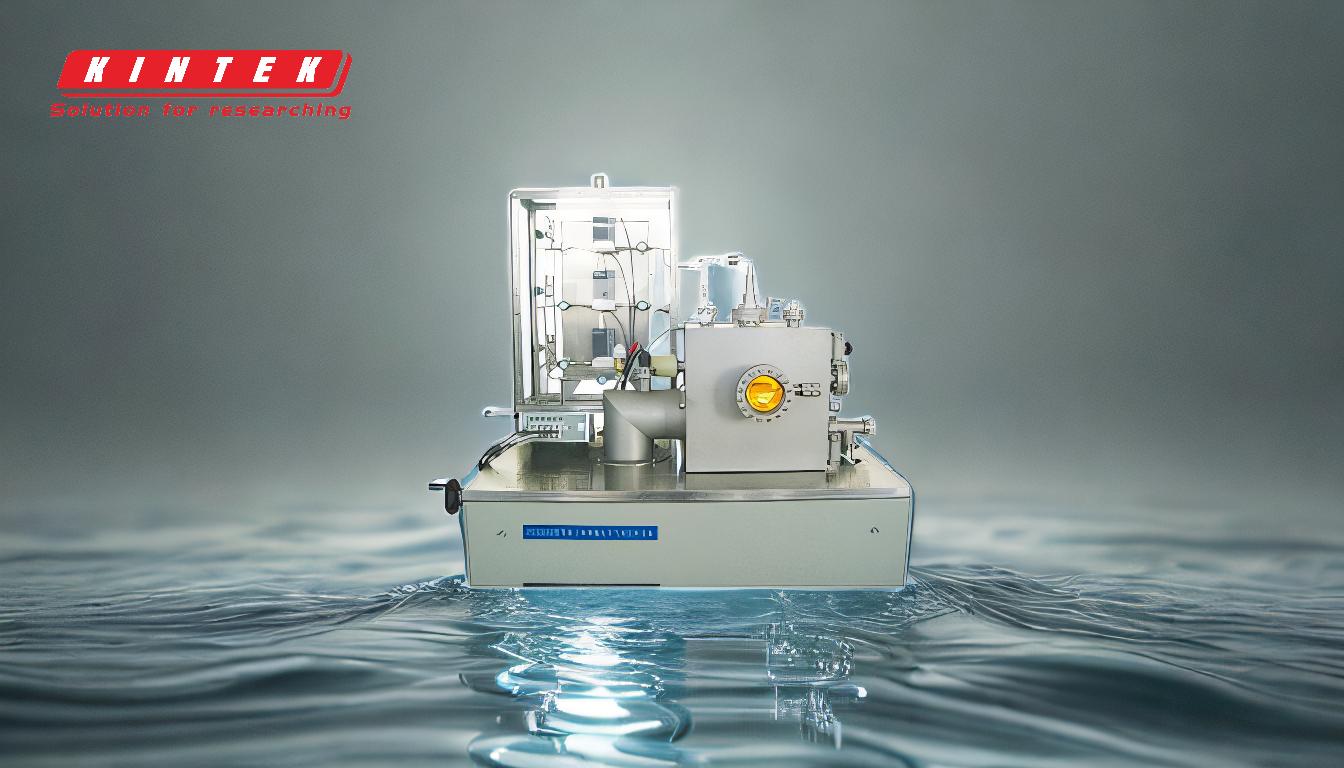
-
What is PVD?
- PVD, or Physical Vapor Deposition, is a coating process where materials are vaporized in a vacuum and then deposited onto a substrate to form a thin film. This technology is widely used to enhance the properties of products, such as wear resistance, durability, and aesthetic appeal.
-
Applications of PVD:
- PVD is used in a variety of industries, including:
- Jewelry and Decorative Products: Enhances the appearance and durability of items like jewelry, door hardware, and kitchen fixtures.
- Industrial Tools: Improves the wear resistance of cutting tools and reduces adhesion between tools and workpieces, particularly in metalworking and plastic injection molding.
- Performance Coatings: Includes diamond-like carbon coatings and PVD chrome alternatives, which are used for their durability and environmental benefits.
- PVD is used in a variety of industries, including:
-
PVD Coating Benefits:
- Cost-Effectiveness: PVD coatings are often more affordable than traditional plating methods like chrome.
- Environmental Impact: PVD processes are generally more environmentally friendly, producing fewer harmful byproducts.
- Enhanced Properties: Coatings improve hardness, wear resistance, and corrosion resistance, extending the lifespan of products.
-
PVD Techniques:
-
Thermal Evaporation: One of the most common PVD methods, where the source material is heated in a vacuum until it vaporizes. The vapor then condenses on the substrate to form a coating. Heating methods include:
- Hot filament
- Electrical resistance
- Electron or laser beam
- Electric arc
- High-Vacuum Environment: The process occurs in a vacuum to minimize interference from gas atoms or molecules, ensuring a high-quality coating.
-
Thermal Evaporation: One of the most common PVD methods, where the source material is heated in a vacuum until it vaporizes. The vapor then condenses on the substrate to form a coating. Heating methods include:
-
Industries and Products Using PVD:
- PVD is used in the manufacturing of:
- Jewelry: For decorative and protective coatings.
- Hardware: Such as door and window fixtures, kitchen and bathroom hardware.
- Lamps and Marine Supplies: For enhanced durability and appearance.
- Handicrafts and Decorative Items: To improve aesthetic appeal and longevity.
- PVD is used in the manufacturing of:
-
Advantages Over Traditional Methods:
- PVD offers a more sustainable and efficient alternative to traditional coating methods like chrome plating. It provides similar or superior performance characteristics while reducing environmental impact and cost.
In summary, PVD is a highly effective and versatile technology used across multiple industries to enhance the performance and appearance of products. Its applications range from decorative coatings to industrial tool enhancements, offering cost-effective, durable, and environmentally friendly solutions.
Summary Table:
Aspect | Details |
---|---|
What is PVD? | Coating process using vaporized materials in a vacuum to form thin films. |
Applications | Jewelry, industrial tools, performance coatings, and decorative products. |
Benefits | Cost-effective, eco-friendly, enhances durability and wear resistance. |
Techniques | Thermal evaporation, high-vacuum environment, and various heating methods. |
Industries | Jewelry, hardware, marine supplies, handicrafts, and decorative items. |
Advantages | Sustainable, efficient, and superior to traditional chrome plating. |
Transform your products with PVD technology—contact our experts today for tailored solutions!